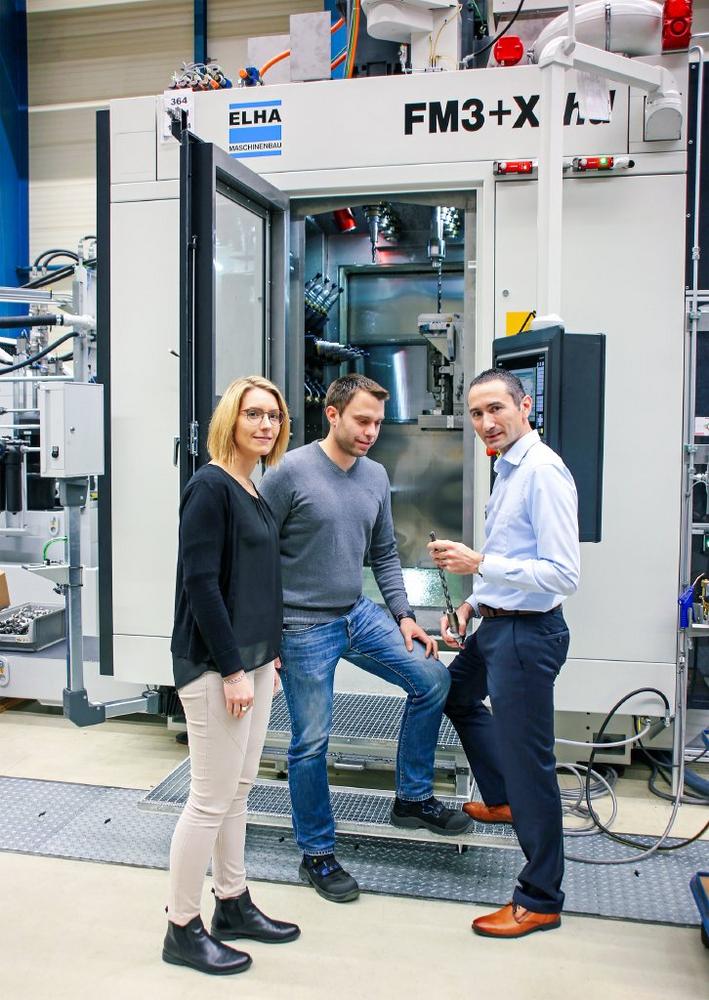
Conceived from the process – a development partnership between a machine manufacturer and a tool manufacturer
“We have a unique approach when we receive customer inquiries,” says Meinolf Wolke, Sales Team Leader at ELHA-MASCHINENBAU Liemke KG (ELHA) in Hövelhof. The medium-sized, owner-managed special machine construction company places the workpiece and its machining at the centre of development and devises an optimal solution perfectly designed for the process sequence. “In doing so, we take all the technical and economic requirements into account,” clarifies Wolke further. Only then do those responsible decide whether an existing machining concept can be used for the process or whether an individual, application-specific construction is required. Meinolf Wolke explains: “As well as providing the machine, we offer services that stretch from process development and the construction of fixtures all the way through to complete, ready-to-operate solutions with automation and production support.”
Special tools for low total costs
“The machining tasks are often as unique as the parts themselves – including in terms of the workpiece materials,” adds Alexander Wiesner, Technical Advisor at MAPAL. “Of course, a lot of machining work on complex parts can be achieved with standard tools. But that often comes with significant drawbacks in terms of cycle times, quality, and cost-effectiveness, particularly when large quantities are being produced.” In these cases, special tools that are precisely calibrated by MAPAL for the machining task in question are preferred.
“During the tool design phase, it’s essential to determine the necessary parameters for the machining process,” says Wiesner, “particularly in the case of challenging geometries.” In order to design the process in the best possible way, MAPAL often makes prototype tools. These are then used to carry out extensive tests with the part to be machined. “That, in turn, helps the equipment manufacturers design the machine with the values identified during testing,” continues Wiesner. He says that MAPAL has had a long-standing partnership with ELHA in this area. The following three examples demonstrate the resulting benefits to customers:
Solid drills for the machining of suspension arms
“We were dissatisfied with the solution that we had been using for drilling from solid in aluminium when machining a suspension arm, which included creating a fitting,” remembers ELHA Project Leader Friedhelm Dresmann. At the time, the company was using tools with brazed PCD cutting edges. In order to keep the machining time as low as possible, these drills were being used with very high feed rates. The disadvantages of this solution were the high drive power required and the insufficient durability of the PCD cutting edges on the solid drill step. In search of a solution, those responsible at ELHA turned to MAPAL. Together, the employees of the machine manufacturer and the tool manufacturer worked to find a solution. What they came up with was a hybrid tool. The tip of the tool is equipped with three-bladed, CVD-diamond coated, ISO-indexable inserts for drilling from solid. The fitting is created using brazed PCD cutting edges on the second step of the tool.
MAPAL’s research engineers tested the new tool in their own R&D centre. The results were impressive. In addition to the lower costs of the indexable inserts overall, the positive blade geometry meant that less drive power was required. What’s more, the previous solution had often produced long metal chips – with the new tool, this was no longer an issue. The indexable inserts at the tip of the drill, which are under significant stress, can be quickly and easily flipped or replaced. As a result, the maintenance costs were also noticeably reduced. Altogether, the suspension arm manufacturers’ production costs for each drilled bore were reduced by over 50 percent.
Disc milling cutters for the machining of suspension arms
“We also worked with MAPAL to find an efficient solution for machining forged suspension arms,” explains ELHA Project Leader Marcel Thieschneider. “Our goal was to develop process-reliable tools while maintaining the required cycle times.” For the suspension arm, a yoke needed to be created from the solid material at the end of the arm. During the required four-spindle machining process, the long-chipping workpiece material demands very high drive power to the machine. In addition to this, the internal contour of the part features a number of angles and radii, making the expulsion of chips during milling difficult.
“In order to ensure short process times, we developed a disc milling cutter with ISO indexable inserts that enables roughing and finishing with minimum quantity lubrication in just one step,” recalls Alexander Wiesner. The indexable inserts are coated with CVD diamond. The precisely defined arrangement of the individual inserts limits the drive power required. After considering the comprehensive tests at MAPAL and the data that resulted from them, ELHA set its machine to operate at this drive power. A positive side effect of using the disc milling cutter was the reduction in cycle time, as only one cut is needed. On top of that, the tool only occupies one row of spindles, reducing the resulting tool costs for the end customer.
Deep hole drill for the machining of stainless steel forged components
“Our customer is a manufacturer of high-pressure fuel-supply distributors for petrol engines. This requires drilling deep bores in narrow, forged, stainless steel blanks,” says ELHA Project Leader Jörg Rodehutskors. The material is difficult to machine, and the bore is 300 mm deep. The drill needs to experience as little axial deviation as possible, otherwise wall of the part (which experiences high pressure) will fall below the required minimum thickness. Previously, the manufacturer machined these bores in a separate, single-spindle machine tool with a single-flute deep hole drill.
In order to optimise their processes, the customer asked ELHA to provide a solution in which the process described above, along with all other machining tasks, could be performed on a single production module using multiple spindles. The parts should leave the production module in ready-to-install condition.
ELHA enlisted MAPAL to assist with the bore process previously discussed. The tool manufacturer was asked to provide a drill that was able to carry out the machining more quickly – and with less deviation and less wear and tear. The MAPAL engineers developed a double-edged solid carbide drill designed to meet the requirements perfectly. With application parameters of Vc = 90 m/min and f = 0.5 mm, the new tool achieves a tool life of 80 metres – almost three times as long as the solution previously in use. Another special feature of the solution developed jointly by ELHA and MAPAL is that the workpieces in the clamping fixture rotate in the opposite direction to the drill during machining, which reduces the deviation of the bore even further. This leads to significant cycle time benefits for the customer, who manufactures up to five million of these parts every year. And on top of that, they now only need one machine to carry out all machining tasks.
Development partnership synergies
“These three examples demonstrate the benefits of our close collaboration with MAPAL,” concludes Carina Becker from Technical Sales at ELHA. “And on top of that, the cooperation gives our design engineers additional freedom.” MAPAL’s specialists for the development of high-performance tools, as well as their exceptionally well-equipped R&D department in Aalen, make it possible to develop and intensively test new tool solutions even during the planning phase. That means ELHA is able to offer its customers even more well-engineered and economically advantageous solutions.
The production module (FM) Philosophy
ELHA primarily developed the production module series for the cutting manufacturing of mass-produced parts (> 100,000 identical or similar parts). In this manufacturing concept, the tools themselves are not moved, but instead the parts are passed along tools arranged in rows. Every row of tools has a clamp and drive system that is optimised for the machining task. The workpieces are moved from each tool row to the next using the clamping fixture, which achieves the shortest possible chip-to-chip times. The modular system can be equipped with various multi-spindle modules. Multi-spindle revolvers providing space for up to 128 directly driven tools can be used for even more flexibility.
About ELHA-MASCHINENBAU Liemke KG
ELHA-MASCHINENBAU is a family-run business that manufactures machine tools for cutting metal machining. The company was founded in 1930 and today is known for its machining centres, special-purpose machines and production modules.
MAPAL – tooling the customer’s success
MAPAL Präzisionswerkzeuge Dr. Kress KG is one of the leading international suppliers of precision tools for the machining of practically all materials. The company founded in 1950 supplies leading customers from the automotive and aerospace industries and from machine and plant engineering. With its innovations the family-owned company sets trends and standards in production and machining technology. MAPAL sees itself as a technology partner, supporting its customers with the development of efficient and resource-conserving machining processes using individual tool concepts. The company is represented with production facilities, sales subsidiaries and representatives in 44 countries worldwide. In 2019 the MAPAL Group had 5,500 employees, generating sales of EUR 620 million.
MAPAL Dr. Kress KG
Obere Bahnstr. 13
73431 Aalen
Telefon: +49 (7361) 585-0
Telefax: +49 (7361) 585-1029
http://www.mapal.com
Vice President Marketing and Product Management
Telefon: +49 (7361) 585-3683
Fax: +49 (7361) 585-1019
E-Mail: andreas.enzenbach@de.mapal.com
Corporate Communications
Telefon: +49 (7361) 585-3552
Fax: +49 (7361) 585-1029
E-Mail: patricia.mueller@mapal.com