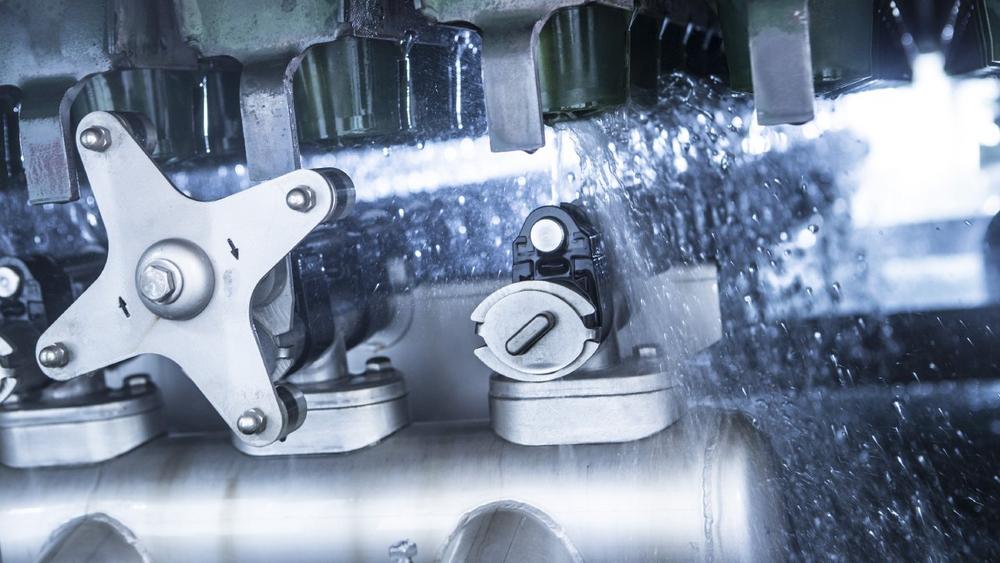
Saving millions of liters of water: KHS provides efficient systems that noticeably cut consumption
Arguably our most valuable resource, water is essential in beverage production for important processes steps such as cooling, lubrication and cleaning. Accordingly, the consumption thereof is still often high. This has also caused the industry to develop a sense of social responsibility regarding the economical use of water. “We aim to reduce the consumption of water in beverage production to an absolute minimum without neglecting the necessary standards of hygiene,” says Siegmar Stang, executive vice-president of the Filling Technology Product Division at KHS.
Here, hygienic design takes on a central role. The systems provider thus makes its machinery especially easy to clean. By eliminating dead spots, offering no-frills machine designs and using high-alloy, corrosion-resistant steel with a low surface roughness the buildup of deposits is prevented. This facilitates cleaning and shortens the duration thereof – which not only means using less water and cleaning media but also saves on energy. The cleaning intervals are also shortened.
Water no longer required
Furthermore, the new filler platforms from KHS no longer have front tables. Ducts and passages are shaped, welded seams are arranged and seals are placed in such a way as to prevent the accumulation of deposits which could possibly lead to contamination. Rinse water is also able to access all surfaces without obstruction and clean them without leaving any residue. In other areas, the machine design ensures that in terms of hygiene water can even be dispensed with entirely. For example, servotechnology and pneumatic equipment replace the wet-lubricated mechanical cam and roller parts previously used on KHS can fillers. One of the world’s biggest soft drinks producers, for instance, has now been able to reduce water consumption per liter of finished beverage from 2.86 liters to 1.61 liters over the last 15 years.
Another major lever is the multiple synergetic use of circular flows. Examples include also using heated water from the vacuum pump in the crate washer, process water in heat exchangers and evaporation energy for cooling. Limiting the amount of wastewater also reduces the carbon footprint, for water treatment is still a process that requires a considerable amount of energy. Each reduction cuts greenhouse gas emissions and ensures a better ecological balance.
Total cost of ownership in focus
The question of economics also plays an important role in the desire to save water. “The prime focus here is on the total cost of ownership,” claims Stang. “Our customers operate in high-investment supply chains with extremely large throughputs. Each and every minute of availability that takes up less time for cleaning counts; each machine downtime means lost revenue.” Thanks to the range of measures taken to reduce water consumption, KHS not only helps its customers to save on resources but also to cut their costs throughout the life cycle of the entire filling line.
In addition, regulatory frameworks are increasingly influencing water management in industry both directly and indirectly. From the CE mark and TÜV certification to the strict requirements of governments or institutional bodies, the bar for saving resources is being set higher and higher. However, it is often consumers who force companies to act; what is referred to as the ‘water footprint’ is also becoming increasingly important to them. Carlsberg, for example, has set itself the goal of reducing its water consumption in beer production by 50% by 2030. Other big players, from brewery groups to soft drink manufacturers, are making similar voluntary commitments which they intend to actually implement – also with the help of technology from KHS.
Info box
• Mixer (CSD) producing up to 72,000 liters per hour: up to 1.2 million liters of water a year saved by using a vacuum pump and applying a constant temperature in a dedicated cooling system operated as a closed circuit.
• Stretch blow molder/filler block producing 36,000 1.5-liter bottles per hour: up to 33 million liters of water a year saved by doing away with the PET rinser.
• Can filler producing 70,000 cans per hour: up to 1.2 million liters of water a year saved by water-free roller lubrication and using an expansion bellows instead of sliding seals.
• Glass bottle filler (beer, CSD) producing 50,000 bottles per hour: up to 2.5 million liters of water a year saved by the new hygienically designed bottle shower.
• Glass bottle filler (beer) producing 50,000 0.5-liter bottles per hour: up to 10 million liters of water a year saved by using a vacuum pump and applying a constant temperature through an external cooling system.
• Flash pasteurizer producing 60,000 liters per hour: up to 2 million liters of water a year saved by intelligent shift registers.
• Tunnel pasteurizer (beer) producing 105,000 0.33-liter bottles per hour: up to 25 million liters of water a year saved by speed control and a cooling tower that ensure maximum efficiency in the pasteurizer.
The KHS Group is one of the leading manufacturers of filling and packaging systems for the beverage and liquid food industries. The KHS Group includes the following companies: parent company KHS GmbH, KHS Corpoplast GmbH and numerous subsidiaries outside Germany, located in Ahmedabad (India), Sarasota and Waukesha (USA), Zinacantepec (Mexico), São Paulo (Brazil) and Suzhou (China).
KHS manufactures modern filling and packaging systems for the high-capacity range at its headquarters in Dortmund, Germany, and at its factories in Bad Kreuznach, Kleve, Worms and Hamburg, where the group’s PET expertise is pooled. The KHS Group is a wholly owned subsidiary of the SDAX-listed Salzgitter AG corporation. In 2019 the KHS Group and its 5,149 employees achieved a turnover of around €1.260 billion.
KHS GmbH
Juchostr. 20
44143 Dortmund
Telefon: +49 (231) 569-0
Telefax: +49 (231) 569-1541
http://www.khs.com
Presse- und Öffentlichkeitsarbeit
Telefon: +49 (251) 625561-243
E-Mail: deppe@sputnik-agentur.de