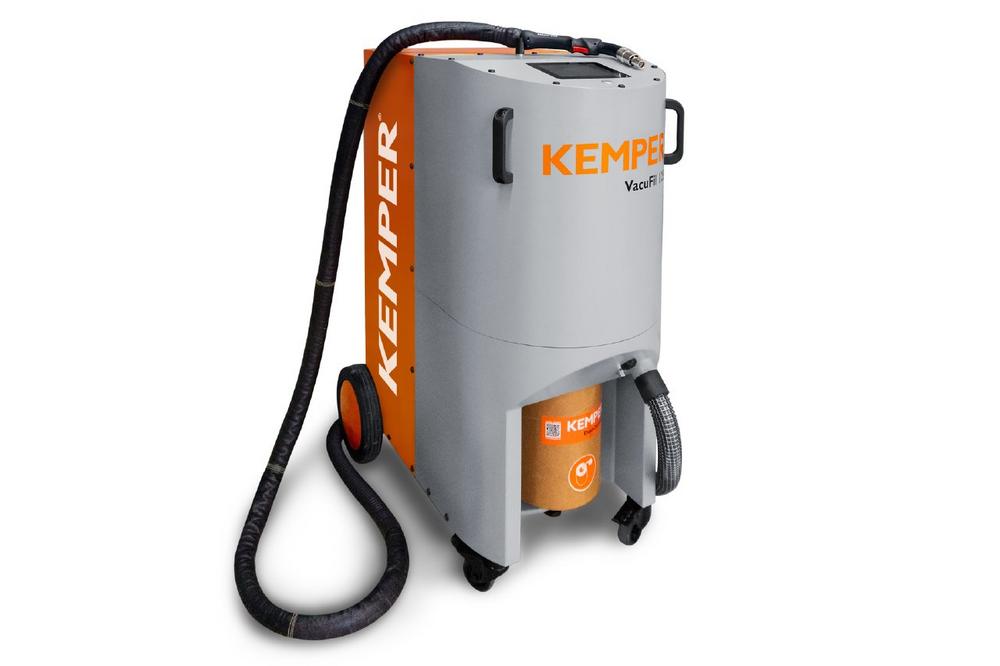
One extraction system for all: VacuFil places the focus on the extraction capacity for each torch
To ensure that the protective gas layer is not destroyed, the correct extraction capacity is important for torch extraction. Extraction torches from any manufacturer require an individual volume flow for this. The new EN ISO 21094 DIN standard now fundamentally defines exactly how this is to be determined. "With VacuFil, we are creating a hitherto unique solution for torch extraction in accordance with these specifications." says Björn Kemper, CEO of KEMPER GmbH. "Our new high-vacuum units are convincing not only due to their simple operation. Thanks to the automatic speed control, welders do not have to laboriously determine the extraction capacity manually. They act in accordance with the standards at all times and the protective gas layer is maintained."
Select the torch and the extraction system adjusts itself permanently
VacuFil can be combined with any conventional welding torch. When welders couple their torch technology with the digital extraction units of the series, they intuitively select the torch of their choice on a touch display. The units then automatically adjust their output to the torch parameters stored in the unit’s software. The integrated extraction volume control ensures that the extraction systems continuously adjust their performance during the welding process. This means that the highest possible air volume flow is always used for extraction.
Depending on the danger intensity of the welding process used, the VacuFil 125i, 150i and 250i versions are available with different maximum extraction capacities. The W3 certification from the Institute for Occupational Safety and Health certifies that the systems meet the best possible protective welding equipment standards. Even the extraction of welding fumes during the processing of chrome-nickel steels is possible. VacuFil is eminently suitable for detecting high levels of smoke and dust during industrial welding. The automatic filter cleaning system enables uninterrupted continuous operation.
Unique torch database assembled
During the development of the VacuFil series, KEMPER has built up extensive torch know-how regarding the necessary extraction capacity. In its own test positions, the manufacturer determined the necessary torch parameters and built up a unique torch database over months. If torch manufacturers change their systems, KEMPER adjusts the parameters in the master data and also adapts the individual extraction capacity. The units are then simple to update using the KEMPER Cloud over the Internet.
All units are also available as analogue VacuFil 125, 150 and 250 versions. Here, welders set the required extraction capacity manually. All new VacuFil variants are suitable as mobile extraction units for use at changing workplaces or when working with large work pieces. Welders automatically carry the torch-integrated extraction unit with them while they are welding.
Earthmoving machinery manufacturer orders 90 units
Shortly after the market launch, the VacuFil solution has already convinced several international machine manufacturers. For example, one of the world’s largest manufacturers of earthmoving machinery has ordered the first 90 VacuFil 125i and is using them successfully in a production facility in the UK. Further orders have since been received almost weekly. "The companies usually have torches from different manufacturers for changing welding applications. A single system lets them achieve a high level of occupational safety when using different torches" says Marc Crawford, Sales Manager UK at KEMPER.
KEMPER GmbH is a manufacturer of extraction plants and filter systems for the metal processing sector. The medium-sized, family-run business based in Vreden, Westphalia, is the technology leader with its highly efficient filter systems that filter even ultrafine dust particles from the air when welding fumes are generated. The product portfolio includes extraction tables for cutting processes and the entire accessory chain for protective welding equipment and air quality management for the metal processing industry. KEMPER was founded in 1977 and has more than 400 employees today. The management team consists of Björn Kemper and Frederic Lanz. As well as headquarters in Vreden, Germany, the company also has a production site near Prague in the Czech Republic. KEMPER is represented worldwide with more than ten branches and numerous established trading partners.
KEMPER GmbH
Von-Siemens-Str. 20
48691 Vreden
Telefon: +49 (2564) 68-0
Telefax: +49 (2564) 68-120
http://www.kemper.eu
Sputnik – Presse- und Öffentlichkeitsarbeit
Telefon: +49 (251) 625561-26
E-Mail: patzkowsky@sputnik-agentur.de

