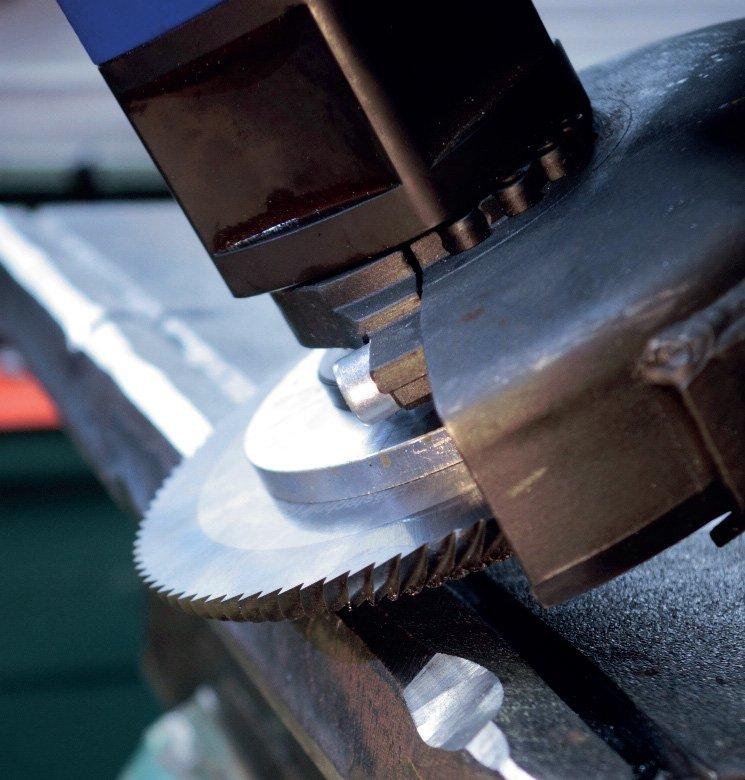
Milling instead of grinding – with the hand angle miller – versatile and flexible
For all of those the following applies:
The surfaces processed with the discs are metallic bright, and therefore prevent cavities while welding. While working, the discs produce neither (unhealthy) dust nor heat, and thus no structural changes that come with heat. The amount of material removed and the fineness of the result depend on the toothing. The fewer teeth, the coarser the chips and the greater the amount of material removed. The more teeth a disc has, the finer the chips and the smoother the surface, but less material is removed. The specific toothing depends on the material to be machined and the disc size. An overview of the common teeth of various materials and disc types can be found on pages 8-11 of our product flyer. Further toothings for special purposes can be developed in cooperation with the customer if required.
The discs can be used for the following tasks:
- The milling disc gets used for beveling, deburr and flatten as well as working out weld roots.
- The double sided milling disc (DMD) is used to open weld roots, according to the literal translation of the German original description, that would be “weld root opener”. Due to the teeth geometry, it is not made for the tasks performed by a single sided milling disc.
- The Doubleworker (DW) combines the scope of single and double sided milling discs, without the need to frequently change the tools. The teeth geometry of the double sided milling disc had been adjusted to resolve the problem of chips getting stuck in the chip chamber.
At some points, milling by hand is very different from grinding or polishing with an angle grinder.
Due to the weight of the milling discs, little / no pressure is required to mill, and the machine takes over the work of the forward movement. The work of the craftsman focuses on operating and guiding the machine.
While it is unusual or even dangerous to tilt the tool to the side when working with cutting discs, this can be done with the milling discs without any risks. In the case of the double sided discs, it is even a common technique to increase the opening angle by tilting the disc.
When milling by hand, other speeds for machines are recommended than those used for grinding. While approx. 12,000 rpm are recommended for milling aluminum with 125 mm discs, for milling steel and stainless steel usually only 1,250 – 2,800 rpm are recommended. These low speeds are no longer feasible with an angle grinder, which is why angle millers / angle polishers are used for this.
For optimal performance, we recommend the compressed air machines developed by us and produced by the company Deprag CZ. These machines can be purchased directly from us or our local dealers.
Besides these tool from Deprag CZ, we also use various angle polishers from Dynabrade when using compressed air.
When using machines not sold by us, especially electrical ones, there are a few points to consider:
- Since the forces affecting carbide discs differ from those on cutting / grinding wheels, we recommend guards with a thickness of at least 2.8 mm. All machines we deliver will be equipped accordingly if necessary.
- Also due to the forces affecting, use on machines without metal gears is not recommended. During tests we noticed that the plastic gearbox usually suffered a gearbox damage after a few minutes.
Based on the long service life, the discs can also be used in (partially) automated processes.
A height-adjustable milling carrier for 116 mm and 125 mm milling discs is already available. With this carrier it is possible to remove a weld seam to a certain height, or to work out a slight indentation. At one customer, this has already been successfully combined with a robotic arm and enables the fully automatic removal of weld seams to a certain height. There is currently an adapter for the Deprag CZ machines to be fixed on the carrier. The adapter can be developed for other machines if required.
Another option is to use a pendulum arm on a rail, which can be used to open a weld seam evenly in several passes.
The work aids, both the milling carrier and the pendulum arm, can be used location independent. This means, the work aids, equipped with a one or double sided milling disc, can be used on site on the component.
As already mentioned for the milling carrier, the milling discs can also be used in fully automatic operation. For this purpose, the milling disc can be integrated into an automated process either directly or with a machine and, if necessary, work aids.
Note: This article got updated. It previously contained information, that a finishing is required when using the discs. This is not correct, surfaces processed with any of our milling discs do not require a finish or any kind of polishing.
Maija-Frästechnik GmbH, founded in 2012, develops, produces and sells high-quality milling tools made of hard metal. The company owns the patent for milling discs, which was registered in 2000 by the later company founder.
Today it supplies the metalworking industry worldwide in a wide variety of sectors, including ship and yacht construction, container construction, commercial vehicle construction, rail vehicle construction and foundries.
The milling discs were awarded with the German prize for resource efficiency in 2015 – the Federal Ministry of Economics and Technology honored Maija-Frästechnik GmbH for the efficient use of limited resources in 2015.
Ministry and experts were convinced about the recyclability of the milling chips, which – in contrast to abrasive dust – can be reused without major effort.
Maija Frästechnik GmbH
Kölner Straße 199
58256 Ennepetal
Telefon: +49 (2333) 86977-05
Telefax: +49 (2333) 86170-62
http://www.maija-fraestechnik.de/
CEO
Telefon: +49 (2333) 86977-05
Fax: +49 (2333) 86170-62
E-Mail: m.haertel@maija-fraestechnik.de

