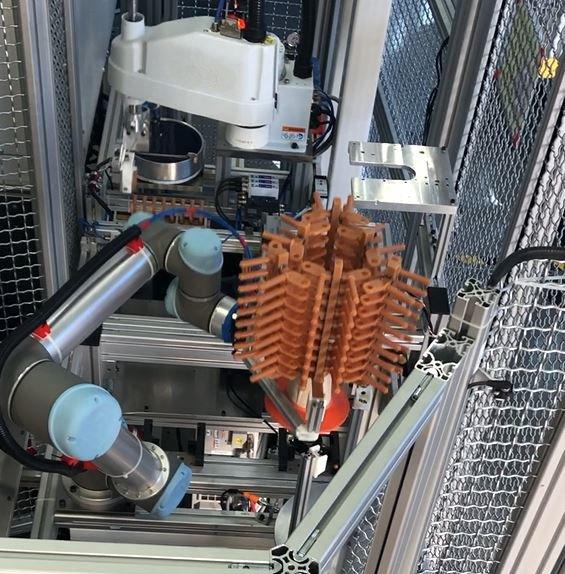
Next step to smart factory – the automatic wax gluing
Particularly in the recent years the company has focused on increasing efficiency in production under the Lean-approach. “We set a first milestone in 2018 with the development of an automated casting plant,” says managing director Alexander Lenert. For the first time at BLANK casting was possible by means of communicating robots. Since then the system has been further developed and today represents an important module in the company’s casting department.
In a next step the development department examined the wax parts production and looked for improvement potentials. “Employees attach the wax parts to wax rods and then connect them to so-called trees before they are coated with ceramic and sand in the next step, thus forming the mould for the subsequent casting process,” explains Diemer, “Depending on the number of pieces and the complexity of the geometry, the wax parts are either injected automatically or produced on a manual injection tool. So the potential lies in the high volumes of individual parts, because automation can quickly pay off here. But automated processing can be also economical for complex geometries and simultaneously high quality requirements.” Together with his team Reinhard Diemer tested this in 2019 when extending an existing wax injection machine.
The wax parts are injected automatically as part of the regular process. In the next step, however, the parts are not placed on a conveyor belt to distribute them to the manual gluing stations. Instead, a robot glues the parts to the wax rods. “First we use a linear robot which lifts the injection moulded parts out of the mould and places them in a prefabricated mould,” says Diemer. Like in the manual work sequence, another robot grips the parts, dips them in hot wax and then glues them to the wax rods.
After about one year of development Diemer is optimistic about the pilot project. “Since these are filigree processes it was important to exactly coordinate the machines with each other. After some fine adjustment we have managed to do this very well.” The robots are now so far advanced that the rods with the wax parts can even be assembled to trees within the autonomous production cell which requires highest precision.
The automated production cell makes this precision possible in an area which is otherwise strongly characterized by manual work steps. “The gluers estimate the distance between the parts on the rods through their many years of experience,” says Diemer, “Same applies to the gluing process and the assembly of the entire tree structure. Automation makes the process faster, more predictable and eliminates variations in quality.”
Whether and for which parts an automation of wax gluing is worthwhile should be decided from case to case. “For each part a set-up effort is needed to adjust the robots to the requirements of the new geometry. This must not be neglected and must be calculated.” Currently the plant is in operation for 6 series of parts and will be further expanded in the coming months.
Further information on this project is available on request from our press contact: manuela.schmid@feinguss-blank.de
Texmo Blank Germany GmbH
Industriestr. 18
88499 Riedlingen
Telefon: +49 (7371) 1820
http://www.TexmoBlank.com
Marketing
Telefon: +49 (7371) 182-200
Fax: +49 (7371) 18244-200
E-Mail: manuela.schmid@feinguss-blank.de
