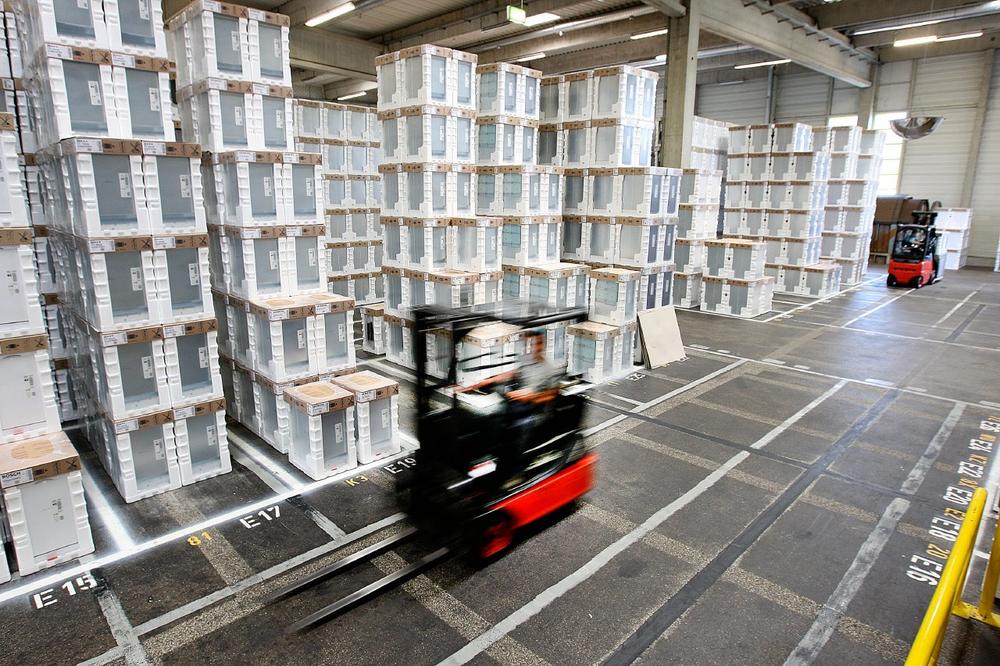
Proven packaging, reduced carbon footprint: BSH uses BASF’s Styropor® packaging based on chemically recycled plastics for the first time
- Helping to close the plastic loop and contributing to the sustainability strategy of both companies
- High-quality transport packaging for sensitive electric appliances still guaranteed
- Styropor® Ccycled™: alternative to fossil raw materials used for home appliances from the BSH Group
What began at a major plastics fair and as a pilot project at the end of 2019 has led to a successful cooperation. From 1 April 2021, BSH Hausgeräte GmbH will for the first time use Styropor® based on a raw material made from chemically recycled plastic waste as a packaging material for selected large appliances of its luxury brand Gaggenau.
BSH is initially testing the Styropor® packaging made from recycled material at its Dillingen production site in Germany. The ambitious objective is to use this type of resource-efficient packaging for all large appliances worldwide. “At BSH, our goal is to improve the quality of life. This also includes conserving natural resources and helping to reduce waste and pollution. We’ve already made major progress in this respect. As Europe’s leading home appliance manufacturer, we have been developing and manufacturing all our products worldwide carbon-neutral at our locations since the end of 2020. But we do not stop there. As a society, and therefore also we as a company, need to move away from a throwaway mentality and towards more understanding of resources and materials. Turning something old into something new and thus avoiding waste is therefore a core element of BSH’s circular economy approach. By using Styropor® packaging, for which the raw materials come from chemical recycling, we are actively contributing to our sustainability goals and the industry-wide circular economy. We are delighted to have BASF, a long-standing, experienced partner, at our side, helping us to achieve these goals,” says Silke Maurer, Chief Operating Officer at BSH Hausgeräte GmbH.
Virgin-quality packaging—smaller carbonfootprint
Due to its manufacturing process, Styropor® Ccycled™ has the same properties as conventional Styropor®. This maintains the excellent packaging properties such as excellent impact absorption and high compressive strength, which are essential for the protection of sophisticated home appliances. In the production of the packaging foams that have become so well-known over the last 70 years, pyrolysis oil has merely replaced fossil raw materials. BASF’s partners extract this oil from plastic waste that would otherwise be used for energy recovery or go to landfill. BASF then uses the required amount of oil to manufacture new plastics at the start of the value chain.
Since recycled and fossil raw materials are mixed in production and cannot be distinguished from each other, the recycled portion is allocated to Styropor® Ccycled™ using a mass balance approach. Both the allocation process and the product itself have been certified by Ecoloop, an independent certification programme. Compared with conventional Styropor®, at least 50 percent of CO2 is saved in the production of Styropor® Ccycled™ packaging.
Closing the loop—conserving resources—protecting the environment
“Current environmental policy focuses on reducing greenhouse gas emissions, conserving fossil resources, and avoiding or using waste. By using products from our ChemCycling™ project, our partner BSH is actively contributing to the recovery of plastics after their use phase and feeding them back into the materials loop,” says Klaus Ries, head of BASF’s Styrenics business in Europe.
In the future, BASF and BSH plan to strengthen their cooperation by examining the use of alternative raw materials along additional value chains and finding solutions to close the plastics loop in these areas. This includes taking further recycling processes into consideration. As uncontaminated Styropor® packaging waste can be mechanically recycled extremely well, this type of recycling is already used widely today and will be stepped up further over coming years.
Read more about BASF’s ChemCycling™ project here.
About BSH
With sales of approximately €13.2 billion in 2019 and 58,000 employees, BSH Hausgeräte GmbH is one of the world’s leading companies in the home appliance sector. Alongside the Group’s 11 well-known home appliance brands such as Bosch, Siemens, Gaggenau, and Neff, its brand portfolio also includes the Ecosystem Brand Home Connect and three Service Brands, including Kitchen Stories. BSH manufactures in 38 factories and is present in around 50 countries. BSH is a Bosch Group company.
At BASF, we create chemistry for a sustainable future. We combine economic success with environmental protection and social responsibility. More than 110,000 employees in the BASF Group contribute to the success of our customers in nearly all sectors and almost every country in the world. Our portfolio is organized into six segments: Chemicals, Materials, Industrial Solutions, Surface Technologies, Nutrition & Care and Agricultural Solutions. BASF generated sales of €59 billion in 2020. BASF shares are traded on the stock exchange in Frankfurt (BAS) and as American Depositary Receipts (BASFY) in the U.S. Further information at www.basf.com.
BASF SE Kommunikation BASF-Gruppe
Carl-Bosch-Straße 38
67056 Ludwigshafen
Telefon: +49 (621) 60-0
Telefax: +49 (621) 60-42525
http://www.basf.com
BASF media contact
Telefon: +49 (621) 60-58772
E-Mail: sven.heppes@basf.com
BSH media contact
Telefon: +49 (89) 4590-5814
E-Mail: julia-henry@bshg.com
