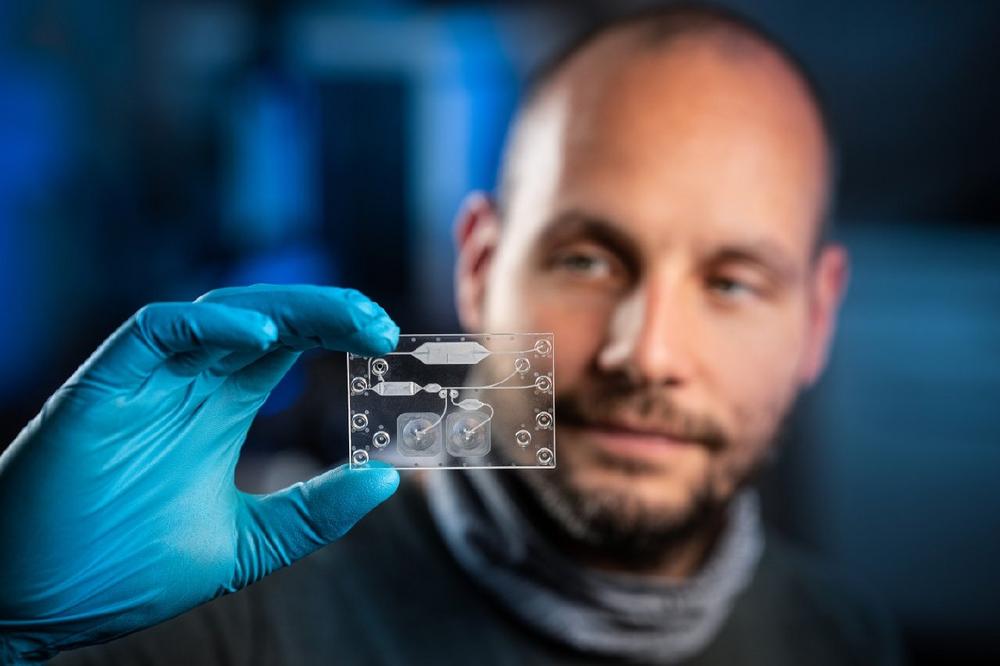
Lab-on-chip systems: From prototype to series production in no time
Lab-on-chip systems are only a few centimeters small, but combine diverse functionalities on this small area, as only well-equipped laboratories allowed in the past. “Especially in personalized medicine they will play an important role in the future,” expects Dr. Frank Sonntag, head of department Micro- and Biosystems Engineering at Fraunhofer IWS. Minimal liquid quantities from patient samples can be analyzed entirely in an automated fashion. The simple handling will also enable near-patient laboratory diagnostics in the future. It is true that various lab-on-chip systems have been developed all over the world in recent years. However, only a small number of these made it to the market. “The hurdle is scaling up lab-scale developed tests for mass production,” he explains. Fraunhofer IWS developed a solution to these industrialization problems.
Planning once for several simultaneous processes
The project “Scalable Microfabrication of Polymeric In Vitro Diagnostic Systems” (SIMPLE-IVD) focuses on the in vitro diagnostic (IVD) cartridges for rapid tests. “Prototypical production processes are currently still not available for the path from small series to large quantities,” explains Florian Schmieder, SIMPLE-IVD project manager. Production processes in the lab include additive manufacturing or multilayer lamination, meaning the buildup in layers of polymer films, which would be implemented for series production in injection molding or roll-to-roll processes. “Until now, manufacturers had to start all over again in order to scale up to another process,” explains the scientist from the Micro and Biosystems Engineering Group at Fraunhofer IWS.
His team has now found a solution to this problem by developing and testing special design rules. With their help, as early as the design phase for IVD cartridges, producers can meet requirements for a wide variety of manufacturing processes, both for prototype development and for small as well as large series. Fraunhofer IWS scientists have already created such design rules for several classical manufacturing technologies. In addition to injection molding and vacuum casting, these include multilayer lamination, deep drawing and several additive processes. “In the future, we will constantly expand the range,” Schmieder looks ahead. In this context, solutions can also be developed with customers as quickly as possible that precisely fit their requirements. A reverse transformation from large to small series would also be possible in practice. The design sets will not only attract manufacturers of IVD cartridges, Schmieder adds: “There are currently numerous biotechnology start-ups that need precisely such options.”
Globally unique solution saves time and costs
The major advantage offered by this innovative method is that prototypes and small series can be turned into industrial solutions more quickly than before. Lab-on-chip systems thus reach market maturity faster and are available to users more quickly. “With our globally unique solution, we can almost halve the time previously required in this respect,” the Fraunhofer IWS researcher clarifies. As a result, costs in the manufacturing process will be reduced.
All companies involved in the project are testing and validating the design rules. “The translation technologies developed in the SIMPLE-IVD joint project help us, as manufacturers of innovative blood separation technologies, to develop new products quickly and in a cost-efficient manner from prototype to finished series product,” Dr. Wilhelm Gerdes, CSO at Cell.Copedia GmbH from Leipzig, also emphasizes the results to date. Other participants include Microfluidic ChipShop mbH from Jena and the two Dresden-based companies GeSIM Gesellschaft für Silizium-Mikrosysteme as well as Michael Sander Kunststofftechnik GmbH. SIMPLE-IVD is financed by funds from the German Federal Ministry of Education and Research.
By the end of the project in 2022, the results are to be translated into a universal data set. “We want to use different methods to produce functionally equivalent IVD cartridges,” says Florian Schmieder, explaining the background. The goal is to achieve the same high quality of end products using different methods and allowing identical results in application. Customized IVD tests enable individual and permanent screening of diseases in healthcare. “Our novel method makes it possible to open up the market for early detection of diseases that currently cannot be covered by statutory screening services due to cost reasons,” summarizes Frank Sonntag. It could also be used for diagnostic home care applications for domestic care or in nursing facilities.
This research and development project is funded by the German Federal Ministry of Education and Research (BMBF) within the “Innvoations for Tomorrow’s Production, Services, and Work” program (FKZ 02P18C100) and implemented by the Project Management Agency Karlsruhe (PTKA). The author is responsible for the content of this publication.
The Fraunhofer Institute for Material and Beam Technology IWS Dresden develops complex system solutions in materials and laser technology. We define ourselves as idea drivers developing customized solutions based on laser applications, functionalized surfaces as well as material and process innovations – from easy-to-integrate custom solutions to cost-efficient solutions for small and medium-sized enterprises to industry-ready one-stop solutions. Our research focuses on aerospace, energy and environmental technology, automotive, medical and mechanical engineering, toolmaking, electrical engineering and microelectronics, and photonics and optics sectors. In our five future and innovation fields of battery technology, hydrogen technology, surface functionalization, photonic production systems and additive manufacturing, we are already creating the basis today for the technological answers of tomorrow.
Fraunhofer-Institut für Werkstoff- und Strahltechnik IWS
Winterbergstraße 28
01277 Dresden
Telefon: +49 (351) 83391-0
Telefax: +49 (351) 83391-3300
http://www.iws.fraunhofer.de
Head of Corporate Communications
Telefon: +49 (351) 83391-3614
E-Mail: markus.forytta@iws.fraunhofer.de
Project Manager SIMPLE-IVD
Telefon: +49 (351) 83391-3520
E-Mail: florian.schmieder@iws.fraunhofer.de

