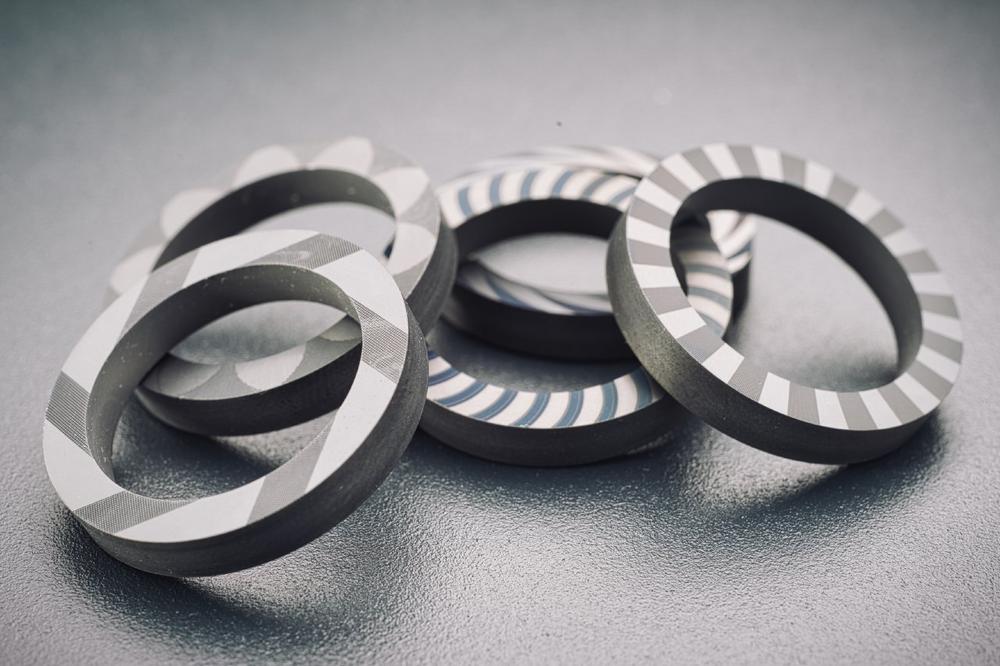
Wir geben Keramik Struktur und Form somit generieren wir neue Funktionalitäten.
Woher kommt die Motivation ?
Wir sind permanent in Zusammenarbeit mit Kunden, aber auch auf Eigeninitiative, dabei tribologische Systeme zu analysieren und zu optimieren. Gerade im Bereich der Pumpentechnik lassen sich enorme Potentiale generieren. Die Kombination der Dichtfunktion im Saugmundbereich zur Reduzierung von internen Leckagen und die Abbildung eines axialen Lagers in einer Baugruppe erhöht zum einem den hydraulischen Wirkungsgrad und kann andererseits die axialen Kräfte aufnehmen. Die Axialkraft resultiert bei rein mechanischen Pumpen aus dem hydraulischen Axialschub, bei elektrischen Pumpen ist es eine Kombination aus hydraulischen Axialschub und der axialen Kraft aus dem elektrischem Antrieb. Diese Anordnung steigert den Gesamtwirkungsgrad, verringert die Reibleistung und reduziert die Teileanzahl, da jegliche zusätzlichen axialen Lagerungssysteme überflüssig sind.
Wie setzen wir das um?
Durch das kontinuierliche Weiterentwickeln unserer Formgebungsverfahren ist dies möglich.
Die Kombination aus der hausinternen Werkstoffentwicklung, im direktem Zusammenspiel mit der Prozesslandschaft versetzen uns in die Lage hohe Genauigkeiten bereits im Urformprozess abzubilden. Somit ist es nicht mehr nötig aufwendige Hartbearbeitungsprozesse nachzuschalten. Es werden lediglich die punktuell beanspruchten Bereiche hartbearbeitet.
Wie sorgen wir für Auftrieb ?
Bei derartigen Systemen ist es notwendig anwendungsspezifisch Randbedingen einzustellen. Zum einen sollte das System schon bei niedrigen Drehzahlen in der Lage sein in der Hydrodynamik zu laufen. Die Trocken bzw. Mischreibungsanteile müssen auf ein Minimum reduziert werden. Nach dem Aufschwimmen des Systems ist es elementar wichtig das der Spaltdruck zwischen den Gleitringen entsprechend ausgelegt ist, um die axialen Kräfte aufzunehmen und die Dichtfunktion zwischen Saugseite und Druckseite zu gewährleisten. Dies wird durch speziell strukturierte Oberflächen realisiert. Wir unterscheiden grundsätzlich zwischen Mikro und – Makrostrukturen die für die notwendige Tribologie sorgen. Mikrostrukturen werden meist über Laserbearbeitung eingebracht, Makrostrukturen hingegen können direkt über den Formgebungsprozess abgebildet werden. Die entsprechend entwickelten Granulate (Feedstock) machen dies möglich. Die Auslegung derartigen Strukturen erfolgt in enger Zusammenarbeit mit Kunden und Entwicklungspartnern.
Unser mittelfristiges Ziel ist es vorhandene Systeme durch eine Substitution zu verbessern und bei Neuentwicklungen von Anfang an einzusetzen. Dies können wir sowohl für sehr kleine Stückzahlen, als auch für Großserien umsetzen.
FCT Ingenieurkeramik steht für mehr als 30 Jahre Erfahrung und Kompetenz in der Werkstofftechnik und bei der Herstellung von keramischen Hochleistungswerkstoffen und Kompositen.
Unsere Spezialität sind Siliziumnitrid- und Siliziumkarbid-basierte, nichtoxidische Keramikwerkstoffe. Mit unseren Anlagen fertigen wir daraus Bauteile in unterschiedlicher Formgebungs- und Sintertechnik, speziell nach Zeichnungen und anwendungsspezifischen Anforderungen unserer Kunden und Partner. Die komplette Prozesstrecke vom Pulver bis zur einbaufertigen Keramikkomponenten ist bei uns im Haus vorhanden.
Aus optimierten bzw. maßgeschneiderten Keramikwerkstoffen erstellen wir gerne Prototypen, Sonderbauteile und kleine bis mittlere Serien für Sie. Auch besonders große, komplexe und hochpräzise Bauteile sind dabei eher Herausforderung als Problem für uns.
Mit unseren nach modernstem Stand der Technik ausgestatteten und im täglichen Betrieb optimierten Anlagen bieten wir Ihnen zudem eine Vielzahl unterschiedlicher Dienstleistungen.
QSIL Ceramics GmbH
Triptiser Str. 22
07955 Auma
Telefon: +49 (36626) 98-0
Telefax: +49 (36626) 98-269
http://www.qsil.com/
Technical Sales & Application Engineering
Telefon: +49 (36766) 868291
E-Mail: toni.steiner@fcti.de

