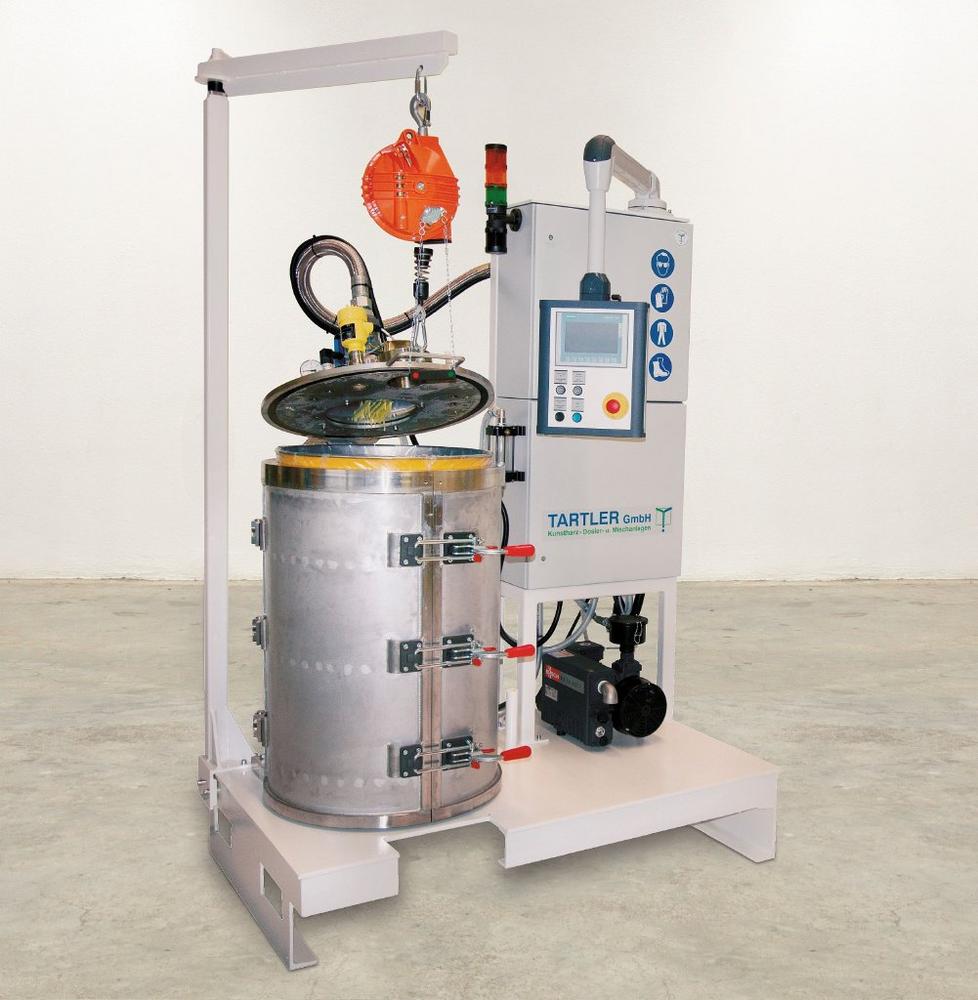
Mehr Nachhaltigkeit in der Rotorblattproduktion
Bei der Produktion von Rotorblättern für Windkraftanlagen werden allein beim Verkleben der bis zu 85 Meter langen Flügelhalbschalen große Mengen von Kunstharzen verarbeitet. Für das weitgehend automatisierte Dosieren, Mischen und Applizieren der meist hochviskosen Pasten rüstet die TARTLER GROUP seit bald drei Jahrzehnten namhafte Hersteller der Branche mit den modularen Mehrkomponenten-Anlagen seiner Baureihe Nodopox aus. Seitdem das Unternehmen vor etwa sechs Jahren auch die Entwicklung vakuumbasierter Entgasungsstationen startete, eröffnet es den Rotorblatt-Produzenten zudem die Möglichkeit, ihre Kunstharz-Verarbeitung erheblich material- und kostensparender zu gestalten. Technologische Maßstäbe hinsichtlich einer nachhaltigen Prozessoptimierung setzen hier inzwischen die neuen Vakuumanlagen TAVA 200 F. Denn durch das blasenfreie und vollständige Ab- und Umfüllen der Kunstharze in Deckelfässer machen sie den Weg frei für das sichere Materialhandling und die Realisierung ressourcenschonender und kostensenkender Aufbereitungsund Kreislaufprozesse.
Entgasungsstation senkt Materialverlust
Lange Zeit gehörte es zu den ständigen Ärgernissen bei der Rotorblatt-Produktion, dass sich größere Mengen sortenreiner Harzreste – aus angebrochenen Fässern oder aus der Rüstphase – nicht weiter- oder wiederverwenden ließen. Sie mussten ausgemustert und entsorgt werden, was auf der Kostenseite negativ zu Buche schlug und allen Ansätzen für einen nachhaltigen Umgang mit dem Material zuwiderlief. Mehrere Vor-Ort-Analysen der TARTLER-Ingenieure hatten beispielsweise zu Tage gefördert, dass selbst bei sach- und betriebsgerecht geleerten Fässern immer noch bis zu 14 kg Material in deren Foliensack (Inliner) zurückbleiben – deutlich sichtbar nach den Fasswechseln in den Dosierund Mischanlagen. Des Weiteren bleiben aus der Prüfung und Qualitätskontrolle der Mischungsverhältnisse ebenfalls etliche Kilogramm neuwertiger Werkstoff übrig – pro Rotorblatt! Hinzu kommen Restmengen aus Spülungen, Überschüssen und anderen Nebenarbeiten. Bislang aber ließ sich das an den verschiedenen Stellen anfallende Restmaterial nicht einfach wieder in die Produktion zurückführen. Der Grund: Beim Einfüllen in die Deckelfässer entstehen Lufttaschen, Luftblasen und somit auch Feuchtigkeit im Material. Bei einem Eintrag dieser „Störluft“ während der Entnahme, Förderung und Dosierung des Materials in die Pumpe der Dosier- und Mischanlage würde der Verarbeitungsprozess massiv behindert. Verfahrensabbrüche wären die Folge und das komplette System müsste (mehrfach) mit Material freigespült werden, bis es wieder luftfrei und einwandfrei arbeiten würde. All dies ginge einher mit erheblichen Materialverlusten und weiteren Kosten, da vorgefertigte Bauteile erneuert und vorgelagerte Prozesse aufwändig gereinigt werden müssten.
Materialreste zurückführen
Mit der Entgasungsstation TAVA 200 F bietet die TARTLER GROUP einen Ausweg aus diesem Dilemma. Denn mit diesem System lassen sich sowohl flüssige als auch pastöse Reste ohne „Störluft“ in Deckelfässer einfüllen und anschließend verlustarm und sicher wieder in den Verarbeitungsprozess einschleusen. Die auf diese Weise erzielten Einsparungen im Materialeinkauf können beachtliche Dimensionen erreichen. Einer der führenden Hersteller von Windkraftanlagen konnte seinen Kunstharz-Verbrauch durch den Einsatz der TAVA 200 F jüngst um etwa 28 Tonnen Kunstharzpaste jährlich reduzieren und so die Gesamtkosten in seiner Rotorblatt-Produktion erheblich senken. Damit wirkt er zugleich der Verschwendung entgegen und leistet einen stattlichen Beitrag zur Ressourcenschonung. Außerdem verbessert er die Ökobilanz seiner Wertschöpfungskette und verkleinert den ökologischen Fußabdruck seines Unternehmens.
Prozessintegrierter Kreislauf
Die Prozesse im sogenannten „Blade Bonding“ hat der angesprochene Rotorblatt-Hersteller insoweit optimiert, dass er eine TAVA 200 F fest in seine Kunstharz-Verarbeitung integriert hat. Hier werden die gesammelten Materialreste in betriebsübliche Spanndeckelfässer ein- und umgefüllt, entgast und von jeglicher Störluft befreit. Sobald ein Fass vollständig mit re-konditioniertem Material befüllt ist, lässt es sich wieder in einer 2KNodopox-Anlage (oder einer ähnlichen Maschine) zum Dosieren, Mischen und Auftragen des Kunstharz-Klebstoffs einsetzen. Auf diesem Weg kann der Hersteller fast alle unvermischten Materialreste wiederverwenden. Und nach Berechnungen von TARTLER lässt sich der Return-of-Investment bereits nach weniger als 24 Monaten erreichen. Erfreulicher Nebeneffekt: Da die Abfallmenge sinkt, schrumpft auch die Gebührenlast für deren Entsorgung.
Luftfrei bei YouTube
Kundengerecht konfiguriert und ausgeliefert wird die TAVA 200 F von SOMATA, einer Unternehmenstochter der TARTLER GROUP. Die Entgasungsstation wird serienmäßig für die luftfreie Ab- und Umfüllung von 200und 50-Liter-Fässern angeboten, auf Kundenwunsch aber auch auf andere Gebindegrößen angepasst. Sie besteht aus einer Vorrichtung zum Einspannen und Stabilisieren des Fasses, einem speziellen Kombiaufsatz zur synchronisierten Vakuumerzeugung und Befüllung, einer Vakuumpumpe und einer Steuerung mit Touchscreen. Alle Komponenten sind rundum zugänglich auf einem Sockel mit Fasszentrierplatte installiert. Während das Beschicken der Station, das Positionieren eines noch leeren Fasses und das Schließen der Spannvorrichtung manuell erfolgen können, laufen die Vakuumbeaufschlagung des Fasses und das nahezu gleichzeitige Einfüllen des Materials vollautomatisiert ab. Nach wenigen Minuten ist ein Fass luftfrei befüllt und steht für den Einsatz in der Produktion bereit. Anschaulich in Szene gesetzt ist dieser Ablauf in einem Video im YouTube-Kanal von SOMATA.
SICHERE UND RESSOURCENSCHONENDE PROZESSE
Über die TAVA 200 F hinaus bietet die TARTLER GROUP drei weitere Systemlösungen für die Entgasung hoch- und niederviskoser Materialien an. Es sind dies die Fasswechselanlage TAVA D sowie die Evakuierungsanlage T-EVAC in ihrer Offlineund Inline-Konfiguration. Sie alle basieren auf der Vakuumtechnik und dienen dem Ziel, das Handling pastöser und dünnflüssiger Medien von Störluft und Feuchtigkeit zu befreien – sowohl beim Abfüllprozess als auch bei der Zuführung in die Verarbeitungsanlage. Wie am Beispiel der TAVA 200 F gezeigt, lassen sich die Systeme außerdem zur produktionsintegrierten Re-Konditionierung von Materialresten, zur gezielten Abfallreduzierung und zur Realisierung von betriebsinternen Materialkreisläufen einsetzen.
TARTLER GmbH
Relystr. 48
64720 Michelstadt
Telefon: +49 (6061) 9672-0
Telefax: +49 (6061) 9672-295
https://www.tartler.com
Marketing Leiterin
Telefon: +49 (6061) 967211
E-Mail: n.kalt@tartler.com

