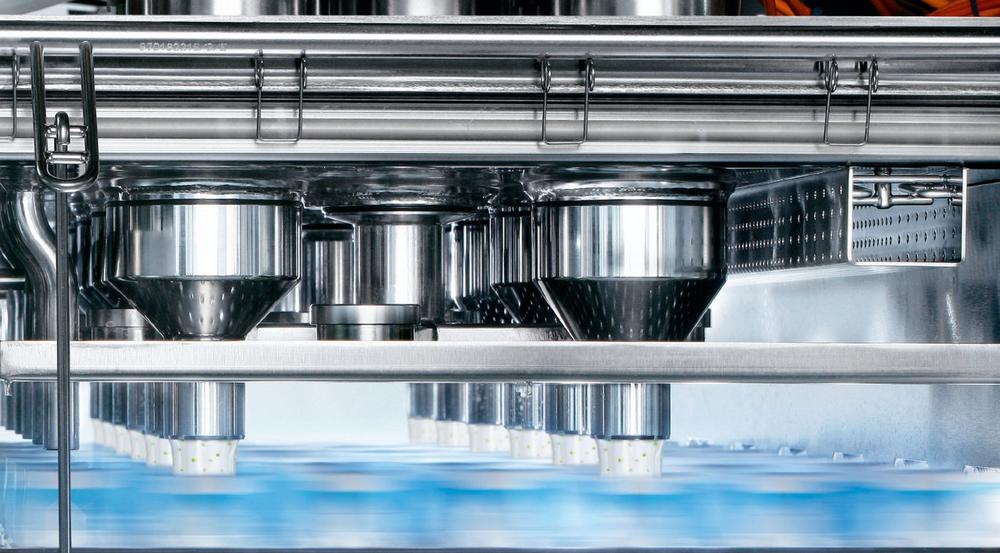
SIG to deliver even more plant flexibility and efficiency with digital recipe management and automatic changes
Digital recipe management enables automatic recipe synchronisation across all relevant parts of the filling line including the downstream. For manufacturers, this means a significantly faster change to the next lot or product, considerably more flexibility in the production process, and ultimately helps to ensure a smarter and more connected filling plant.
Stefan Mergel, Senior Product Manager Equipment at SIG: “In today’s food and beverage plants, production lines need to be more flexible, agile and intelligent to handle new challenges and demands. This can only be achieved by securing greater asset optimisation, which means configuring the optimal long-term infrastructure to flexibly handle any operational demand. And by ensuring intelligent recipe and job handling throughout production.”
SIG’s new built-in capability also means that the latest downstream equipment for SIG filling lines can now make automatic format and volume changes. This seamless integration ensures manufacturers can utilise the full flexibility potential of their filling machines and is yet another way in which the company is helping its customers achieve digital transformation.
SIG’s digital recipe management is enabled through the PLANT 360 Connector. This advanced monitoring and control solution was designed to optimise every part of food and beverage production by gradually integrating all plant processes and systems into one platform, no matter the equipment, supplier or PLC used.
Stefan Mergel: “With SIG PLANT 360 Connector you can integrate the complete filling line – including R-CAM, filling machine and downstream – into the customers’ digital platforms. This ensures you can gain full bi-directional connectivity from shop floor to the top floor.”
Recipe management in a filling plant comprises a number of processes, including defining the product category to be filled and in which packaging format, as well as the number of packs needed and which closures to use. To date, many manufactures have relied upon paper-based recipe management processes. This handling not only results in more manual work but leaves manufacturers vulnerable to the risk of human error.
Bi-directional digital recipe management was developed through SIG’s solution-based Smart Factory platform – a drive to deliver IoT-enabled systems and technical services that transform filling plants into connected factories delivering greater efficiency, flexibility and quality. Now, with this innovation, SIG customers are set to achieve even more flexibility and efficiency in their production process.
SIG is a leading systems and solutions provider for aseptic carton packaging. We work in partnership with our customers to bring food and beverage products to consumers around the world in a safe, sustainable and affordable way. Our unique technology and outstanding innovation capacity enable us to provide our customers with end-to-end solutions for differentiated products, smarter factories and connected packs, all to address the ever-changing needs of consumers. Sustainability is integral to our business and we are going Way Beyond Good to create a net positive food packaging system.
Founded in 1853, SIG is headquartered in Neuhausen, Switzerland. The skills and experience of our approximately 5,900 employees worldwide enable us to respond quickly and effectively to the needs of our customers in over 60 countries. In 2020, SIG produced 38 billion carton packs and generated €1.8 billion in revenue. SIG has an AA ESG rating by MSCI, an 18.8 (low risk) score by Sustainalytics and a Platinum CSR rating by EcoVadis. For more information, visit www.sig.biz For insights into trends that drive the food and beverage industry and inspire us to innovate, visit our SIGnals blog: https://www.sig.biz/signals/en
SIG Combibloc
Rurstraße 58
52441 Linnich
Telefon: +49 (2462) 79-0
Telefax: +49 (2462) 79-2519
http://www.sig.biz
Press Officer
Telefon: +49 (2462) 79-2608
Fax: +49 (2462) 7917-2608
E-Mail: heike.thevis@sig.biz

