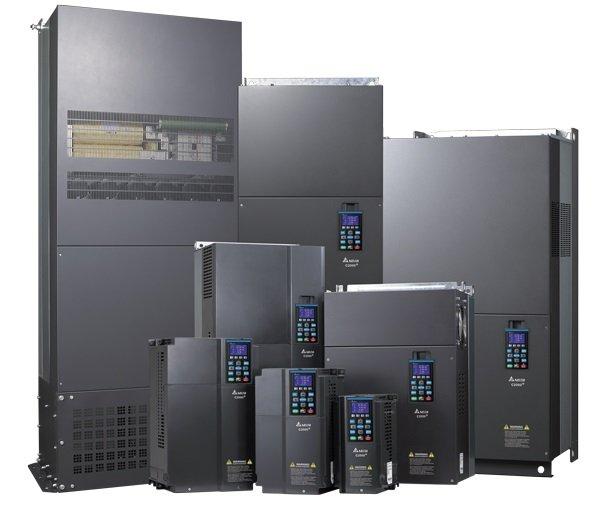
Heavy-duty AC motor drive performance at a normal-duty price point
There are AC motor drives that perform well in general-purpose applications and others for more specific scenarios such as positioning or winding and unwinding. When evaluating AC drives, the first thing to consider is the type of power, single phase or three-phase. Next, input voltage and frequency must match the facility where the drive will operate. The new C2000 Plus is a three-phase motor drive that accepts voltages of 230V and 460V and performs well across a wide range of applications including positioning, cranes, extruders, and sectional mixers.
Servo-like operation
Traditional servo systems for positioning often include a permanent magnet motor and the corresponding motor drive. A separate PLC controller regulates the speed, direction, and more. Motor speed feedback to the controller is accomplished using a tachometer generator. An encoder provides position data. The advantages of permanent magnet motors are their relative light weight and precision for applications requiring lower horsepower. The disadvantage is cost.
The new C2000 Plus AC motor drive can be used with asynchronous AC induction motors as well as permanent magnet motors for precise control of position, speed, and torque. With an integrated encoder, programmable logic controller, and pulse generator, the C2000 Plus is suitable for both sensor and sensorless motors and applications that would traditionally have called for a servo system.
The C2000 Plus also supports multiple position control functions, including homing, multi-step positioning and single positioning. These functionalities are widely used in position control applications such as smart warehouses and automatic conveyor systems.
Enhanced overload capacity
The overload capacity of the C2000 Plus has been increased to 560 kW. This is a critical advantage because it makes the drive suitable for applications in which a higher degree of overload can be expected for a short duration such as when a longer conveyor system must overcome inertia to get up to speed. The 60s overload capacity has been increased from 120% in the previous model to 150% in the C2000 Plus. This makes the new drive superior to a great number of options in the normal-duty segment and competitive with drives in the heavy-duty segment.
Built-in PLC with 10k steps program capacity
The C2000 Plus offers built-in data storage that allows users to read the PLC register of their drives using Fieldbus communications. The external PLC reads PLC data from the drive using various communication protocols and monitors the data collected from the drive. It triggers alarms if necessary.
Built-in time unit auto-conversion also allows the PLC to enable 33 kHz high-speed pulse count input. Users can calculate speed by using high-speed count input through the drive’s internal conversion without purchasing any additional hardware.
The built-in PLC determines drive status automatically. Its virtual terminal simulates a hardware interface through communications or PLC control to trigger hardware. For example, when using the built-in PLC to determine the drive status, if the drive is not in AUTO mode, the virtual terminal function can switch the drive to AUTO mode.
Users can edit PLC programming via the Ethernet interface. Instead of going on-site, users can download, upload, or monitor PLC programs at the central control.
Outstanding resistance to environmental contaminants
Environmental adaptability is more important than ever across a range of industries. The C2000 Plus now comes with improvements in many areas for significantly enhanced environmental endurance.
In the textiles industry, for instance, high temperatures and poor ventilation are common. This can make it difficult for drives to dissipate heat. Fiber can also accumulate in the heat sink, leading to overheating and faults. The heatsinks in the C2000 Plus Series have been specially designed with larger gaps between the individual blades and a polished extruded aluminum finish to prevent fiber from clogging them.
Heat dissipation is in fact important for compact drives across every industry. Beyond the heat sink, the unit’s fan plays an important role here. That’s why it must be protected accordingly. The C2000 Plus fan now offers IP55 protection (previously IP51) to maximize performance in environments where dust, oil mist, and salt mist may be present.
The PCB coating in the C2000 Plus has also been enhanced with wider spray coverage for anti-sulfur and anti-corrosion protection to comply with the IEC 60721-3-3: 3C3 standard. This standard protects the electronic components from corrosive gases (salt mist, SO2, O3, and H2S) and assures it can be operated in harsh environments such as sewage treatment facilities.
An easier, faster, and more intuitive LCD keypad interface
The new user-friendly IP66 keypad can mount directly to the control box. It provides a start wizard and lets users select applications and the display language.
The keypad also offers powerful storage for historical data and fast parameter setting. Users can quickly locate and modify existing parameters (up to 98 sets) instead of looking for them in the parameter group. Up to 30 historical error records can also be accessed to check voltage, current, frequency, DC bus voltage, or date and time.
User-defined parameters are available at the press of a button. Just enter F4 in the parameters settings page to save a maximum of 32 parameters. The Copy function saves parameters and PLC programs to the keypad memory for later transfer to another drive.
Delta provides two types of software for connecting the keypad to the PC, TPEditor and VFDSoft. The TPEditor can edit up to 256 HMI (Human-Machine Interface) pages, making the keypad a small HMI. It also lets users edit their own start-up pages and add equipment names or company logos as desired.
Motor control
The C2000 Plus supports multiple motor drives including SynRM, PMSM and IM motors. With built-in motorrelated parameter functions, users can use FOC to obtain stable speed output and optimal dynamic response. Closed-loop control (FOC PG) allows speed ratios of up to 1:1000. Open-loop control (FOC sensorless) can provide speed ratios of up to 1:100.
Motor-related parameters vary with temperature and current. The C2000 Plus performs online tuning for motor parameters based on these physical characteristics to enhance the motor’s control performance.
System applications
In the textile industry, the motor often coasts to a stop when the mains electricity experiences an outage. This can lead to yarn breakage or insufficient twisting for double twisting. Deceleration energy backup (DEB) allows the C2000 Plus to regenerate DC bus voltage so the drive can ramp down the motor to a stop, avoiding re-splicing or rewinding for the factory.
It’s not possible to mount external brake resistors on large industrial fans. Instead, traction energy control is used to dissipate the energy generated by DC bus voltage during ramp-down with large load inertia. This enables quick deceleration without a brake resistor.
Applications in construction and building materials often involve heavy loads. Pipe jacking machines, sandstone crushers, and heavy-duty slat feeders are good examples. In this environment, the master-slave method allows for load sharing. Here, the master axis controls the speed and sends torque commands to the slave axes to balance the load.
New possibilities
What will industrial and manufacturing firms do with a new AC motor drive that allows for servo-like operation and heavy-duty performance at normal duty pricing? The food, chemicals, metalworking, rubber, and plastics, industries as well as municipal infrastructure and more will benefit from the flexibility, fast communications, and enhanced overload capacity of the C2000 Series. Applications that were previously deemed cost-prohibitive can now be re-analyzed considering this new price-performance level. For companies seeking to expand, new production lines can offer greater efficiency and an advantage over the competition. Whatever the application involves, be it winding, positioning, or other types of variable speed and torque applications, Delta now has an excellent solution that offers dramatically improved performance.
Delta, founded in 1971, is a global leader in switching power supplies and thermal management products with a thriving portfolio of smart energy-saving systems and solutions in the fields of industrial automation, building automation, telecom power, data centre infrastructure, EV charging, renewable energy, energy storage and display, to nurture the development of smart manufacturing and sustainable cities. As a worldclass corporate citizen guided by its mission statement, "To provide innovative, clean and energy-efficient solutions for a better tomorrow," Delta leverages its core competence in high-efficiency power electronics and its CSR-embedded business model to address key environmental issues, such as climate change. Delta serves customers through its sales offices, R&D centres and manufacturing facilities spread over close to 200 locations across 5 continents.
Throughout its history, Delta has received various global awards and recognition for its business achievements, innovative technologies and dedication to CSR. Since 2011, Delta has been listed on the DJSI World Index of Dow Jones Sustainability™ Indices for 8 consecutive years.
In 2017, Delta was selected by CDP (formerly the Carbon Disclosure Project) for its Climate Change Leadership Level for the 2nd consecutive year. For further information about Delta, please visit www.delta-emea.com.
Delta Electronics (Netherlands) B.V.
Zandsteen 15
NL2132MZ Hoofddorp
Telefon: +31 (20) 8003900
Telefax: +31 (20) 8003999
http://www.delta-emea.com/
Mepax
Telefon: +34 (619) 0277-78
E-Mail: m.depablos@mepax.com

