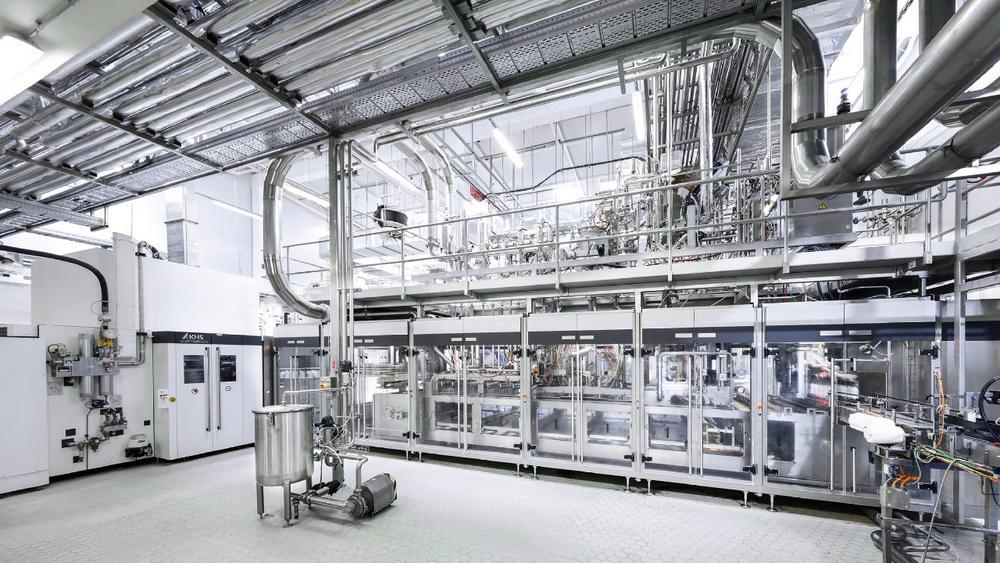
Phoenix aus der Asche
Ausgangspunkt der heutigen Imlek-Gruppe ist ein Bauerngut in Glogonjski Rit, einem Vorort von Belgrad. Hier gründet sich 1953 eine handwerkliche Molkerei. Von dort wird die Milch von rund 800 Kühen, täglich zwischen 3.000 und 5.000 Liter, zunächst noch in Blechkannen von Pferdegespannen und Traktoren auf die Märkte der Stadt gebracht. Schon vier Jahre später erhält der Betrieb seine erste Pasteurisierungs- und Abfüllanlage. Die Entwicklung nimmt nun Fahrt auf: 1963 produziert die Molkerei bereits mehr als 20 Millionen Liter jährlich. Auch die Siebzigerjahre stehen ganz im Zeichen von Wachstum: Immer mehr Molkereien schließen sich dem Verbund an. Seit 1991 wird das Unternehmen als Aktiengesellschaft unter dem Namen Imlek geführt. Heute füllt man hier mehr als eine Million Liter Milch pro Tag ab; der Jahresumsatz beträgt rund 300 Millionen Euro. Damit ist Imlek Marktführer – über die Grenzen Serbiens hinaus ebenso in den Nachbarländern Montenegro, Bosnien und Herzegowina sowie Mazedonien. Weitere Absatzmärkte sind zudem Kroatien, Albanien, Slowenien und vor allem Russland.
Als erstes Unternehmen im Balkanraum überhaupt investiert der Molkereiriese 2012 in einen Aseptikfüller, um für einen Teil seines Sortiments die keimfreie Abfüllung in PET-Flaschen zu ermöglichen. Übergeordnetes Ziel ist es, durch längere Haltbarkeit und ein geringeres Transportgewicht den Export sensibler Produkte zu erleichtern. Seinerzeit fällt die Entscheidung zugunsten des Linearfüllers Asbofill ABF 711 von KHS, da dieser die sterile Abfüllung dank seiner kleinen Aseptikzone ganz ohne Zwischensterilisation erlaubt. Verarbeitet werden stündlich bis zu 12.000 PET Flaschen mit einem Volumen zwischen 250 Milliliter und 2 Liter.
Fokus auf Flexibilität
Angesichts seines umfassenden Sortiments sind für Imlek die schnellen Formatwechsel wichtig, um in der Produktion möglichst flexibel agieren zu können. Schließlich müssen abwechselnd Extended Shelf Life (ESL)- und ultrahocherhitzte (UHT)-Milchprodukte abgefüllt werden können. Während sich schon die ESL-Milch durch eine um bis zu vier Wochen längere Haltbarkeit auszeichnet, bleiben UHT-Produkte ungeöffnet sogar drei bis sechs Monate haltbar. Insbesondere für die vielen verschiedenen kleineren Produktchargen bietet ein problemloser und kurzer Produktwechsel zum Beispiel gegenüber Kartonverpackungen mehr Flexibilität, Sicherheit sowie Schnelligkeit.
Überzeugen kann der Asbofill ABF 711 in puncto Flexibilität mit seinen vielfältigen Gestaltungsmöglichkeiten bei Flaschen und Verschlüssen, für deren Nutzung mechanisch nicht eingegriffen werden muss. Eine Besonderheit des KHS-Aseptikfüllers ist seine mit nur 1,5 Kubikmeter kleinstmögliche Hygienezone: In Kombination mit dem Raum-in-Raum-Konzept der Maschine senkt sie das Rekontaminationsrisiko auf nahezu Null. Die Beschränkung der Sterilisation auf die notwendigen Flächen – also außen nur des Neckbereichs – erlaubt einen sparsameren Umgang mit Sterilisationsmedien. Zudem benötigt der Füller aufgrund seiner kompakten Bauweise weniger Platz und lässt sich einfacher reinigen. Und dass er beispielsweise im Produktionszyklus kein zusätzliches Wasser benötigt, lässt ihn zugleich unter Nachhaltigkeitsaspekten gut aussehen.
So zufrieden sind die Serben mit der Technologie von KHS, dass sich das Unternehmen dem Dortmunder Maschinen- und Anlagenbauer gerne als Anschauungsobjekt für andere Interessenten zur Verfügung stellt. Immer wieder besuchen Kollegen den Imlek-Betrieb im Belgrader Vorort Padinska Skela, um sich die Maschine unter Alltagsbedingungen in der Produktion anzusehen. Schließlich hat sich die Molkerei selbst aufgrund guter Referenzen und Empfehlungen für eine KHS-Anlage entschieden – und diese Wahl zu keiner Zeit bereut.
Im September 2018 wütet in Padinska Skela ein Brand, der einen Großteil der Produktion zerstört und enormen Sachschaden anrichtet: Die Vorzeigetechnik des Aseptikfüllers wird ebenso wie viele andere Maschinen und Anlagen ein Raub der Flammen: „Ende 2018 und das komplette Jahr 2019 waren für uns eine sehr herausfordernde Zeit“, erinnert sich Darko Samardžija, Chief Supply Officer der Imlek-Gruppe. „Um die Versorgung des Marktes mit unseren Produkten zu gewährleisten, mussten wir die bezogenen Milchmengen zur Weiterverarbeitung an unsere anderen Werke in der Region sowie an Standorte außerhalb des Imlek-Systems umleiten. Dabei galt es sicherzustellen, dass alle Molkereien, an die wir die Rohmilch weitergegeben haben, unsere hohen Produktionsstandards erfüllen konnten. Schließlich sollten die Verbraucher Imlek-Produkte weiterhin in der gewohnten, besten Qualität bekommen.“
Erfolgreicher Wiederaufbau
Am Anfang des Wiederaufbaus steht die klare Entscheidung, die neue Fabrik zur modernsten in der Region zu machen – eine komplexe Aufgabe, wie Samardžija betont, die aber so schnell und erfolgreich abgeschlossen wird, dass die Folgen des Feuers, bei der Menschen glücklicherweise nicht zu Schaden kamen, bald vergessen sind. Heute steht der Standort für zukunftsweisendes Hightech in der Milchindustrie.
Dazu trägt maßgeblich die neue Blocklösung InnoPET BloFill ACF-L bei: Zum ersten Mal wurde eine KHS-Streckblasmaschine der neuesten Generation, eine InnoPET Blomax V, mit einem KHS-Aseptikfüller, dem Innofill PET ACF-L, verheiratet. Der Block punktet mit einer Vielzahl an Weiterentwicklungen, die ihn gegenüber dem Vorgängerfüller nicht nur noch leistungsfähiger macht, sondern vor allem nachhaltiger und wirtschaftlicher – etwa durch Energieeinsparungen von bis zu 40 Prozent. Um beide Maschinen zu verbinden, wurde eigens ein Transfermodul entwickelt, das den kontinuierlichen PET-Flaschenstrom aus der rotativen Streckblasmaschine in den batchweisen Verarbeitungsprozess des linearen Füllers überführt. Dafür werden aus dem Flaschenstrom je zehn aufeinanderfolgende Behälter als Gruppe so beschleunigt und von den nachfolgenden Einheiten getrennt, dass sie an der anschließenden Stoppposition problemlos durch Greifer gemeinsam entnommen und in die Trägerbleche des Füllers eingesetzt werden können. Auf einen Lufttransporteur kann durch die Kombination aus Streckblasmaschine und Füller komplett verzichtet werden – eine kompakte Lösung, die Platz spart, den Energieverbrauch reduziert und eine potenzielle Fehlerquelle eliminiert.
Mehr als nur Ersatz
Auch hinsichtlich der technischen Einzelheiten ist die Zeit seit der ersten Anschaffung im Jahr 2012 nicht stehen geblieben. Bei allem Unglück durch den Verlust der bewährten Lösung und dem erheblichen Organisationsaufwand während der Überbrückungszeit kann sich Imlek nun über eine neue Maschine freuen, die dank zahlreicher Weiterentwicklungen inzwischen weit über den Rahmen einer bloßen Ersatzinvestition hinausgeht. Experimente muss Imlek deswegen jedoch nicht eingehen: „Die Anforderungen waren im Prinzip dieselben wie bei der Erstinbetriebnahme“, erklärt Samardžija. „Im Vordergrund standen die Sicherung der Produktqualität und die Produktionsstabilität. Und wir haben bei der Wiederbeschaffung erneut Wert auf die besondere Flexibilität gelegt, um unsere unterschiedlichen Volumenformate auf der gleichen Maschine produzieren zu können.“ Durch die Verblockung kann ein vollumfänglicher Formatwechsel jetzt sogar innerhalb von nur zehn Minuten erfolgen – gegenüber Einzelmaschinen mit Lufttransporteur eine Zeitersparnis von bis zu 40 Prozent.
Im Unterschied zum alten Füller wurde beispielsweise die Füllmengengenauigkeit um rund 30 Prozent verbessert. Dafür kommen ebenso im Aseptikbereich magnetisch-induktive Durchflussmesser mit neuer Softwareauswertung und bewährten Algorithmen zum Einsatz. Sie sorgen für gleichmäßige Kopfraumvolumina und damit identische Füllstände in den Flaschen und minimieren das Risiko des Überschäumens.
Aseptik aus dem Baukasten
Neu am Aseptikfüller Innofill PET ACF-L ist zudem der modulare Aufbau. Er erlaubt es grundsätzlich, bereits bei der Anschaffung optionale Leermodule einzuplanen. Diese bieten Platz, damit der Füller zu einem späteren Zeitpunkt etwa um Folienverschließer oder Doseure für Fruchtstückchen erweitert werden kann, sofern es das Sortiment erfordert.
Teil der wiederhergestellten Linie bei Imlek ist schließlich die von 2012 stammende KHS-Verpackungsmaschine Innopack Kisters SP Basic, ein Schrumpfpacker, der bis zu 10.800 Gebinde pro Stunde mit Folienverpackungen versehen kann. Die Verpackungseinheit gehört zu den wenigen Ausstattungsstücken im Maschinenpark, die den Brand unbeschadet überstanden haben – nach einer Generalüberholung ist sie wieder voll funktionsfähig. „Auf der neuen Linie füllen wir – wie schon auf der alten – Frischmilch in verschiedenen Formaten sowie Schokoladenmilch ab“, sagt Samardžija. Die neuen Möglichkeiten, die sich aufgrund der State-of-the-Art-Technologie und der damit einhergehenden, gewachsenen Flexibilität bereits jetzt bieten, möchte man in naher Zukunft weiter ausschöpfen: „Wir können uns gut vorstellen, das Portfolio unseres Aseptikfüllers künftig zusätzlich auf Milchshakes und aromatisierte Milch auszuweiten“, sagt der Chief Supply Officer der Molkerei.
Zukunftsweisendes Sortiment
Rund 200 Produkte umfasst das Sortiment der Serben heute. Den größten Teil des Umsatzes erzielt man mit Sauermilchprodukten und frischer beziehungsweise Ultrahocherhitzter Milch. Finanziell nicht weniger wichtige, aber vom Volumen her deutlich kleinere Produktkategorien sind Milchstreichfette, Butter und übliche Mehrwertprodukte. Die Zukunftsorientierung, die das Unternehmen hinsichtlich seiner technischen Ausstattung der Produktion beweist, gilt genauso für sein Angebot: Neben Standard- und Bio-Milchprodukten umfasst dieses laktosefreie Produkte sowie die probiotische „Imlek Balans+“-Linie für alle, die den Themen Verdauung und Immunität besondere Aufmerksamkeit schenken. „In diesem Jahr haben wir „Imlek Protein“ auf den Markt gebracht, ein proteinreiches, laktose- und zuckerfreies Milchgetränk, das speziell für diejenigen gedacht ist, die auf ihre Ernährung achten und Sport treiben“, betont Samardžija. „Solche Produkte stehen schon seit einiger Zeit im Fokus der weltweiten Molkereiindustrie. Da ist es für uns nur logisch, Getränke dieser Kategorie unseren Verbrauchern im heimischen Markt anzubieten.“
Zur Modernität des serbischen Milchriesen gehört das strategische Engagement für mehr Nachhaltigkeit: „Im Rahmen unserer ökologischen Verantwortung statten wir unsere Marke Moja Kravica als erster heimischer Milchproduzent mit Verpackungen aus recycelbaren, biobasierten Kunststoffen aus“, sagt Samardžija nicht ohne Stolz. „Sogar der Verschluss selbst besteht aus Kunststoff pflanzlichen Ursprungs, und zwar aus Zuckerrohr.“ So viel steht fest: Seit seinen frühen Anfängen als lokaler Milchversorger auf einem Bauerngut am Stadtrand von Belgrad ist Imlek sehr weit fortgeschritten – und hat das Ende seiner beeindruckenden Entwicklung längst nicht erreicht.
Die KHS Gruppe ist einer der weltweit führenden Hersteller von Abfüll- und Verpackungsanlagen in den Bereichen Getränke und flüssige Lebensmittel. Zur Unternehmensgruppe zählen neben der Muttergesellschaft (KHS GmbH) diverse ausländische Tochtergesellschaften mit Produktionsstandorten in Ahmedabad (Indien), Waukesha (USA), Zinacantepec (Mexiko), São Paulo (Brasilien) und Suzhou (China). Hinzu kommen zahlreiche internationale Verkaufs- und Servicebüros. Am Stammsitz in Dortmund sowie in ihren weiteren Werken in Bad Kreuznach, Kleve, Worms und Hamburg stellt die KHS moderne Abfüll- und Verpackungsanlagen für den Hochleistungsbereich her. Die KHS Gruppe ist eine 100-prozentige Tochtergesellschaft der im SDAX notierten Salzgitter AG. 2020 realisierte die Gruppe mit 5.085 Mitarbeitern einen Umsatz von rund 1,130 Milliarden Euro.
KHS GmbH
Juchostr. 20
44143 Dortmund
Telefon: +49 (231) 569-0
Telefax: +49 (231) 569-1541
http://www.khs.com
Presse- und Öffentlichkeitsarbeit
Telefon: +49 (251) 625561-243
E-Mail: deppe@sputnik-agentur.de

