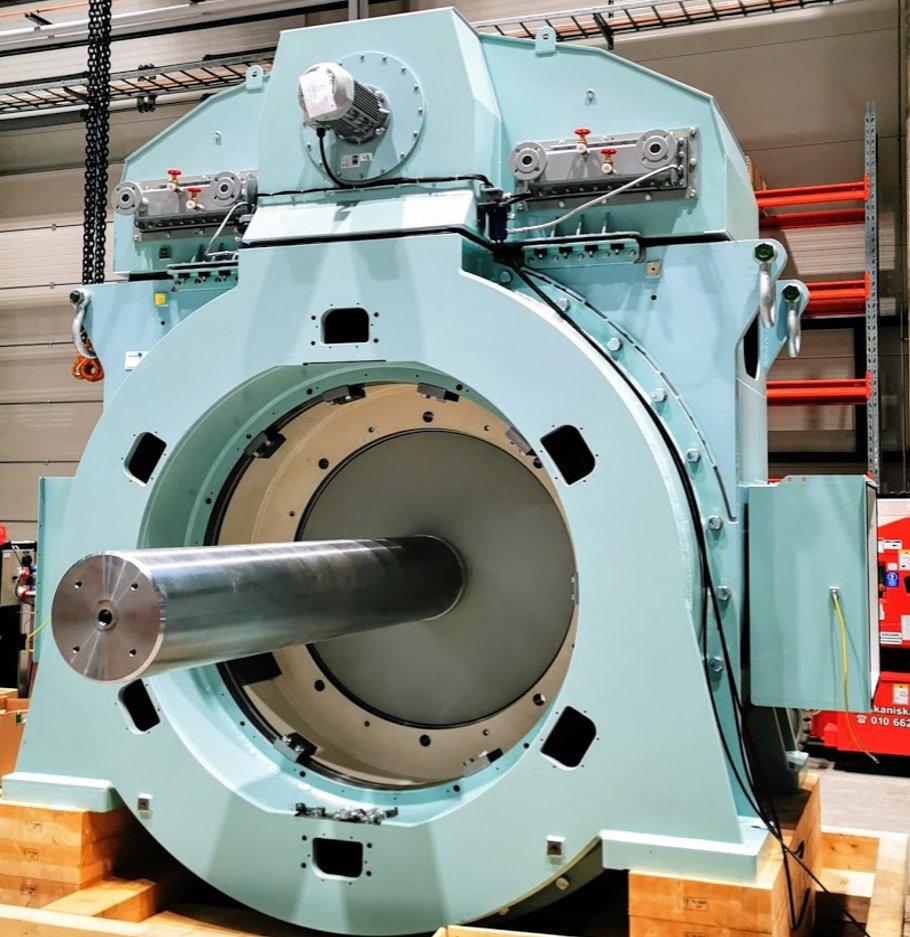
The Switch sweeps past ‚magic‘ milestone of 100 in-line PMM shaft generators sold
A peek in the past
Shipboard electrical power generation has traditionally been performed by separate auxiliary gensets not connected to the main engine. One positive of auxiliary gensets is they don’t require power electronics for frequency conversion when driven in constant-speed mode. However, they have higher specific fuel-oil consumption (SFOC) compared to the main engine, and they can’t run on cheap heavy fuel oil (HFO) without additional equipment – meaning higher maintenance.
Shaft generators muscle in
One of the best alternatives to supercharge energy efficiency in line with the IMO’s goal to drastically reduce emissions from shipping is to use variable-speed shaft generators, where electric power is produced by the vessel’s 2-stroke main engine. These have typically been electrically excited synchronous generators (EESG) where the EESG is mechanically connected to the main shaft and electrically connected to the ship’s grid.
Connection to the power grid is either through a frequency converter or direct, in which case only fixed speed is possible. The EESG system is also complex, requiring additional kit such as a brushless exciter or slip rings and an automatic voltage regulator (AVR) to supply rotor current. Crucially, losses in the rotor winding reduce efficiency while EESGs are also physically large with high rotating inertia.
The new PM wave
Step in PMM generators, which although invented a century ago have proven their worth and versatility in modern applications ranging from distributed power generation and wind turbines to elevators and hybrid cars. Uptake in shipping has been quite slow due to low awareness of their immense benefits but they’re becoming increasingly popular. Here’s why replacing direct-driven EESGs with PMMs provides the winning benefits of higher efficiency, reliability and flexibility.
No need for magnetization
Firstly, an EESG’s magnetic field is produced with electromagnets that need external energy for magnetization, lowering efficiency and increasing main-engine fuel burn. In contrast, PMGs feature strong Neodymium magnets that don’t require external energy for magnetization, resulting in 2%-3% higher efficiency across the entire operating range. That means less fuel burn, lower emissions and overall reduced Opex. Fuel burned in the main engine to produce electricity in EESGs often makes up more than 95% of overall generator lifetime costs, so this difference in efficiency can trigger huge lifetime savings.
Minimum components and maintenance
Secondly, PMMs are much more compact and mechanically simpler in construction than EESGs, meaning greater long-term reliability and far less maintenance. There’s no additional kit such as exciters, slip rings or AVRs to worry about that require maintenance and pose a risk of failure.
Dynamic performance
The third benefit is the PMM’s extremely low inertia and weight. This is related to the simple rotor construction. The EESG features a heavy solid-steel rotor with massive field poles and windings attached. In comparison, the PMG rotor is a hollow steel cylinder with magnets fixed on its surface. This has direct positive effects on the dynamic performance of the whole shaft line, including torsional vibrations and design flexibility for the ship. They’re lighter to handle and easier to accommodate, freeing up vital space.
Frequency converters top it off
Coupling a PMM with a frequency converter seamlessly gives the maximum amount of freedom in optimizing engine and propeller efficiencies. Variable-speed operation combined with a controllable-pitch propeller results in the best overall efficiency since efficiency of both the main engine and propeller can be optimized separately depending on load conditions.
Slow speed advantage
While the efficiency premium of PMM in geared, high-speed applications is typically only around 1% higher compared to conventional machines, they have significantly better efficiency in partial load/slow-speed applications (also where induction [asynchronous] machines are used in shaft generators – see white paper here). That’s why they’ve become a standard choice in large LNG and LPG carriers that typically use in-line shaft generators.
Bright future
“We’ve made it to over 100 in-line PMMs mostly for LNG and LPG carriers but also products tankers and car carriers, which is tremendous. People are starting to see what I call the ‘magic’ of permanent magnets and realising how it can accelerate the shift to enhanced performance and sustainability. We’re targeting many more PMM-powered generators and direct-drive propulsion solutions in the coming years so the story will only get better,” said Puranen.
Yaskawa Environmental Energy / The Switch focuses on electrifying the world with game-changing green technologies. Our innovative electrical drive train products, capabilities and solutions convert energy sustainably, store energy effectively and consume energy responsibly. Today, we have over 16 GW of megawatt-class environmental energy technology delivered for leading energy pioneers throughout the world. We’re on a mission to enable more profitable power generation, energy storage and use, while lowering the cost of electricity, operations and emissions. For more information, visit: www.theswitch.com
YASKAWA Europe GmbH
Philipp-Reis-Str. 6
65795 Hattersheim am Main
Telefon: +49 (6196) 569-300
Telefax: +49 (6196) 569-398
http://www.yaskawa.eu.com
Marketing Communications Specialist
Telefon: +358 (50) 554-5044
