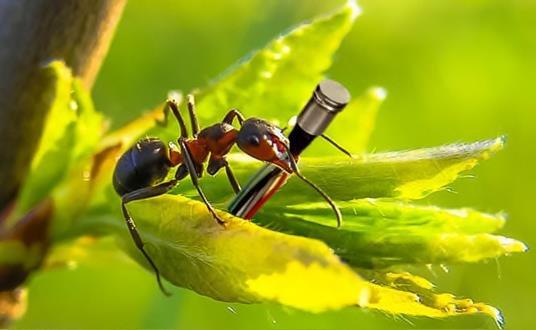
Sensoren für Test Rigs – MADE TO MEASURE
Heute übernehmen Sensoren diese Aufgabe. Sie werden bei Lebensdauer- und Belastungsprüfmethoden verwendet, um Schwachstellen von Prüflingen zu erkennen.
Betriebsfestigkeitsprüfungen (Durability):
Bei der Bestimmung der Lebensdauer eines Produkts spielt die Betriebsfestigkeit eine wesentliche Rolle. Diese Eigenschaft beschreibt, wie ein Prüfling Belastungen in einem definierten Zeitraum schadensfrei überstehen kann. Dazu werden oft mit Hilfe der "Wöhlerkurve" die Last- bzw. Spannungsamplituden gegen die Anzahl der Zyklen jeweils logarithmisch dargestellt. Die Wöhlerkurve ist in drei Bereiche eingeteilt:
Kurzeitfestigkeit oder statische Festigkeit (<10.000 Zyklen Schadensfreiheit), Zeitfestigkeit (>10.000 bis <1 Million Zyklen Schadensfreiheit) und Dauerfestigkeit (>1 Million Zyklen Schadensfreiheit)
Um Betriebsfestigkeitsprüfungen einigermaßen genau zu bestimmen braucht es viel Zeit (bei Fahrzeugen manchmal 1 Million km Fahrstrecke und 3 Jahre Dauerversuche). Um diese Prüfungen in realistischen Zeiträumen durchführen zu können, ist eine Verkürzung notwendig. Dies kann beispielsweise durch Änderungen an den Parametern der Experimente erreicht werden:
1) Höhere Belastungsamplituden
2) Höhere Geschwindigkeiten
3) Nur wesentliche Ereignisse
4) Vereinfachung (beispielsweise durch Verwendung von Sinus- statt realen Schwingungen)
Environmental Stress Screening (ESS)
ESS, beschreibt eine solche Belastungsprüfung und -auslese in einer beschleunigten Lebenszeit.
Hier werden Prüflinge in einer verhältnismäßig kurzen Zeit (Tage bis Monate) Belastungen unterworfen, die normalerweise während der gesamten Lebensdauer des Prüflings vorkommen.
Ziel ist es, die Ausfallhäufigkeit zu minimieren. Hierbei wird versucht den in der Skizze dargestellten "Badewannenverlauf" so "tief" wie möglich zu halten.
ESS wird in die zwei Bereiche HASS und HALT unterteilt, in der diese Ausfälle eintreten können:
HASS, eine Auslese-Püfung (ohne Beschädigung der Produkte), die in der Produktionsphase eingesetzt wird, um Fertigungsfehler zu erkennen (also am Anfang des Lebenszylkus).
Prüfungen während der normalen Nutzungsdauer des Produktes mit einer relativ konstanten und zufälligen Ausfallrate.
HALT, eine Konstruktions-Prüfung, die in der Entwicklungsphase eingesetzt wird, um Designfehler zu erkennen. Hier werden Prüflinge solange getestet, bis sie eine Beschädigung aufweisen (also eher am Ende des Lebenszyklusses).
Non-Destructive Testing (NDT)
Diese Art von zerstörungsfreier Werkstoffprüfung (ZfP), bezeichnet man generell als NDT. Hier wird die Qualität des Prüflings mit unterschiedlichen Verfahren untersucht, ohne ihn zu beschädigen. Die verwendeten Verfahren können je nach Art des Verschleißes sehr unterschiedlich sein. Dazu gehören – außer einer rein visuellen Prüfung – Messungen der Dehnung u.a. mit Dehnungsmessstreifen, Wirbelstrom-, magnetoresistiven- oder Lasersensoren, Feuchtemessungen, Dichtigkeitsprüfungen, Strukturmessungen durch Modalanalyse, Ultraschall- oder Körperschallsensoren, Oberflächenprüfungen durch Laserscanner, Mikroskope oder optische Farbeindringprüfungen und vieles mehr.
Condition Monitoring (Zustandsüberwachung)
Im Gegensatz zum ESS (HALT und HASS), die die Lebensdauer durch höhere Belastungen künstlich verkürzt, wird die Zustandsüberwachung während der Lebenszeit eines gefertigten Produkts durchgeführt.
Während des Betriebs eines Produktes können aufkommende Fehler schon früh erkannt werden, um dann entsprechende Maßnahmen vorzeitig ergreifen zu können, bevor ein größerer Schaden tatsächlich auftritt. Zurzeit erfolgt diese Erkennung meist noch durch geschultes Personal, das die Signale der Sensoren richtig interpretieren kann. In Zukunft wird diese Erkennung durch "intelligente Sensoren" in vorhandenen Bus-Systemen wie CAN kontinuierlich durchgeführt.
Modalanalyse /
Die Modalanalyse wird hauptsächlich verwendet, um die Schwingungsmuster (Moden) zu erkennen. Die Prüflinge werden dabei entweder durch einen Impulshammer oder einen Shaker angeregt und mit Sensoren an verschiedenen Stellen gemessen, um zu schauen, wie stark der jeweilige Bereich schwingt bzw. ausgelenkt wird.
Auch die Risserkennung nicht sichtbare Risse können durch Modalanalyse oder Ultraschall-Messungen erkannt werden. Bei der Modalanalyse werden die Spektren des Erzeuger-Impulses (Kraftsensor im Hammer) mit dem Spektrum des Antwortsignals verglichen.
Messungen an heißen Teilen
Für die Prüfung an heißen Teilen (wie beim Auspuff oder bei Turbinen) ist es zudem notwendig Sensoren einzusetzen, die hohe Temperaturen bis über 600 °C aushalten, ohne selbst beschädigt zu werden.
Grundlage für alle diese Maßnahmen sind geeignete Sensoren.
Wie zu erkennen ist, gibt es nicht nur eine Vielzahl von Methoden zur Optimierung eines Produkts, sondern eine ganze Fülle an Sensoren und Herstellern, die sich auf das jeweilige Sensorsystem bzw. eine bestimmte Prüfmethode spezialisiert haben. Was dem Anwender leider häufig fehlt, ist ein Überblick über die verschiedenen Methoden und Sensoren.
Verschiedene Sensoren für die gleiche Messgröße/Unabhängigkeit vom Sensorprinzip
Einen Überblick über die Sensoren für die unterschiedlichsten physikalischen Größen zu haben insbesondere die Unterschiede, Vor- und Nachteile der jeweiligen Sensoren und Sensorprinzipien und Methoden is essenziell um eine optimale Lösung für die Anwendung auszusuchen.
Für Beschleunigungsmessungen, bSensoren mit verschiedenen zu Grunde liegenen physikalische Messprinziepien können die selbe Messgröße messen. Je nach Anwendung kann dann der Sensor, der auf dem einen oder anderen Messprinzip beruht, seine jeweilige Stärke ausspielen. Beispielsweise, werden für Schock-Tests meistens piezoresistive Beschleunigungssensoren verwendet, für Schwingungsbelastungen piezoelektrische. Für langsame Bewegungen kapazitive Beschleunigungssensoren.
Verschiedene Sensoren für den gleichen Prüfstand
Für die Erkennung von Motorverschleiß könnte man eine Temperaturmessung verwenden, denn ein Temperaturanstieg ist meistens schon ein Zeichen von Verschleiß. Allerdings ist der Verschleiß dann meistens schon so weit fortgeschritten, dass es für einen Eingriff zu spät sein könnte. Besser wäre es, schon an einer Veränderung am Ton oder Geräuschpegel des Motors einen Verschleiß zu erkennen. Hier kann also eine Vibrationsmessung eingestetzt werden. Wo es früher hierzu einen geübten Techniker gebraucht hat, übernehmen dies jetzt Beschleunigungssensoren oder Mikrofone. Noch früher ist dies möglich, wenn man den tatsächlichen Metall-Abrieb im Getriebe frühzeitig erkennt und den Nutzer alarmiert, denn oft tritt dieser auf, bevor es zu einer wahrnehmbaren bzw. messbaren Änderung im gemessenen Frequenzspektrum des Motors kommt
Maßgeschneiderte Sensoren
Oft ist es nicht möglich Standardsensoren in vorhandenen Umgebungen zu montieren, ohne kostspielige Änderungen am System vorzunehmen. Hier ist man auf flexible Partner angewiesen, die – auch für geringe Stückzahlen – vorhandene Sensoren an die Anwendungen anpassen, nach dem Motto "MADE TO MEASURE"!
Intelligente Sensoren / Internet Of Things (IoT)
Die Zukunft aber liegt in intelligenten Sensoren und lernfähigen Erkennungs- und Wartungssystemen.
Hier werden Sensoren vernetzt und senden nicht nur ihre Signale über ein BUS-System, wie beispielsweise CAN, an ein Auslese- und Analysegerät, sondern analysieren die Daten selbstständig mit integrierten Mikroprozessoren, wie dem erweiterten CAN-BUS-System CAN-MD®; wobei MD für Maschinen Diagnose steht (maschine diagnostics).
Durch CAN-MD® – Inlineadapter können bereits auf dem Markt befindliche Analogsensoren mit dieser Intelligenz aufgerüstet werden, um mit im CAN-MD® Zustandsüberwachungs Netzwerk eingebunden zu werden.
Zustandsindikatoren, CI (Condition Indicators)
In jedem CAN-MD® – kompatiblen Sensor können bis zu 126 Zustandsindikatoren programmiert werden. Mit bis zu 32 Sensoren pro CAN-BUS-Eingang eines kompatiblen Datenerfassungsgeräts kann dauerhaft sehr differenziert überwacht und damit auch schnell reagiert werden. Auch Rohdaten können über das BUS-System übertragen werden. Zudem können Sensoren im CAN-MD®-System-BUS auch miteinander kommunizieren.
Über das Internet können diese Maschinenzustandsdaten der Prüflinge (of Things) über ein CAN-MD®-Gateway von der "Cloud" für eine Fernsteuerung und -verwaltung abgerufen werden.
Die Zukunft: künstliche Intelligenz
Allerdings muss auch hier eine technisch versierte Person die optimalen Parameter für die Zustandsindikatoren kennen und eingeben. In Zukunft wird ein KI-System in einem beschleunigten Lebenszyklus des Objektes (HALT) die Parameter durch Lernen von Fehlern selber erkennen und sich selbst ständig optimieren.
Nachhaltigkeit
Den richtigen Sensor und das richtige Verfahren auszuwählen kann die Lebensdauer von Produkten erheblich verlängern und somit nicht nur den Benutzern eine Menge Ärger und dem Her-steller eine Menge Kosten ersparen, sondern auch einen wertvollen Beitrag zur Nachhaltigkeit und zum Schutz unserer Umwelt leisten.
disynet GmbH
Breyeller Str. 2a
41379 Brüggen-Bracht
Telefon: +49 (2157) 8799-0
Telefax: +49 (2157) 8799-22
http://www.sensoren.de
Telefon: +49 (2157) 8799-28
Fax: +49 (2157) 8799-22
E-Mail: peter.ettwig@disynet.de

