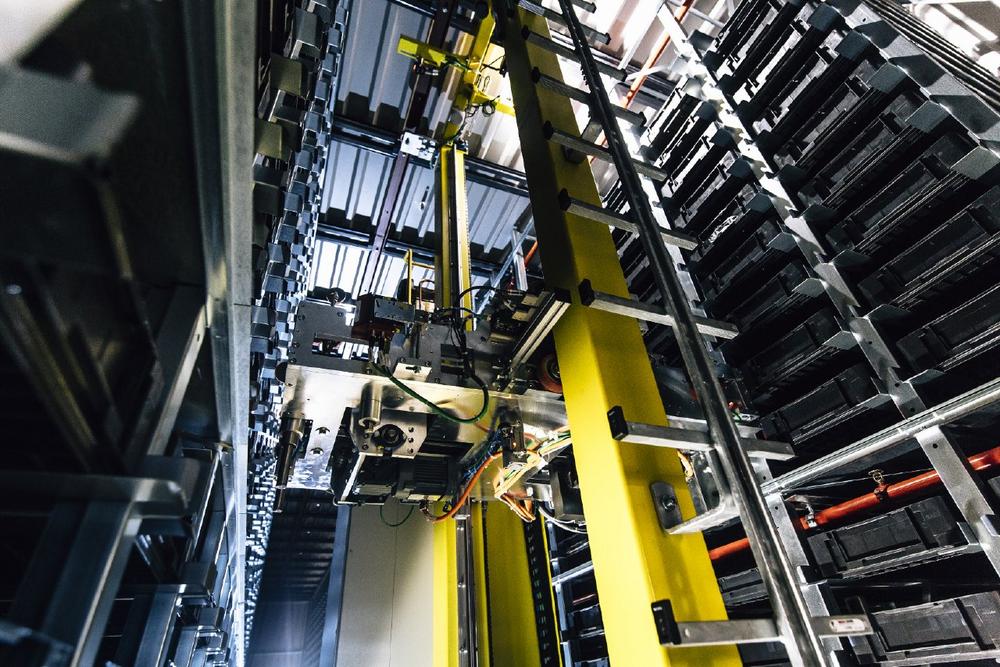
Alles auf Lager für Ihren Schrank
Das Unternehmen Hettich wurde 1888 gegründet und ist heute einer der weltweit größten Hersteller von Möbelbeschlägen. Mehr als 6.700 Mitarbeiterinnen und Mitarbeiter in fast 80 Ländern entwickeln und produzieren intelligente Technik für Möbel. Am Standort in Spenge (Nordrhein-Westfalen) werden Dämpfungssysteme und Laufteile für Schranksysteme in automatischen Lagersystemen des Automatisierungsspezialisten de Man Automation + Service aus Borgholzhausen gelagert. Ziele bei der Realisierung der automatisierten Pufferlager waren das Garantieren von Produktionssicherheit durch Bestandsreserven, kurze Nachschubzeiten und ein mannloses KLT-Handling. Beide Lagersysteme sorgen inzwischen nicht nur für äußerst effiziente Lager- und reibungslose Produktionsprozesse, sondern bilden zugleich eine räumliche Trennung zwischen Produktions- und Verpackungsbereich in der Fertigungshalle.
Lager 1: Pufferlager für Dämpfungssysteme
Dieses Lager wurde als erstes Projekt realisiert und im Folgenden sowohl um eine Roboterbestückung als auch einen Anbau zur Steigerung der Lagerfläche erweitert. Es dient zum Ausgleich von Schwankungen zwischen der Produktion auf den Montageanlagen und dem Bedarf in der kundenindividuellen Verpackung. Hierzu zählen sowohl die Rüstvorgänge bei Produktwechseln, als auch die Differenz zwischen produktionsoptimierten Losgrößen und dem Kundenbedarf. Das Lager übernimmt die Bereitstellung leerer KLTs an den Montageanlagen, der Palettier-/Depalettieranlage und einem manuellen Ein- und Auslagerungsplatz ebenso wie die Einlagerung voller KLTs von allen genannten Stellen. Zudem gehört die Bereitstellung voller KLTs an den Verpackungsplätzen und die Wiedereinlagerung dieser Behälter zum Leistungsspektrum.
Seit der Erweiterung umfasst das Lager eine Länge von ca. 40 Meter, eine Breite von ca. 6,30 Meter und eine Höhe von ca. 5 Meter. Die Dämpfungssysteme werden in zwei verschiedenen Typen von Kleinladungsträgern (KLTs) gelagert, die sich in Höhe und Gewicht unterscheiden. Da die KLTs an den Verpackungsplätzen auch von Mitarbeitern gehandelt werden, beträgt das maximal zulässige Gewicht im gefüllten Zustand 15 Kilogramm. Zur Einlagerung depalettiert der Handlingroboter (Smart NJ40-2.5 des Herstellers Comau) auf Euro-Paletten angelieferte KLT und legt sie auf eine Einlager-Rollenbahn. Der Greifer besteht aus vier pneumatisch schwenkbaren Greifarmen zum sicheren Handling der Behälter. Die Position der KLT wird von Laserscannern erkannt. Aus Sicherheitsgründen steht der Roboter innerhalb eines Schutzzaunes mit Schutztür. Die angetriebenen Einlager-Rollbahnen fördern die KLT in das Regalbediengerät (RBG), welches sie in den zugewiesenen Lagerplätzen einlagert. Dabei verfährt das RBG entlang einer Zahnstange innerhalb einer geschlossenen Schutzeinhausung. Der obere Teil wird von Laufrollen an der Führungsschiene geführt. Die Einzugs- und Ausschubvorrichtung zieht über Flachriemen den KLT von der Rollenbahn ein, Pneumatikzylinder richten ihn aus. Das RBG lagert den KLT nun in einem vom Lagerverwaltungsrechner zugewiesenen Stellplatz ein.
Nach Anforderung zur Auslagerung eines KLT zieht die Einzug- und Ausschubvorrichtung den entsprechenden Behälter vom Stellplatz ein und übergibt ihn zur ausfördernden Rollenbahn. Ein Mitarbeiter entnimmt den KLT, stellt ihn auf einen der Arbeitstische und entnimmt die benötigte Anzahl an Teilen. Nach der Bearbeitung stellt der Bediener den leeren oder teilgefüllten Behälter wieder zurück auf die Rollenbahn und quittiert die Ablage. Ganz leere KLTs werden aus dem Lagersystem gefördert und vom Roboter zwecks Abtransports auf leere Paletten gestapelt. Zu der Anlage gehören 15 verschiedene motorisch angetriebene Rollenbahnen: sechs zum Ausschleusen voller KLTs, drei zum Zuführen voller KLTs, zwei zum Zuführen leerer KLTs, zwei zur Rückführung voller KLTs und eins zur Rückführung leerer KLTs. Behälter die als „nicht in Ordnung“ erkannt wurden, werden aus dem System ausgeschleust.
Lager 2: Pufferlager Laufteilmontage
Das Pufferlager für die Laufteilmontage erstreckt sich auf einer Länge von ca. 22,1 Metern, einer Breite von ca. 4,44 Metern und einer Höhe von ca. 5 Metern. Zum Lager gehören 17 motorisch angetriebene Rollenbahnen. Eingelagert werden hier zwei verschieden große Eurotecbehälter, die sich in Höhe, Volumen und Gewicht unterscheiden. Diese Kleinladungsträger (KLT) werden über die Rollenbahnen dem Regalbediengerät zugeführt. Dieses kann zwei KLTs gleichzeitig transportieren und lagert diese je nach Anforderung in die Lagerplätze der Regale ein oder schiebt sie auf die Rollenbahnen zur Auslagerung zwecks Zuführung zu den Montageanlagen. Das RBG verfährt dabei entlang einer Zahnstange. Oben wird es von Laufrollen an der Führungsschiene geführt. Die Einzugs- und Ausschubvorrichtung fördert über einen Zahnriemen den KLT von der Rollenbahn bzw. auf die Rollenbahn. Der KLT wird dabei von Pneumatikzylindern ausgerichtet und in einem vom Lagerverwaltungsrechner zugewiesenen Stellplatz eingelagert. Der Bahnhof des RBG wird über Hebeketten angehoben bzw. abgesenkt. Über einen Seillängengeber wird die Hubposition überwacht und korrigiert.
de Man MasterMind steuert alle Prozesse
Bei beiden Lagern sind die Regale und die Fahrbereiche der RBGs aus Sicherheits- und Staubschutzgründen von einer Schutzeinhausung umgeben, der Bereich rund um den Roboter ist durch einen Schutzzaun gesichert. Der Zugang zu den Anlagenbereichen erfolgt jeweils über eine Schutztür. Vor dem Öffnen der Schutztür ist der Taster „Schutztür anmelden“ am Bedienelement zu betätigen, damit die Anlage den Takt zu Ende fahren kann. Die Sicherheitsverriegelung mit Zuhaltung verhindert solange das Öffnen der Tür, bis die Gefahr vorbei ist. Eine Notentriegelung erlaubt es, eingeschlossenen Personen die Zelle zu verlassen.
Die Funktionen der Anlagensteuerungen werden auf einem Touchpanel angezeigt und vom Bediener angewählt. Die Hauptansicht bietet über eine schematische Darstellung der Anlage einen schnellen, einfachen und intuitiven Zugriff auf alle Funktionen. Kern des Materialflusssystemes ist der Lagerverwaltungsrechner (LVR). Auf dem LVR läuft die Serversoftware des de Man Softwareproduktes MasterMind. Der LVR ist mit dem Hausnetz der Firma Hettich verbunden und hält eine Verbindung zu einer Datenbank, in der alle relevanten Daten des Systems abgelegt werden. Zudem ist er Verbindungspartner zum SAP, von dem Transportaufträge übernommen und an das Quittierungen übergeben werden. Der LVR generiert aus den Daten Transporte für das RBG und die Fördertechnik. Alle KLTs sind auf beiden Längsseiten mit einem Barcode gekennzeichnet. Stationäre Scanner an den Fördertechniken können so jeden Behälter eindeutig identifizieren. Die Roboterzelle verfügt über einen eigenen Bedien-PC, dessen Oberfläche ebenfalls aus der de Man MasterMind Systemfamilie stammt und sich bedienerfreundlich in das Look-and-feel des Lagerverwaltungsrechners einfügt.
Komplettlösungen aus einer Hand
Die de Man Automation + Service GmbH & Co. KG aus Borgholzhausen ist Spezialist für ganzheitliche Automatisierungslösungen und kompetenten Service. Seit über 45 Jahren entwickelt de Man für jeden Kunden maßgeschneiderte Automatisierungslösungen in den Bereichen Robotik, Lager und Fördertechnik. Individuelle Programmierdienstleistungen sowie kompetenter Service für eigene und externe Anlagen – von der Wartung und Reparatur bis hin zum Retrofit – runden das Angebot des Systemintegrators ab. Weitere Informationen: www.deman.de!
de Man Automation+Service GmbH & Co. KG
Industriestraße 18
33829 Borgholzhausen
Telefon: +49 (5425) 9497-0
Telefax: +49 (5425) 5774
http://www.deman.de
Marketing
Telefon: +49 (5425) 9497-25
Fax: +49 (5425) 9497-90
E-Mail: sandra.friedlein@deman.de