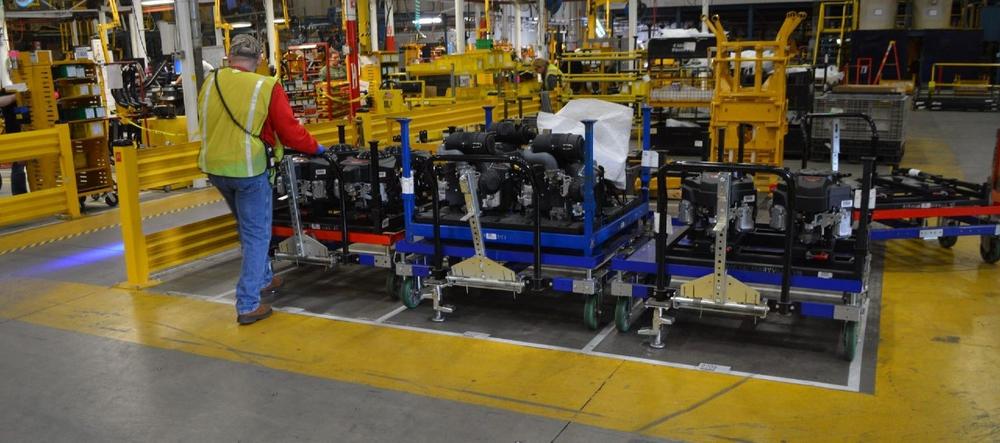
Three tips to improve your material flow
Coordinating materials and a manufacturing process in a global environment is no easy task. The flow of materials outside your own facility has many different forces that can impact it for better or worse. Managing outside suppliers (domestic & international), long distances, and other organizations all contribute to the fact that managing the flow of materials is difficult.
In this article, we will outline three strategies for you to implement to help you improve the flow of materials in your facility.
Material and Part Tracking
The first step in the process of improving your material flow is having a system for tracking all your materials. Similar to when you purchase a product off Amazon or from an E-Commerce store you receive notifications throughout the whole flow of the shipment. In most cases it works as below:
- Order Confirmation
- Shipment Notification with tracking number
- A delivery completion notification
- An after-sales follow-up
When it comes to manufacturing and industrial businesses the ordering of bulk materials becomes more complex and can be more difficult to track and monitor the flow of materials. But this is the first recommendation for improving your material flow. Ensuring you have a process of tracking and tagging all of your materials, from the moment you placed the purchase order with your supplier you should have information regarding the material flow. Once the materials have arrived at your facility, you need to have a system in place for tracking where the materials are placed within your own internal warehouse. This allows you to track the flow of your own materials from storage, to the assembly line, to delivery to your customers. Having a bird’s eye view of where your materials are at all times is the first step to improving the flow of your materials.
Using AGVs and material handling carts allows you to better improve the transportation of your materials once they arrive at your facility. Having better control of the internal transportation of your goods limits errors or misplaced goods which can lead to delays in delivery time and increased defects in your products.
Implementing Milk Run Delivery
Implementing a milk run method for delivery of parts and materials to your assembly line will give you a more organized approach to your material flow. Having a “call” or “pull” system ensures that the materials needed are delivered only once they are necessary. This can be difficult to do outside of your own facility, however, there is an increased push by large manufacturers to have their immediate suppliers located extremely close by. Having suppliers located as neighbors to your facility means that this type of pull system can be used when materials are needed within your facility. Effectively, empty containers flow from the manufacturer to the supplier and are then refilled for delivery, creating a smooth material flow between supplier and manufacturer.
However, this becomes much more difficult when your suppliers are located internationally. But setting up an internal pull system can help you monitor the flow of materials between your own warehouses/storage and the assembly line.
Efficient Material Transportation
The final strategy for improving your material flow is ensuring you have efficient transportation methods throughout every stage. So, from when your supplier ships your materials to when you ship out your final goods to your customer, the transportation needs to be safe, secure, and efficient. If you can implement a tracking system of your materials as mentioned in the first strategy it can make this third point much easier. While it is complex and costly to create an efficient global material transportation system it is easier, to begin with, your own material transportation. Moving away from less efficient forms of transportation such as manual and forklift transportations in your facilities is an excellent first step. Creating internal lines of transportation by tugger trains, AGVs, or AMRs can make your transportation much more efficient.
Tugger trains can ensure that your parts and materials are delivered to where they are supposed to be on time. You can also choose what type of material handling carts you attach to the train and thereby create a more effective way of presenting your different components. Having your materials delivered as they are needed, as well as the option of leaving carts at various stations, will help create a flowing material process. This can also be completed using automation via AGVs and AMRs.
Conclusion
Improving material flow is a way to remain competitive as a manufacturing facility. The three strategies in this article are just a few, yet vital actions to achieve a better material flow:
- Material and Part Tracking
- Implementing Milk Run Delivery
- Efficient Material Transportation
These tips are not implemented in one day, but they will affect your warehouse performance significantly. You will improve your product quality, delivery times, inventory reduction, and reduction in the number of defects. Therefore, focusing on enhancing your material flow is something you should prioritize and continuously work to improve.
What is the next step?
Start the process by focusing on what you can control; your internal processes and intralogistics. You can start by asking yourself the following questions: How do your internal processes look? What delivery methods do you use? What material handling equipment is your facility using today?
By organizing your internal processes and methods for handling, tracking, transporting, and moving material, you are up to a great start. To achieve a smooth material flow within your warehouse, ensuring that you have efficient transportations is also vital. Floor congestion, unwanted wait times, and delivery capacity all affect the flow across the shop floor. As earlier mentioned, implementing a tugger train system can play an essential role in accomplishing efficient transports. And to reach even higher efficiency, you might want to look at making some of your transports autonomous, using AGVs or AMRs. Our autonomous eQart, which is developed to be straightforward, easy to implement, and integrate with your existing material handling carts, could be one way of transforming some of your processes quickly.
FlexQube offers a unique and patented concept that is used to design and deliver robust, modular and flexible material handling carts that can also run autonomous. The company has manufacturing in Sweden and USA and distribution in North America and in Europe. On December 14, 2017, the company was listed on the Nasdaq First North in Sweden.
FlexQube has some of the world’s largest manufacturers within automotive-, energy-, defense-, aerospace-, home appliances-, and construction machinery among their customers. Some examples are Volvo Cars, Siemens, Autoliv, Scania, Whirlpool, Eberspächer and Mann+Hummel.
FlexQube GmbH
Feldbergstrasse 27-29
61440 Oberursel
Telefon: +49 (160) 2436305
http://www.flexqube.com
