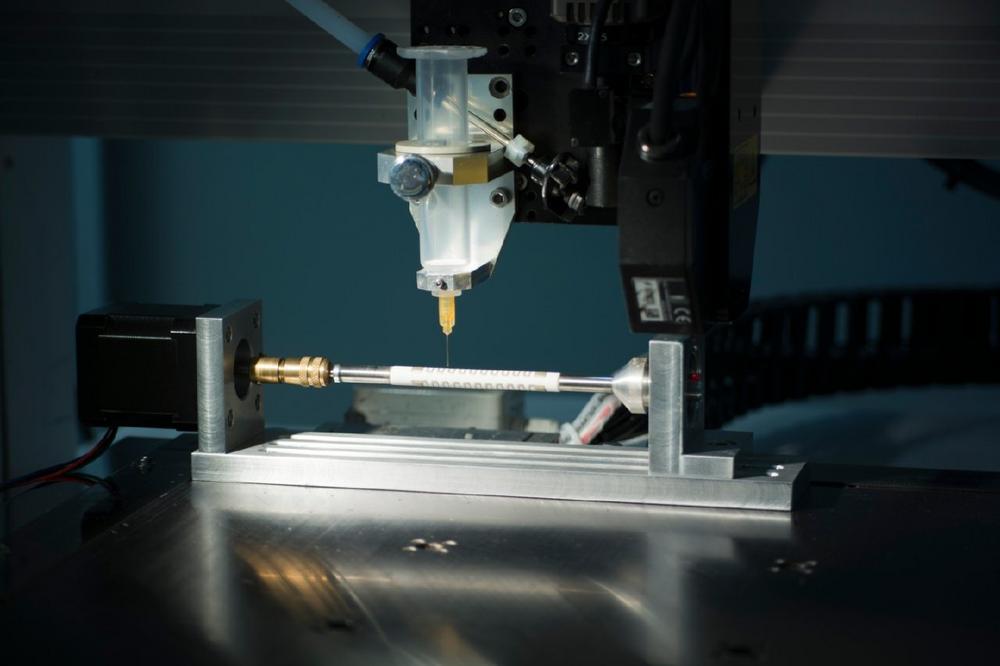
Hot patterns in cold space
“We are continuously researching with our partners to find even more powerful solutions for our customers and to further increase the reliability of our systems,” emphasizes Dr. André Holz, Team Leader Thermal Engineering at Airbus Defence and Space in Bremen. “We are actively cooperating with Fraunhofer scientists to further develop these technologies, such as printed heaters, which are a valuable support for both sides.” Because up to now, technicians have had to manually apply polymer heating foils in these cases. “This is not only time-consuming, but also prone to errors,” explains Lukas Stepien, group manager Printing, who co-developed the additively manufactured heaters at Fraunhofer IWS. “Small gas bubbles can be enclosed undetected during the bonding process. The bubbles expand in space vacuum, a process which ultimately lowers the heat output.” The new IWS concept now solves these problems. In particular, it involves heating titanium tubes with a diameter of only six millimeters, which are subsequently used to transport gases or liquids. First, the Fraunhofer engineers insulate these tubes with a thin ceramic coating in a thermal spray system. The next step is to use a dispense printing machine to apply the heating elements, which resemble the shape of a meander. If an electrical current flows through the metallic meander, it will release heat.
Ultra-thin meanders precisely printed on curved surfaces
To create these heating patterns, the scientists fill a cartridge with a special paste containing small silver particles. Other pastes with particles of copper, nickel or other conductive metals can also be used. Compressed air then drives the viscous material through the cartridge towards a fine cannula. This hollow needle finally prints the heating pattern, about ten micrometers thick, onto the ceramic-insulated tubes, which rotate on a shaft. “The print head must maintain a constant distance from the ceramic layer at all times – and this is not on a two-dimensional surface, but on a curved tube,” emphasizes Lukas Stepien. This challenge is a very special one, and has been solved by Fraunhofer IWS through a sophisticated interaction of shaft and cannula control.
Such a solution offers several advantages compared to conventional adhesive heating foils: On the one hand, a lot of error-prone manual work is eliminated. The Fraunhofer heaters, however, can be printed automatically instead, allowing to coat even complexly shaped objects with a perfect fit – without air bubbles or wrinkles, which often occur in films. The Dresden engineers also expect their printed heaters to be cheaper and more flexible to manufacture. They will last longer, especially at high operating temperatures, function more reliably and achieve higher long-term heating performance than conventional solutions. Higher power densities, material and time savings can be achieved. In addition, manufacturers can test in advance to verify the performance of the printed heaters in practical use. “Beyond 300 degrees, the use of foil heaters simply is not an option,” emphasizes Lukas Stepien. “Plastics cannot withstand such operating temperatures permanently.” So far, Fraunhofer IWS printed heating elements are designed for temperatures of up to 200 degrees. The Dresden researchers intend to raise this limit to about 800 degrees in the future using new paste compositions and advanced developments.
A further improvement has been added to the institute’s research agenda: In order to provide heat, the printed heaters need a power connection. Previously solved by soldering connections, the next step is to use more effective contacting methods “Made in Dresden”.
Against condensed water on lenses
Apart from space travel, quite earthly applications also suggest themselves: For example, filigree heaters can be imagined that keep annoying condensation away from reflex cameras or from the camera lenses of autonomous vehicles. Pipe systems with precisely printed heaters are also interesting for the chemical, semiconductor and food industries, which often require precisely controlled temperatures for their processes.
The Fraunhofer Institute for Material and Beam Technology IWS stands for innovations in laser and surface technology. As an institute of the Fraunhofer-Gesellschaft zur Förderung der angewandten Forschung e. V., IWS offers one stop solutions ranging from the development of new processes to implementation into production up to application-oriented support. The fields of systems technology and process simulation complement the core competencies. The technology fields of Fraunhofer IWS include PVD and nanotechnology, chemical surface technology, thermal surface technology, generation and printing, joining, laser ablation and separation as well as microtechnology. The competence field of material characterization and testing supports the research activities.
At Westsächsische Hochschule Zwickau, IWS runs the Fraunhofer Application Center for Optical Metrology and Surface Technologies AZOM. The Fraunhofer project group at the Dortmunder OberflächenCentrum DOC® is also integrated into the Dresden Institute. The main cooperation partners in the USA include the Center for Coatings and Diamond Technologies (CCD) at Michigan State University in East Lansing and the Center for Laser Applications (CLA) in Plymouth, Michigan. Fraunhofer IWS employs around 450 people at its headquarters in Dresden.
Fraunhofer-Institut für Werkstoff- und Strahltechnik IWS
Winterbergstraße 28
01277 Dresden
Telefon: +49 (351) 83391-0
Telefax: +49 (351) 83391-3300
http://www.iws.fraunhofer.de
Leiter Unternehmenskommunikation
Telefon: +49 (351) 83391-3614
Fax: +49 (351) 83391-3300
E-Mail: markus.forytta@iws.fraunhofer.de
