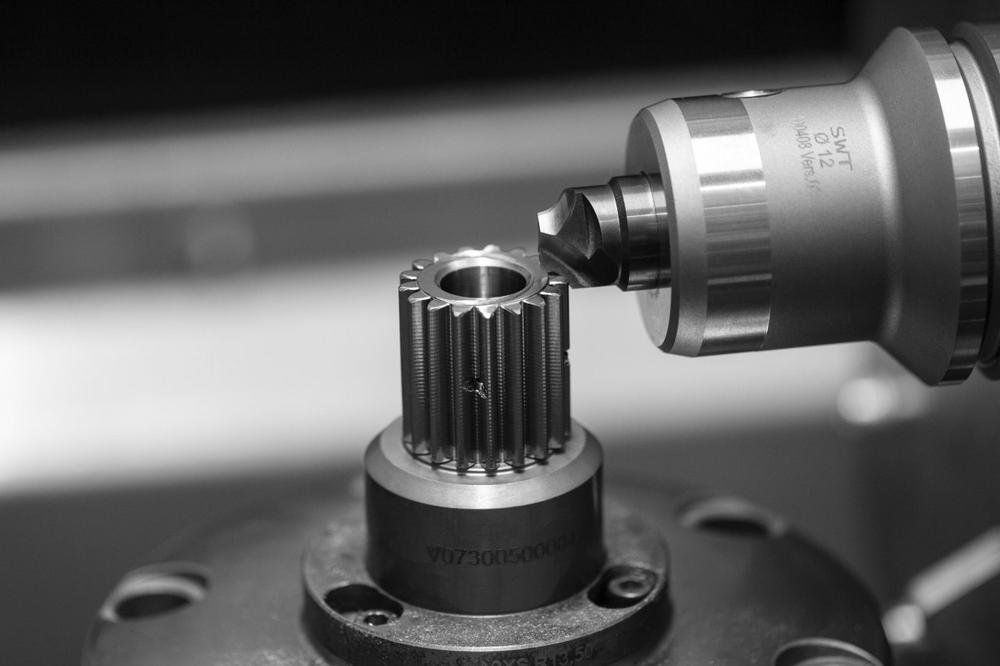
Framo Morat extends technology spectrum by adding Radial Gear Chamfering and deburring
In GearValley, nestled in Germany’s Upper Black Forest region, the traditional company Framo Morat has been producing precise gear components for a wide variety of applications for over 100 years. The range of parts includes spur gears, pinion and rotor shafts, ring gears, chain and pump gears as well as gear segments and special profiles. In a production area of 18,000 m² at the headquarters in Eisenbach, all quality-critical soft and hard machining steps are carried out in-house. In addition to turning, milling, broaching, gear cutting and grinding, Framo Morat also houses processes for heat treatment within its own four walls.
For the core competency of gearing, gear hobbing or gear shaping technologies are used, depending on the type and geometry of the components. "An ever-growing challenge is the resulting burr at the tool outlet, which can be removed with more or less difficulty depending on the geometry of the workpiece," says Stephan Bennert, Production Manager at Framo Morat. In addition, producers must cope with constantly increasing technical demands on the tooth front edge.
The logical consequence was the purchase of an RGC 350, developed by TEC for GEARS together with the Radial Gear Chamfering process. This makes it possible to create defined, reproducible chamfers on the tooth front edges, even on workpieces with interfering contours, such as multiple gears or shaft heels. The chamfering process takes place in continuous operation at high cutting speeds in an environmentally friendly way through dry cutting.
"Compared to the deburring stations or manual deburring activities used so far, the RGC 350 is superior from both a technical and economical standpoint due to its short cycle times," Bennert says. "The Radial Gear Chamfering process helps us to accelerate the overall throughput of our gear components and increase our efficiency. And all this with maximum accuracy and reproducible quality," adds Bennert.
With a footprint of approx. 2 m², the RGC 350 is extremely compact. Interlinking with a robot cell enables continuous machining. An optional brushing operation can also be carried out by the automation system without interrupting production. Thanks to the reproducible results, there is no need for constant readjustment; the machine works virtually autonomously. No in-depth programming knowledge is required to set up and convert the RGC 350. Setup is facilitated on the one hand by the good accessibility and the use of standard clamping devices, not to mention the intuitive touch display. All data required for setup is supplied together with the tool and can therefore be transferred to the machine quickly and easily.
Framo Morat is a pilot user of the Radial Gear Chamfering process and is in close contact with TEC for GEARS. Findings from daily real-world operation on the prototype of the RGC 350 flow directly into the optimization of the tools and the machine. "One factor that went into our decision was the fact that TEC for GEARS acts as a system provider by providing us with the complete process, the technology and all necessary components from one source," reports Volker Waller, Director of Operations at Framo Morat. "With the large variety of different components, some of which are highly complex, TEC for GEARS is a highly competent partner for our daily business, who actively supports us in the adaptation and further development of the machine and tools," continues Waller.
About the Franz Morat Group:
With over 100 years of experience in gear technology and drive engineering, the Franz Morat Group combines expertise in metal-cutting gear technology and plastic injection molding technology under one roof. The components and drive systems, most of which have been developed specifically for the customer, are used in such fields as mechanical engineering, rehabilitation equipment technology, intralogistics and the automotive industry. The Franz Morat Group has approximately 650 employees and operates subsidiaries in the US, Poland, Mexico and Turkey.
https://franz-morat.com/
About TEC for GEARS:
TEC for GEARS originated in an R&D project of the Baden-Wuerttemberg Cooperative State University Lörrach. The project developed the Radial Gear Chamfering process and the RGC 350 machine required for it. Thus TEC for GEARS offers its customers the process as a one-stop system provider. With selected partner companies, TEC for GEARS enables the reliable subcontracting of small, medium and large quantities, including maintenance, service and user support.
http://www.tecforgears.de/
Framo Morat GmbH & Co. KG
Franz-Morat-Straße 6
79871 Eisenbach / Hochschwarzwald
Telefon: +49 (7657) 88-0
Telefax: +49 (7657) 88-333
https://de.framo-morat.com/
Geschäftsführer TEC for GEARS
Telefon: +49 7723 92 90 959
E-Mail: info@tecforgears.de
Marketingleitung Franz Morat Group
Telefon: +49 (7657) 88-566
E-Mail: s.federer@framo-morat.com

