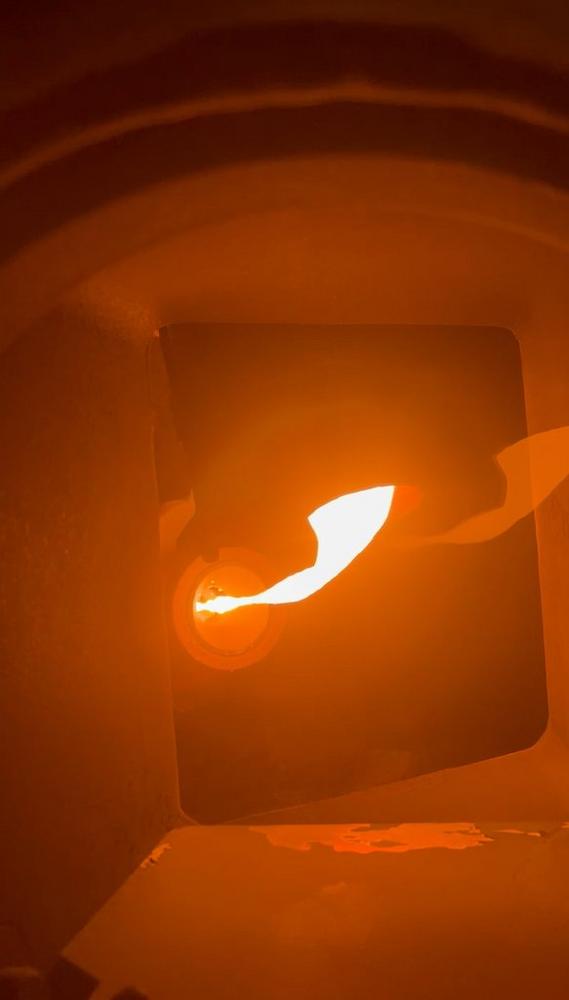
2 in 1: Mit Automatisierung und neuer Zweikammer-Vakuumgießanlage schafft die BLANK-Gruppe ein neues Setup im Vakuumguss
„Die bisherigen Einkammer-Vakuumgießanlagen und die damit verbundene Technik arbeiten zwar effizient, jedoch bringt der Ablauf der Prozessschritte Grenzen der Machbarkeit mit sich“, erklärt Bartosz Debek, der den Aufbau der Anlage betreute. Im bestehenden Prozess werden die über 1000°C heißen Schalen manuell aus dem Rundofen entnommen und in die Einkammer-Anlage gestellt. Im nächsten Schritt platzieren MitarbeiterInnen einen Fasertiegel mit der noch festen Legierung auf der Schale. Zwischen Schale und Tiegel sorgt ein geldstückgroßer „Penny“ dafür, dass sich die Schmelze im anschließenden Gussprozess unter Vakuum in der Kammer gleichmäßig verflüssigt, bevor das Schmelzen des „Pennys“ den Weg in die Schale freigibt. Das Problem des bisherigen Prozesses ist jedoch, dass sich die Schale in der Zeit bis zur Verflüssigung der Schmelze bereits unkontrolliert abkühlt, was bei anspruchsvollen Feingussteilen zu Fehlern führen kann.
Durch die Installation einer zusätzlichen Zweikammer-Anlage, konnte dieses Problem nun beseitigt werden. Die aus zwei Kammern bestehende Anlage schmilzt die Legierung in einer oberen Kammer über eine Induktionsspule, während sich die Schale ohne Hitzeverlust immer noch im Rundofen befindet. Erst wenn die Schmelze für den Abguss bereit ist, meldet die Anlage die Bereitschaft zur Schalenaufnahme. Mittels eines Industrieroboters wird die Schale innerhalb weniger Sekunden der unteren Kammer zugeführt und anschließend die Luft rasch abgepumpt, um nach dem Vakuumausgleich beide Kammerbereiche miteinander zu verbinden. Die Schale wird dann in die Gießposition gefahren und der Abguss erfolgt durch Drehen des Schmelztiegels. Mithilfe dieses neuen Prozesses konnte die Schalenabkühlzeit mehr als halbiert werden.
„Mit der neuen Anlage haben wir die Möglichkeit, schwer gießbare, dünnwandige Teile prozesssicher herzustellen, denn die Abkühlphase wird um zwei Minuten reduziert, was Gussfehlern vorbeugt. Feingussteile, auf die das Abkühlen der Schale geringeren Einfluss hat, werden weiterhin auf der bestehenden Einkammer-Anlage gegossen“, erklärt Peter Schäfer, der die Leitung des Gussbereichs verantwortet. „Wir wollten nun aber noch einen Schritt weitergehen und beide Anlagen, d. h. die Ein- und die Zweikammer-Gießanlage, miteinander verbinden, um den Prozess weiter zu automatisieren.“
„Diese Verbindung wurde durch einen Roboter bewerkstelligt, der gleichzeitig beide Anlagen bedient“, ergänzt Robert Rettich, Leitung des Betriebsmanagements und der Automatisierung bei BLANK. „Die Herausforderung lag hierbei besonders in der unterschiedlichen Taktung der Anlagen. Wir konnten die Maschinen und den Roboter aber so aufeinander abstimmen, dass das Schalenhandling und das Aufsetzen des Ingots bei der Einkammer-Anlage vom Roboter übernommen wird. Auch das Einfahren der Schale mit dem Ingot in die Anlage erfolgt automatisiert über den Roboter und eine Hubeinheit.“
Dieser Roboter der Einkammer-Anlage bedient zusätzlich auch die Befüllung der neuen Zweikammer-Anlage. „Dadurch konnte ein vollautomatisiertes Arbeiten der Maschinen erreicht werden.“ Die Abstimmung und das Bewegen der Schalen durch den Roboter ist nur durch ein ausgeklügeltes Greifsystem möglich, das betriebsintern durch mehrere Projektteams entwickelt wurde. So konnte erreicht werden, dass die Keramikformen mit verschiedenen Aufbauarten durch nur einen Robotergreifer gehandhabt werden, der die Prozessanforderungen sowohl der Einkammer- als auch der Zweikammer-Anlage erfüllt.
Das Konzept solle im nächsten Schritt auf weitere Anlagen im Unternehmen ausgeweitet werden, erklärt Peter Schäfer. „Durch die Vollautomatisierung und die Integration der neuen Zweikammer-Anlage erreichen wir eine schnellere Durchlaufzeit und qualitativ bessere Ergebnisse bei für den Gussprozess anspruchsvollen Teilen. Für die Nutzung der verbundenen Anlagen ist es notwendig, den Aufbau der Gießtrauben aufeinander abzustimmen. Diese Anpassung soll nun bei weiteren Modellen durchgeführt werden, sodass in Zukunft immer mehr Feingussteile über das neue Konzept in Serie produziert werden können. Das ist unsere nächste Herausforderung!“
Die BLANK-Unternehmensgruppe – Hidden Champion im Herzen Oberschwabens
BLANK ist ein Familienunternehmen mit über 800 Mitarbeitern, das seit mehr als 60 Jahren erfolgreich Feingusserzeugnisse fertigt und in die ganze Welt exportiert. Die BLANK-Gruppe, bestehend aus der FEINGUSS und FORMENBAU BLANK GmbH, der B² smart precision in Rumänien und der FEINGUSS BLANK USA Inc., ist eine der führenden Feingießereien mit Bearbeitungszentrum in Europa. Kein anderes metallformendes Verfahren kann ähnlich komplexe Formen zu vergleichbaren wirtschaftlichen Bedingungen herstellen wie der Feinguss nach dem Wachsausschmelzverfahren. Qualität auf höchstem Niveau, Genauigkeit bis ins kleinste Detail und eine nahezu unerschöpfliche Werkstoffvielfalt zeichnen Feinguss, made by BLANK, aus. Seit mehr als sechs Jahrzehnten sind wir deshalb Premium-Partner in der Automobilindustrie, im Maschinen- und Anlagenbau, in der Elektrotechnik, Feinmechanik und vielen weiteren Branchen.
Texmo Blank Germany GmbH
Industriestr. 18
88499 Riedlingen
Telefon: +49 (7371) 1820
http://www.TexmoBlank.com
Marketing & Unternehmenskommunikation
Telefon: +49 (7371) 182-200
Fax: +49 (7371) 18244-200
E-Mail: Manuela.Schmid@feinguss-blank.de

