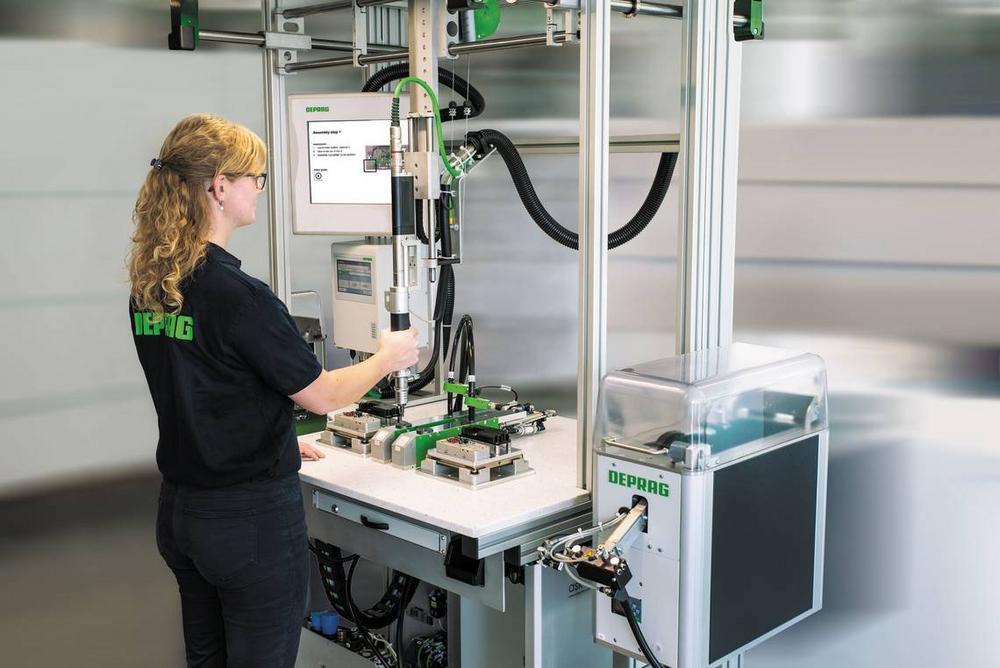
Configuration, not programming: Process visualisation made easy
Businesses must be able to react quickly to changing quantities, models or degrees of automation. Even if systems are ready and available for operation within a short space of time, new sequences need to be integrated correctly into the production process and employees need to be trained. As a consequence, assembly errors are not infrequent – whether due to insufficient or incorrectly understood assembly instructions – or carelessness. Even experienced employees can easily overlook alterations to the operating procedure.
The automation expert DEPRAG SCHULZ GMBH u. CO. has come up with the optimal solution: the new DEPRAG Operator Guidance software which effectively prevents any glitches in the production process. The software is there to support the operator throughout assembly and is reliable and easy to understand. First and foremost, it prevents human errors. Where previously, each worker needed to develop extensive know-how in order to guarantee trouble-free assembly, now with the DEPRAG Operator Guidance, complicated sequences are made simple. The app guides the operator step-by-step through the assembly process – even new members of the team with no previous skills can be trained in a short time.
Intuitive instructions – fast and reliable assembly
The software facilitates the creation of as many digital assembly instructions as required. The DEPRAG Operator Guidance is installed on appropriate hardware with an operating system (from Windows 7). System requirements also include PowerPoint and a display unit at the work station. PowerPoint is used to create a step-by-step guide for each component. The flexibility of PowerPoint allows a range of visualisation options – text, images, videos or audio files can be added with ease. “Our customers can configure any number of components and product groups, and all without any programming knowledge!” exclaims Daniel Guttenberger, Product Manager for DEPRAG Screwdriving Technology. Time-consuming consultations between the manufacturer and customer are no longer needed. “The customer can, of course, adjust or expand on the working instructions at any time. This means that any compliance requirements for in-house processes and directives can simply be factored in”, continues Guttenberger.
Assembly instructions created by the customer in the DEPRAG Operator Guidance component configurator are conveniently linked with different screwdriving programs and rules – without the need for a higher-level PLC. A separate screwdriving program is saved for each individual screw position. Once this screw position has been reached in the process, the corresponding screwdriving program is activated in the DEPRAG sequence controller. Communication between the screwdriving controller and PC occurs via a direct cable connection or indirectly via the customer’s normal Ethernet network. Automatic supervision of each screw position ascertains whether an OK or NOT OK result has been achieved. Depending on the result and rules configured, a new step is displayed for the worker. This impressive operator guidance enables fast, error-free assembly and ensures the highest process reliability.
Even greater process reliability can be achieved with the addition of the DEPRAG position control stand (PKS) available as standard. Position control systems coordinate and optimise the entire production process and ensure that the correct fastener is assembled with the correct torque, at the correct time and in the correct location. When assembling several screws on one component, the sequential order in which screws are tightened may play a vital role in process reliability. Position control systems manage these sequences: the screw can only be tightened if the operator has followed the correct order.
The impressive features of the software do not end with clear operator instructions and fast teaching of new employees, the DEPRAG Operator Guidance also facilitates the automatic documentation of processing data.
Automatic archiving and documentation of processing data
Seamless documentation of production data is increasingly vital. Using the DEPRAG Operator Guidance, processing data for each component can be filed and saved centrally: on a hard drive or in the DEPRAG Cockpit. This eliminates manual data collection. Processing data and screwdriving results are automatically matched with the component’s serial number. The screw position and relevant end values are saved for each serial number. This ensures complete traceability and transparency.
The software also allows integration of customer-specific extensions (so-called plugins). The customer can integrate their own sequences and programs for defined events (e.g. component successfully assembled, screw position successfully assembled). There are options for e.g. communication with the customer’s individual MES system, transfer of end values, display of additional instructions or similar.
Outstanding, cost-effective practical solution
The DEPRAG Operator Guidance software significantly increases process reliability on simple manual work stations without a PLC. It is also suitable for use at repair stations. The operator can, for example, select the screw location to be repaired on the product image. The software automatically detects the correct screwdriving program required. In addition to screw assembly, the software can also be used for other assembly processes, such as gluing or pressing, etc.
If a customer wants to implement a new assembly process, first of all, any specifications must be defined, such as: the correct sequential order for the screws, the various torques needed for each screw position and ensuring that no screw position is overlooked. At the same time, all processing data such as torque, angle, status, screw position and serial number of each component must be assigned correctly and saved automatically.
Thanks to the DEPRAG Operator Guidance, a fast, cost-effective solution has been found. First, the customer compiles all operating steps and the corresponding processing parameters. Once configured, the software guides the operator step-by-step through the assembly process. At the manual work station, all instructions are clearly presented for the operator on a display screen. The worker begins by scanning the serial number of the component to be assembled or entering this manually. This ensures that processing data is matched with the correct component right from the start. The software automatically provides the corresponding digital assembly guide for that specific component and informs the operator of the next assembly step. To further support the worker, images, text or short videos can be displayed to precisely demonstrate the location of the parts required. The operator then assembles each screw position on the component according to a specific sequential order. The OK or NOT OK result is automatically monitored. Depending on the result and rules configured, the worker is shown the next step in the procedure. If any steps are carried out mistakenly or incorrectly, the system immediately blocks the execution of further steps until the previous step has been corrected. Some notifications must also be acknowledged by the operator – an additional safety feature. Complex steps can be demonstrated clearly using detailed videos.
“Manufacturing companies aim to guarantee maximum quality with minimum outlay and expense. In production, if errors are prevented or detected and remedied, time-consuming reworking steps and waste can be avoided. Our new DEPRAG Operator Guidance software is the ideal solution for improving product quality and raising productivity in automated production and the field of industrial reworking”, clarifies Product Manager Guttenberger.
DEPRAG SCHULZ GMBH u. CO.
Carl-Schulz-Platz 1
92224 Amberg
Telefon: +49 (9621) 371-0
Telefax: +49 (9621) 371-120
http://www.deprag.com
Pressekontakt
Telefon: +49 (9621) 371-343
Fax: +49 (9621) 371-199
E-Mail: d.duebbelde@deprag.de

