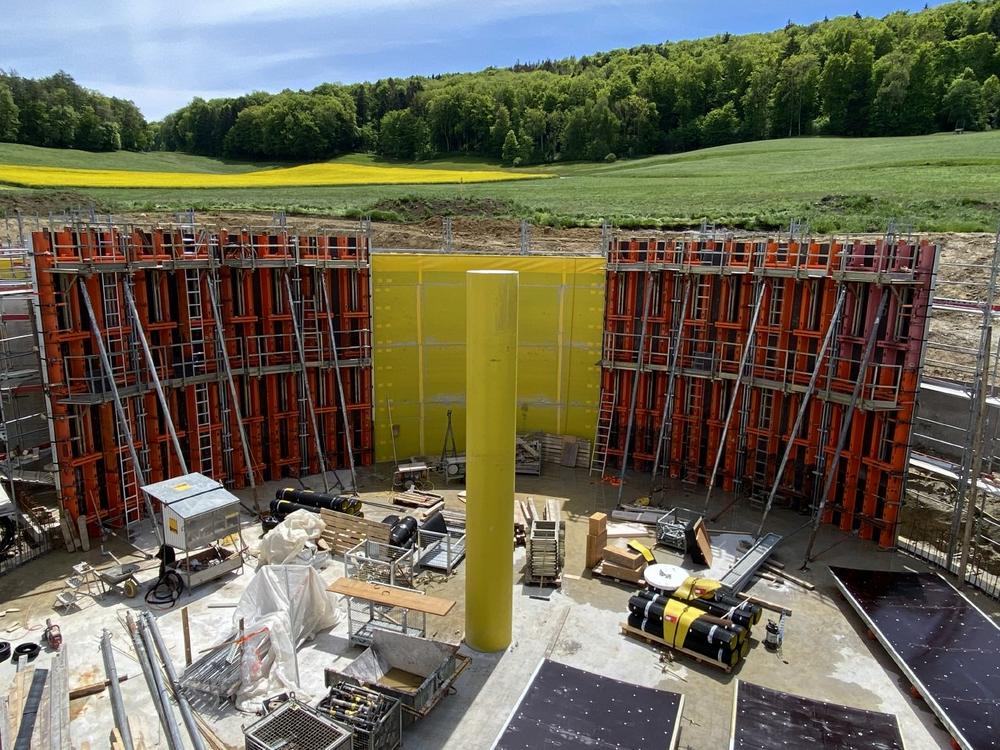
Circular reinforced concrete constructions for biogas plants formed quickly and safely with PASCHAL
The biogas plant turns liquid manure into energy
As a large livestock unit, the agricultural village of Höfli has a lengthy tradition, stretching back as far as March 1956. The long-term tenants approached the owners back in 2014 to discuss the topic of liquid manure. From that moment onwards, they worked together on planning and implementation, with a view to effectively combining agriculture with generating energy.
The first building permit for a small plant was granted in 2016. The owners and tenants then decided to construct a larger plant with a capacity of 250 kW.
A fermenter, the secondary fermenter, pipework and the plant building are currently under construction. For environmental reasons, underground pipework for liquid manure has already been installed and routed to neighbouring farms to ensure the constant supply of biomass. Once operational, the biogas plant will ferment the organic substances, including manure and liquid manure, from the farms into gas. That biogas will then be converted to heat and chiefly fed into the public grid as green energy.
The heart of the biogas plant – the fermenter and the secondary fermenter
The two circular reinforced concrete constructions were formed and cast by Stutz AG in eight concreting cycles over six weeks using the circular formwork system TTK – circular trapezoidal girder formwork with clamp connection. For efficient and reliable reinforcement and concreting, the inner TTK – circular trapezoidal girder formwork was combined with the Multip and served as a safe working platform.
The responsible foreman, Adrian Gantenbein, is fully satisfied with PASCHAL in terms of work preparation, logistics and the formwork system.
At the site meeting in mid-June 2021, Adrian Gantenbein particularly emphasised the practical handling and easy implementation of the large TTK formwork units during concreting, with formwork heights of 637.5 cm for the secondary fermenter and a formwork height of 750 cm for the fermenter.
‚The easy handling of the pre-rounded, large TTK formwork units with practical clamp connection are one of the main reasons for the record-breaking construction time of just under six weeks,‘ explains Adrian Gantenbein.
Consistently compatible for real efficiency
The consistency of the system compatibility at PASCHAL is clearly demonstrated by the combination of the TTK – trapezoidal girder formwork with clamp connection and the Multip. The functional working platform meets the most stringent of safety standards laid down by the BauBG (BGR 187) and enhances the efficiency of work when forming and concreting.
Assembly on the formwork is performed quickly, easily and safely with the formwork panel lying on the ground, thus minimising the potential for hazardous situations. After the Multip has been secured to the
formwork, the system merely needs to be unfolded.
Ladders, boards and railings are, of course, included in the folding system unit so that it can be transported and set up on site without requiring extra assembly or additional components.
The setting and releasing of connecting pieces, the attaching or removing of crane attachments and also the releasing of fixed anchorages can be carried out quickly
and safely. The Multip simply remains attached when the formwork units are moved.
‚If everything goes to plan, as it did with the circular reinforced concrete constructions, the plant should be connected to the grid by the end of June 2022,‘ explains site manager Kevin Kollbrunner of Stutz AG.
PASCHAL-Werk G. Maier GmbH
Kreuzbühlstr. 5
77790 Steinach
Telefon: +49 (7832) 71-0
Telefax: +49 (7832) 71-209
http://www.paschal.de
PR
Telefon: +49 (7832) 71-237
E-Mail: katja.muench@paschal.de

