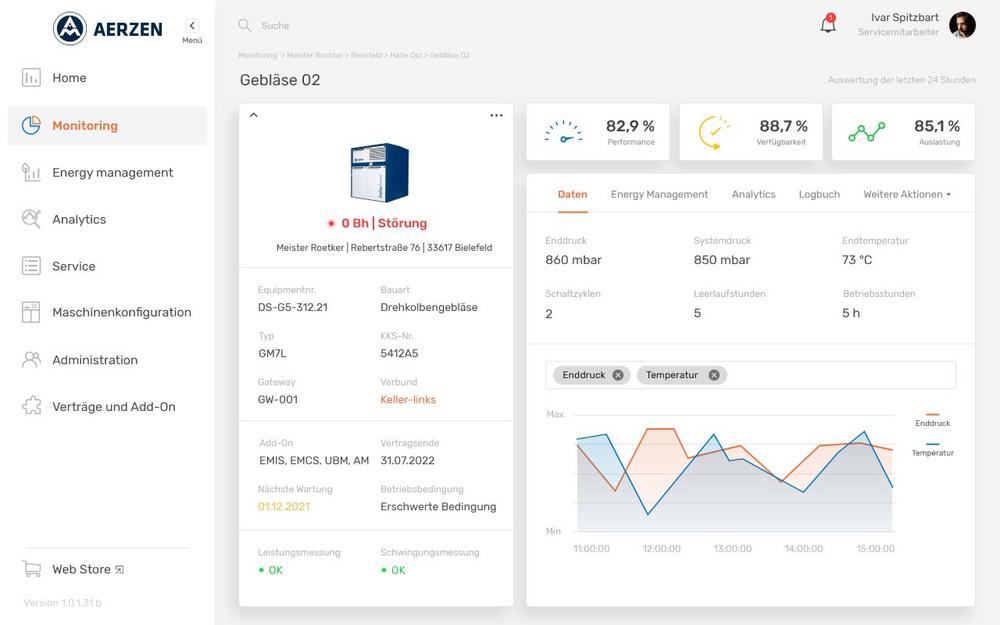
AERprogress – Added value through digitisation
From the operator’s point of view, the change towards networked compressor and blower packages is attractive in several respects. On the one hand, the extensive recording and evaluation of energy-related process data allows efficient control of the assemblies in combination – this can noticeably reduce energy costs and CO2-emissions. On the other hand, operators benefit from greater process safety, transparency and reliability. The recording of all relevant operating data provides information about the processes involved in the compression process. This information can be used to implement modern and data-supported service and maintenance concepts. Advantage: condition-based service and maintenance of the systems reduces the number of incidents and minimises downtimes.
Aerzen Digital Services – from machine manufacturer to system integrator
The new company unit Aerzen Digital Systems underlines the transformation of Aerzener Maschinenfabrik from a renowned manufacturer of assemblies to a digital system integrator. As a leading technology developer AERZEN focuses on the data-based consideration of the entire life cycle of its machines. The service offer of the new digital unit is accordingly focused on the overall optimisation of the entire process chain.
The focus of the new AERprogress offer is the customer as operator of compressor and blower packages: The various components of the modular service package are aimed at optimising the cost structure in Machine Life Cycle Cost Management in a sustainable and customer-specific manner.
Maximum transparency in Machine Park Management
As a basic package AERZEN offers the user-friendly Machine Park Management. Users can see all active plants on an interactive world map and can select them specifically. This allows you to see at a glance which machines are in operation, when maintenance is due or where a fault may be present. In the monitoring menu the user can view the relevant process parameters in detail: Diagrams and trend displays provide information about performance, availability and utilisation of machines. Sensitive and customer-specific process data is always protected during live transmission, data ownership remains with the customer at all times. For the operator, the central plant management reduces time and cost-intensive on-site appointments.
Customised Add-ons for individual projects
In order to meet the individual, industry-dependent requirements for operation of blower and compressor packages, AERZEN offers various Add-ons.
The Add-ons in the Condition Monitoring section are aimed at optimising plant availability through time- or usage-based maintenance concepts. By recording the operating hours or system conditions, it is possible to fully exploit the service life of the components.
In the category Energy Management AERZEN offers with the Improvement System an Add-on for sustainable reduction of energy consumption and CO2-emission. By means of the data-based evaluation of energy-related parameters, weak points are identified and optimisation potentials are made visible. Depending on the system configuration, this makes it possible to reduce energy costs by more than 20 %.
The Consumption Certification Add-on rounds off the range of services of AERprogress and allows the customers to create standard-compliant reports with just one click. The reports meet the requirements of the energy management standard ISO 50001:2018 and facilitate the obligation to provide proof to shareholders and stakeholders.
Industrial plants all over the world are provided with gaseous media using AERZEN blowers and compressors. The innovative AERZEN machine technology represents experience gained over more than 150 years of company history. The range of products includes rotary lobe compressors, positive displacement blowers, turbo blowers and screw compressors. AERZEN blowers and compressors are tested and certified according to DIN EN ISO 9001. There is a variety of product offers from standard products to special solutions individually tailored to the customer. Digital services can be used to increase efficiency, availability and productivity in a sustainable and future-oriented manner.
In addition, the AERZEN After Sales Service offers the complete range of services – from the full maintenance contract to repairs and upgrades of existing plants.
Aerzener Maschinenfabrik GmbH
Reherweg 28
31855 Aerzen
Telefon: +49 (5154) 81-0
Telefax: +49 (5154) 81-9191
http://www.aerzen.com
Marketing Referent
Telefon: +49 (5154) 81-9970
Fax: +49 (5154) 81-719970
E-Mail: sebastian.meissler@aerzener.de
