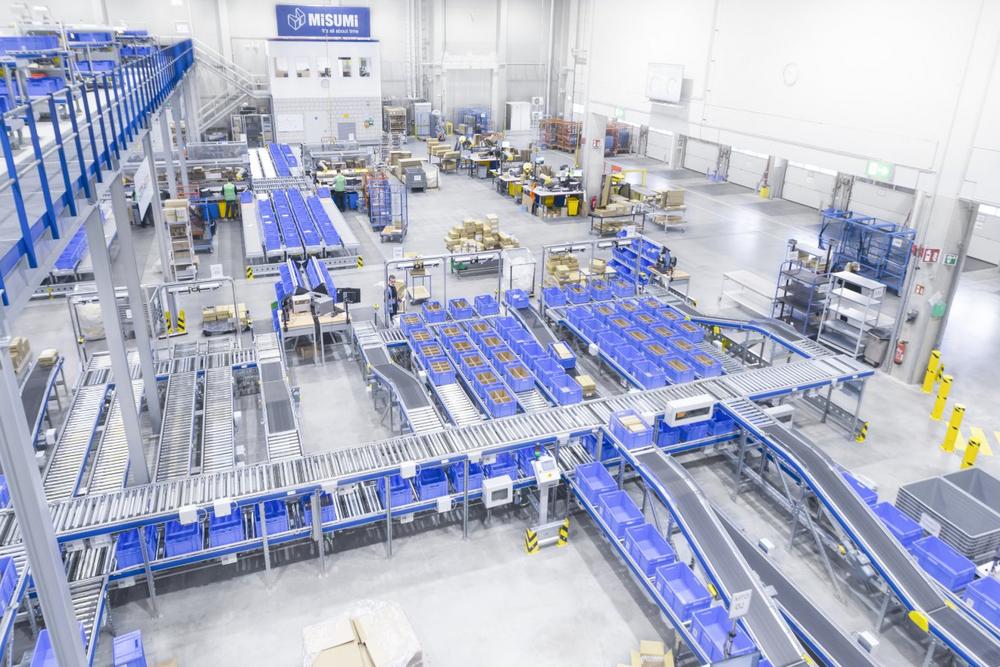
SSI Schaefer Delivers High-Performance Logistics Center for Mechanical Engineering Components
"It’s all about time" is the motto of Misumi and underlines the vital role that time plays in the business activities of the company, which was founded in Tokyo in 1963. Misumi is a global supplier of customized mechanical engineering components and standard parts for industry, particularly for special-purpose machinery. Customers can choose from a portfolio of 17 million parts from various manufacturers or configure their desired part from more than 100,000 basic components, even for a batch size of 1. These so-called make-to-order (MTO) components constitute more than 50% of the business operations of Misumi. The company has adopted the cross-docking principle for the turnover of its stock: as soon as they are received, products are consolidated against the existing goods in stock and dispatched to customers in Germany and across Europe on the same day.
Maximizing Warehouse Capacity and Optimizing Space Utilization for Short Delivery Times
Speed, in other words, a short delivery time, is one of Misumi’s core strengths. Innovation cycles are additionally considerably shorter than before, particularly in mechanical engineering, leaving the market players with less time for product development and needing their components sooner. Misumi normally supplies its customers with special components, made in Asia, within a week. "The higher our stock levels, the shorter the average delivery time," explains Jörg Gonnermann, General Manager Logistics Service Platform at Misumi Europa GmbH. "As a first step it was therefore important to significantly increase warehouse capacity." This brought Misumi and SSI Schaefer together in 2018 when, as part of a material handling project, SSI Schaefer installed a 4-tier R 3000 modular shelving system to increase warehouse capacity at Misumi by a factor of 6. The modular shelving system is 45 m x 48 m in size and makes optimum use of the 10-m high building, providing space for up to 250,000 items. The compact shuttle warehouse, added later, has meanwhile helped increase storage capacity to 450,000 items. Misumi has now considerably boosted its stock levels and can supply standard parts to its customers much faster than before, as they can be added to the MTO items directly from the warehouse.
Custom Automation
The B2B activities of Misumi are dominated by e-commerce: around 75% of the orders are currently processed through its own e-commerce platform. Due to the strong growth of e-commerce, powered by digitalization in mechanical engineering (Industry 4.0), the number of customer orders handled by Misumi has significantly increased over the years. To be able to handle this increasing number of orders even more efficiently, Misumi opted for a highly automated solution that would offer increased warehouse capacity while providing ample scope for future growth. The automation concept of SSI Schaefer was soon on the table and convinced Misumi on the spot. "The concept went into our requirements in great detail and looked at how to achieve the highest levels of process efficiency and make best use of the available space. It also considered ergonomic aspects in terms of work stations and ensured a high degree of flexibility in system utilization," recalls Gonnermann. "Our demanding requirements were totally satisfied and we were even given some useful extra features." SSI Schaefer realized the entire material handling solution from its own resources: modular shelving system, shuttle system, conveying system, returnable containers through to work stations, logistics software, and finally Customer Service & Support.
High-Performance Logistics for Increased Efficiency
Despite the limited space available, the material handling solution was able to interconnect the different work stations and warehouse areas perfectly. Misumi is now the proud owner of an open-ended and powerful material flow system that has sufficient buffer capacity to handle the order levels as they fluctuate during the day. At the heart of the system is the shuttle warehouse, which makes fully automated warehousing possible and, thanks to its compact design, optimum use of the available space. SSI Schaefer installed the shuttle warehouse, which was constructed using 580 metric tons of steel and has space for 66,000 containers, at the end of 2019. At present, it holds 200,000 items across 10 aisles and 22 levels and covers an area of 39 m x 46 m. The single-level SSI Cuby shuttle, which can handle both containers and cartons, is used inside the shuttle warehouse. Misumi uses around 56,000 LTF 6280 returnable containers from the SSI Schaefer portfolio. Of these, approximately 46,000 are used as stock containers in the shuttle warehouse, while the rest are utilized for order consolidation. Two lifts, installed at the front in each aisle, ensure a high degree of technical performance of the system and a high level of reliability in the shuttle warehouse. The conveying system connects the two warehouse areas with the various work stations – at ground level as well as on the steel platform – and thus eliminates almost all walking. The system also includes six conveyor loops – three loops on top of each other, per level – on which the storage, retrieval, and empty containers are transported and distributed between the storage, picking, and dispatch/packing locations. The shuttle warehouse and conveying system are controlled by the WAMAS® logistics software from SSI Schaefer.
The 825 m² steel platform, on which the picking area is situated, lies in front of the shuttle warehouse. The platform is where the five ergonomic Advanced Pick Stations two-level, used for order picking, are located; these stations are linked to the shuttle warehouse. Up to six orders can be handled by each work station simultaneously, at rates of up to 1,000 picks per hour. If required, two additional work stations can be added to the picking stations. Employees are guided by a light signal that keeps them focused on the picking operation. This approach has resulted in a dramatic increase in picking speed and quality at Misumi, while reducing the error rate to almost zero. The goods-in and dispatch areas are located underneath the steel platform on the first floor. "Overall, lead times have improved and we are seeing high increases in productivity," observes Gonnermann. "In the ideal scenario, an order will pass through our logistics center in less than 60 minutes." A further advantage: system operation is now much easier to predict and it is now possible to produce a highly detailed plan for each day’s volumes.
The system went live in April 2020. The introduction of automation came at the right time, even though conditions at the start of the COVID-19 pandemic in 2020 made things more difficult. The new material handling solution provides much more flexibility in personnel planning, with no more overlapping shifts. "The work steps are ideally structured, so our employees were quickly up to speed with the new workflows," is how Gonnermann describes the introductory phase.
Transparent and Efficient Material Flows
The customized components arrive by air freight in the morning at Frankfurt Airport and are delivered to the Misumi logistics center by truck. At the eight goods-in work stations, the pallets are broken down using a cross-docking procedure, distributed in containers, and temporarily stored in the shuttle warehouse. The pallets have several thousand individual positions for a large number of different customers. The goods are split by customer-specific MTO goods and goods for storage at the first four work stations. The MTO items are packed in containers and transported into the shuttle warehouse until the order is completed. The goods for storage are forwarded to one of the four remaining work stations, where the items are sorted for storage either in the modular shelving system or in the shuttle warehouse. Once this decision has been identified, the goods pass along the conveying system to the corresponding warehouse area. Picking of the goods for storage is either done manually in the 4-tier modular shelving system or in accordance with the goods-to-person principle at the picking stations linked to the shuttle warehouse. As soon as picking of all the order items is complete, the warehouse management system launches the retrieval process. The conveying system transports the containers to one of the dispatch work stations, where the items are taken out of the containers and packed in a carton, prepared for shipping, and handed over to the express delivery company.
Permanent System Availability
Although the system has been commissioned and the project closed-out, the collaboration between Misumi and SSI Schaefer is by no means over. The two companies continue to work closely together within the scope of the service contract. SSI Schaefer took over all the servicing and maintenance of the system for the first two years after handover to ensure continuous operation of the system. Preventive maintenance is performed by specially trained service technicians using SSI CMMS, the computerized maintenance management system. SSI CMMS is an electronic service portal that controls and monitors maintenance and repair activities efficiently. All the relevant information can be stored, consolidated, and visualized to provide fact-based insights into the status of the system. Any faults and wear can be detected and rectified in a timely manner. "Ever since we first met SSI Schaefer, we’ve found them to be a totally reliable and professional partner that has full control over the processes, even after commissioning," summarizes Gonnermann.
The SSI Schaefer Group is the world’s leading provider of modular warehousing and logistics solutions. With headquarters located in Neunkirchen (Germany), SSI Schaefer employs approximately 10,500 associates globally, along with seven domestic and international production sites, and approximately 70 worldwide operating subsidiaries. Across six continents, SSI Schaefer develops and implements innovative industry-specific answers to its customers‘ unique challenges. As a result, it plays a key role in shaping the future of materials handling.
SSI Schaefer designs, develops and manufactures systems for warehouses and industrial plants. Its portfolio includes manual and automated solutions for warehousing, conveying, picking and sorting, plus technologies for waste management and recycling. In addition, SSI Schaefer is now a leading provider of modular, regularly updated software for in-house material flows. Its IT team, with a headcount in excess of 1,100, develops high-performance applications, and provides customers with in-depth advice on the intelligent combination of software with intralogistics equipment. The SSI Schaefer IT offering, including its own WAMAS® and SAP products, delivers seamless support for all warehouse and material flow management processes. Solutions from SSI Schaefer improve the productivity and efficiency of customer organizations – not least through the highly precise monitoring, visualization, and analysis of operational metrics for proactive intralogistics management.
SSI Schaefer offers highly sophisticated, turnkey systems. As an international player, it can deliver one-stop solutions to all four corners of the earth. Its comprehensive portfolio encompasses design, planning, consulting, and customer-specific aftersales services and maintenance.
SSI SCHÄFER
Fritz-Schäfer-Strasse 20
57290 Neunkirchen / Siegerland
Telefon: +49 (2735) 70-1
Telefax: +49 (2735) 70-396
http://www.ssi-schaefer.de
Junior Project Manager CR & PR | Global Marketing
Telefon: +49 (2735) 70-9683
Fax: +49 (2735) 70-382
E-Mail: Annika.Nolte@ssi-schaefer.com
Marketing & Kommunikation
Telefon: +49 (2735) 70-252
Fax: +49 (2735) 70-382
E-Mail: melanie.kaempf@ssi-schaefer.de

