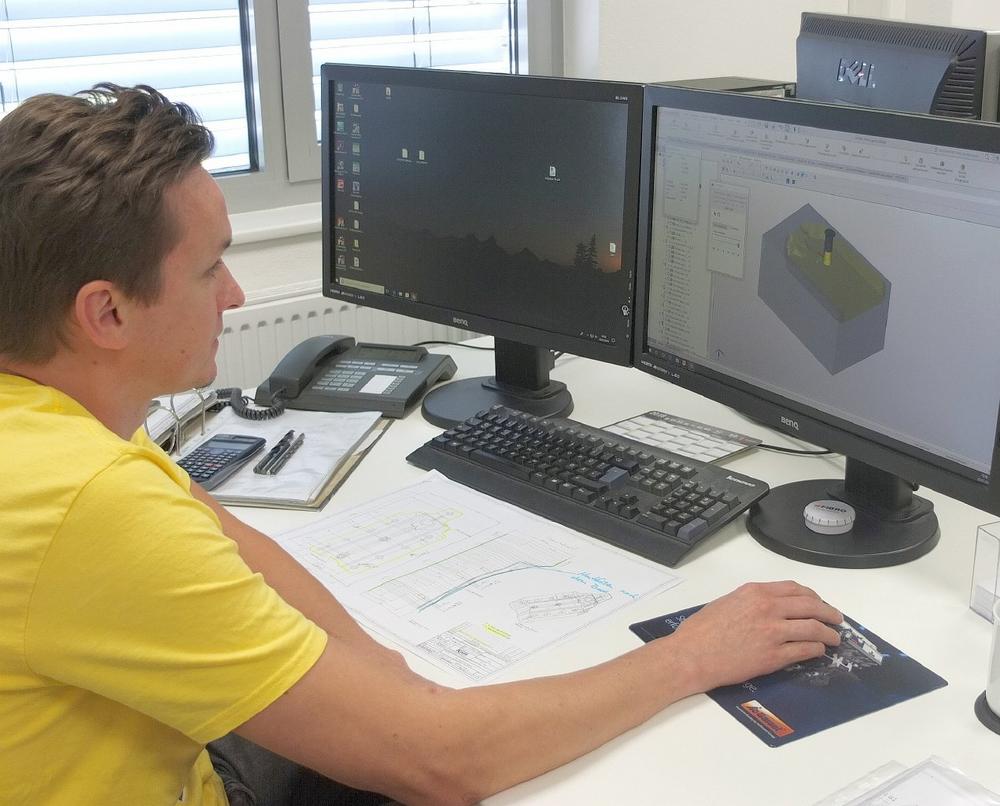
SolidCAM im Kauth Werkzeugbau: „Ohne CAM geht es nicht mehr“
Die Paul Kauth GmbH & Co. KG geht auf ein Taxi-Unternehmen mit Tankstelle und Reparaturwerkstatt, gegründet 1928 in Spaichingen, zurück. Noch der Gründer, Paul Kauth, hat das Unternehmen 1952 auf eine vollkommen neue Schiene gesetzt: Fortan wurden Drehteile und Muttern produziert. Im Jahr 1964 zog die Firma nach Denkingen, wo auch eine erste eigene Produktionshalle gebaut worden war.
Nochmals einige Jahre später gab es einen weiteren starken Bruch im Unternehmen: Weil zu viele billige Importe von Drehteilen die Preise kaputt machten, verlegte sich Kauth auf Blechumformteile. Die Zielgruppe war die Automobilindustrie. Für die großen Automobilunternehmen wurden z. B. Achsbefestigungen, Gewindeplatten, Tür- und Heckscharniere, Sitzbefestigungen oder Motor- und Getriebebefestigungen entwickelt und produziert-bis heute. Sie alle entstehen in Folgeverbundwerkzeugen, die eine ausgefeilte Werkzeugtechnik verlangen.
Eine Besonderheit des Hauses ist die Herstellung von Tuben. Hierbei ist Kauth Technologieführer, der sehr anspruchsvolle Tuben herstellen kann. Kauth schafft es, sowohl massive Tuben als auch hohe Tuben zu vereinen. Auch hierbei wird das Material kaltgezogen, wodurch hohe Festigkeiten entstehen.
Paul Kauth hat die notwendigen Werkzeuge früher komplett von außen bezogen. Mitte 2012 hat man sich dann entschlossen, einen eigenen kleinen Werkzeugbau aus einer Insolvenz heraus zu kaufen. In den Folgejahren wurde viel dort investiert und heute sind 17 Mitarbeiter beschäftigt, welche u. a. die Bereiche Werkzeugkonstruktion, NC-Programmierung und Produktion abdecken.
"Die Kauth Werkzeugbau GmbH wird als eigenständiges Unternehmen geführt, arbeitet derzeit aber zu 100% für die Muttergesellschaft", wie der Betriebsleiter Alexander Schläfle berichtet.
Die Paul Kauth GmbH & Co. KG ist unterdessen auf 550 Mitarbeiter gewachsen, verteilt auf fünf Standorte in Denkingen, Frittlingen, Deilingen, Solingen und Finnentropp. Eine sechste Niederlassung in Kanada ist derzeit in Vorbereitung.
Ein Prozess ohne Schnittstellen
Schon vor rund 10 Jahren hat sich Kauth aus strategischen Gründen – wie es heißt – für SOLIDWORKS entschieden. Da das CAM-System SolidCAM nahtlos in SOLIDWORKS integriert ist (gleicher Kern, gleiche Benutzeroberfläche, voll assoziative Verbindung von CAD-Modell und Werkzeugwegen), können die Informationen und Daten bruchlos von der Artikelkonstruktion in die CAM-Programmierung fließen und schließlich über den Postprozessor an die Maschine. „Ohne CAM ginge es nicht mehr bei uns“, betont Schläfle.
SolidCAM bietet eine Reihe von Bearbeitungsmöglichkeiten für die mechanische Zerspanung und das Erodieren:
- 2,5 D Fräsen
- 3 D Fräsen HSS
- 3 D Fräsen HSR/HSM
- Mehrseitenbearbeitung mit indexierten Achsen
- 5Achs-Simultanbearbeitung
- Drehen und
- Drehfräsen/Fräsdrehen
Dazu kommen noch:
- CIMCO DNC, NC-Verwaltung
- Drahterodieren mit DCAMCUT
- Werkzeugverwaltung über TDM und
- iMachining
Zurück zum Werkzeugbau in Frittlingen.
Was hat dort zur Entscheidung für SolidCAM geführt?
"Schon das Vorläuferunternehmen hatte SolidCAM im Einsatz. Man hat dann hier zunächst einmal damit weiter gemacht und dabei festgestellt, dass man mit dem System gut arbeiten kann", berichtet Alexander Schläfle. Wesentlich später, 2015, als man mit einer eigenen Produktion begann, wurde noch einmal grundsätzlich überlegt, ob dieses oder auch ein anderes System besser sei bezüglich zukünftiger Anforderungen.
Schläfle: "Fest stand, dass nur ein System mit SOLIDWORKS-Integration infrage käme."
Beide Seiten, sowohl die Konstrukteure als auch die NC-Programmierer, haben am Ende für das Duo, SOLIDWORKS/SolidCAM, votiert.
Schritt für Schritt zum perfekten Werkzeug.
Der Prozess beim Kauth Werkzeugbau beginnt damit, "dass die Kollegen aus Denkingen mit einem neuen Teil auf uns zukommen", so Schläfle. Neben allgemeinen Erklärungen dazu, stehen dann bereits die Geometriedaten im SOLIDWORKS-Format zur Verfügung.
Der Konstrukteur macht daraus einen Methodenplan und einen Vorschlag, wie das Streifenlayout aussehen soll. Hilfreich an der Stelle ist auch die Software Logopress, die ebenfalls in SOLIDWORKS integriert ist und von DPS geliefert wird.
Logopress unterstützt die Werkzeugkonstruktion, das Streifenlayout, die Abwicklung sowie auch die Freiformabwicklung.
Liegen die bisher angesprochenen Ergebnisse vor, wird auf dieser Basis eine Kalkulation und ein Angebot erstellt denn, wie gesagt, der Werkzeugbau ist zwar ein Teil der Kauth-Gruppe, wird aber eigenständig geführt. "Würden unsere Preise nicht stimmen, wären wir z. B. viel teurer als der Wettbewerb, bekämen wir auch den Auftrag nicht", ist sich A. Schläfle sicher.
Gibt es die Freigabe, wird das Werkzeug in SOLIDWORKS aufgebaut. Bei einem Fertigstellungsgrad von 80%, macht man erneut einen Kontrollschritt! Das bedeutet, die Auftraggeber in Denkingen erhalten die Ergebnisse und machen "eine Art Vorabnahme", wie Schläfle sagt.
Nach diesem Schritt und dem nötigen "ok" werden die Werkzeuge fertig konstruiert. Jetzt erfolgt die finale Abnahme, bei der u. a. jede einzelne Station genau angeschaut wird.
Ist der Konstruktionsprozess und die Freigabe beendet, wird noch die Zeichnungsableitung gemacht.
Dann erfolgt der Übergang in die Fertigung und SolidCAM kommt ins Spiel. Zum Zeitpunkt der Recherche zu diesem Artikel wurden zwei CAM-Arbeitsplätze betrieben. Mittlerweile sind 5 Lizenzen installiert (3 für die Konstruktion und 2 für das CAM-Fräsen).
Wenn der NC-Programmierer nun mit seiner Arbeit beginnt, muss er nicht irgendwelche Übertragungsmaßnahmen durchführen oder sonst etwas, sondern er klickt einfach den Button "CAM" an, alle nötigen Arbeitsleisten erscheinen und es geht unmittelbar los!
Ebenfalls positiv für die Performance wirkt sich die Tatsache aus, dass alle Maschinen und Werkzeuge in Bibliotheken hinterlegt sind. Der Bediener zieht sie einfach in die Arbeitsebene und setzt sie ein.
Das geht nicht nur schnell, sondern erlaubt hernach auch eine vollständige Simulation: Tisch im Weg, Halter im Weg, Schraubstock im Weg usw., alles kommt bei der Simulation heraus: "Spätestens beim 5Achs-Fräsen muss simuliert werden. Die möglichen Bewegungen sind so komplex, dass sie nicht mehr vom Bediener übersehen werden können", wie Schläfle weiß.
SolidCAM wird beim Kauth Werkzeugbau hauptsächlich für die Programmversorgung von Hermle Bearbeitungszentren eingesetzt. Bearbeitungsarten: Fräsen und Bohren. Die Postprozessoren macht DPS, so dass die Daten problemlos bis zur Maschine weiterfließen.
Die am Ende resultierenden Genauigkeiten "reichen aus", wie der Betriebsleiter versichert, um auch die anspruchsvollen Werkzeugteile sicher zu bearbeiten.
Schruppen im Gleichlauf
Seit einigen Jahren bieten CAM-Hersteller spezielle Programme für die Schruppbearbeitung im Gleichlauffräsen an. Eines dieser Pakete ist iMachining von SolidCAM.
iMachining ist ein automatischer CNC-Programmgenerator zum Hochgeschwindigkeitsfräsen, für das Schruppen, Restmaterialschruppen und Grobschlichten von prismatischen und flächig geformten 3D-Teilen.
Die Software nutzt die 3D-Rohmodelldaten und die CAD-Geometrie des Fertigteils für die Eingabe. Den Rest macht das System selbst. Das geht aber nur durch in der Datenbank hinterlegte Angaben: Dazu gehören die Werkzeugdaten, die Materialdaten (viele sind schon im System vorgehalten, andere können ergänzt werden) und die Maschinendaten. Aus allen diesen Angaben erstellt iMachining ein Hochgeschwindigkeits-CNC-Programm. Der innovative Algorithmus des Systems sorgt dafür, dass immer das gleiche Spanvolumen pro Fräszahn abgetragen wird. Somit wird das Werkzeug optimal ausgelastet, aber nicht überlastet und es entsteht ein insgesamt sehr großes Spanvolumen pro Zeiteinheit.
Am Ende des Verfahrens, das hier nur grob geschildert ist, steht eine Zeitersparnis, die im Durchschnitt mit 70% angegeben wird. Natürlich hängt der Wert aber von den jeweiligen Aufgaben ab.
Neben der Zeitersparnis steht die Werkzeugschonung im Mittelpunkt, welche gerade bei schwer zerspanbaren Materialien zu deutlichen Standzeiterhöhungen führt (um das 2- bis 3-fache, wie die Erfahrung zeigt).
Kauth Werkzeugbau nutzt diese Software ebenfalls, jedoch nicht flächendeckend. "Wir nutzen für das schnelle Schruppen auch so genannte Hochvorschubfräser, die ebenfalls sehr produktiv sind und eine Alternative darstellen", weiß Schläfle. Welche Art des Schruppens zum Tagen kommt, entscheidet der CAM-Programmierer nach seiner Erfahrung.
Am Ende beteuern die Zerspanungsfachleute in Frittlingen, dass sie mit SolidCAM rund herum zufrieden sind, wie auch mit der Betreuung durch DPS. Nochmals Betriebsleiter Schläfle: "Es ist von großem Vorteil, dass DPS so servicestark ist. Wenn wir Hilfe brauchen, erhalten wir diese sehr schnell, innerhalb von Stunden. Wenn wir neue Maschinen bekommen, kümmert sich DPS vorbildlich um die Postprozessoren, so dass wir sehr bald in Produktion gehen können."
Die DPS Software wurde 1997 gegründet und ist heute der größte selbstständige SOLIDWORKS Reseller in Europa und der größte Sage-Reseller in D-A-CH. Exklusiv vertreibt DPS die ERP Software RPS im deutschsprachigen Raum. Neben den Produkten von SOLIDWORKS hat DPS die CAM-Produkte von SolidCAM im Portfolio. Hinzu kommen DPS eigene Module und Lösungen.
Für die Möbelbranche vertreibt DPS in Zentraleuropa die Softwarelösung SWOOD auf Basis von SOLIDWORKS.
Das Unternehmen hat 40 Standorte in Deutschland, Österreich, der Schweiz, Polen und Tschechien und beschäftigt 600 Mitarbeiter.
Unterstützt werden über 11.000 Kunden in der gesamten Prozesskette von der Konstruktion, über die Berechnung und Fertigung bis hin zur Datenverwaltung und der Abbildung der damit verbundenen kaufmännischen Prozesse. Software- und Schnittstellenentwicklungen sowie Schulungs- und Beratungs-dienstleistungen vervollständigen die kundenorientierte Ausrichtung.
http://www.dps-software.de/
DPS Software GmbH
Epplestraße 225 | Haus 5
70567 Stuttgart
Telefon: +49 (711) 797310-0
Telefax: +49 (711) 797310-29
http://www.dps-software.de

