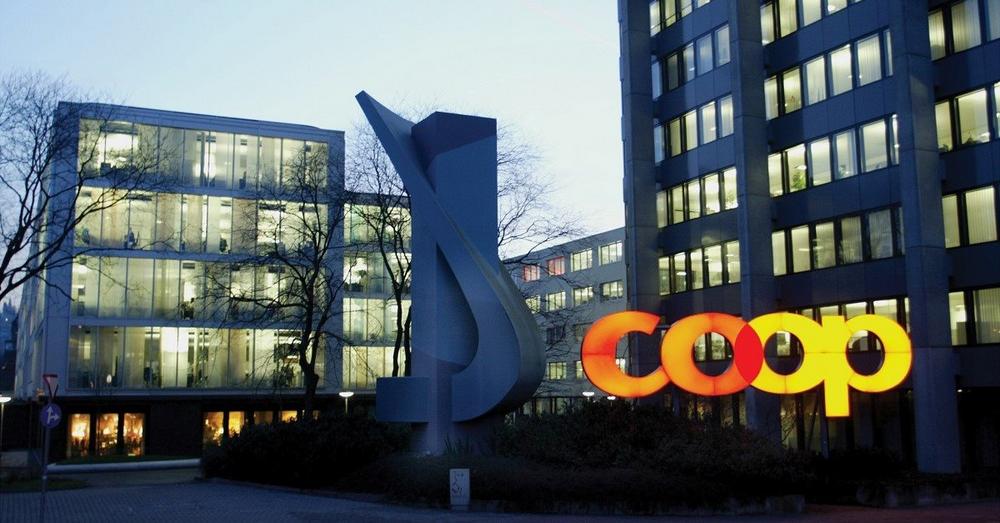
Swiss retail company Coop: A Highly Efficient E-Commerce Warehouse Created in 14 Days
With around 90,000 employees, Coop is a major player in Switzerland. Besides the well-known supermarket chain, the Coop Group also includes various sales formats as well as wholesale and production companies. In 2020, this successful company achieved total revenues of 30.17 billion Swiss francs, and its online retailing business has seen powerful growth.
Focus on increasing capacity
While traditionally rooted in brick and mortar retail, Coop recorded a sharp rise in orders via the online shop Coop.ch during the lockdown of spring 2020. Faced with this unforeseeable spike in demand, the logistics structures reached the limits of their capacity. A quick solution therefore had to be found to create more storage space and offer customers additional delivery time slots.
Twin-pillar strategy for online business implemented in a rush
Coop initiated a twin-pillar strategy. First, an assortment of products was defined that would keep an average Swiss household supplied with basic goods. These products would then be handled via a 6,000 square meter warehouse leased at short notice, equipped with a new IT and logistics infrastructure, and connected to the Coop network, all within the space of 14 days. WAMAS was implemented in partnership with SSI Schaefer. At the same time, more than 100 pickers were trained to operate the logistics software, which has been used since commissioning to manage the rapid processing of online orders efficiently via 300 pick-up locations with multiple placement. The extremely user-friendly WAMAS user interface also ensured that staff could learn the system quickly.
Software standard and team strength as project accelerators
Coop has relied on the software expertise of SSI Schaefer for its warehouse management since 2001. The retail and wholesale company uses a uniform warehouse management (WMS) solution at all its locations to optimize performance and harmonize logistics processes. Another advantage of WAMAS is the increased transparency of all stocks and transactions with complete traceability. The integrated software standard, tailor-made for Coop, as well as trust in the partner’s know-how built up over the course of a 20-year collaboration, proved decisive in overcoming even unplanned events: "Setting up a warehouse from scratch and putting it into operation in just 14 days is only possible with dependable partners, and a team where everyone knows what to do, and if you can fully rely on each other," says Martin Nyfeler, Head of IT Pro. WW Logistics/SCM, Coop, underlining the successful collaboration with SSI Schaefer.
Agile enough to cope with the unexpected and reliably prepared
Flexibility, responsiveness, and the ability to put ideas into practice are always elementary success factors, but in challenging times they are downright essential. While seasonal fluctuations in demand can be cushioned by precise advance planning over several months, a pandemic event calls for ad-hoc measures to maintain supply chains. These can only be implemented effectively with the support of a long-standing software partner like SSI Schaefer, who understands both the industry and the customer’s specific needs, and is fully familiar with the processes. At the same time, the new e-commerce warehouse in Altishofen which has been implemented within a very short time for Coop – a retail company that has also become a successful online retailer – is tangible proof that the material handling specialist has again lived up to its promise to deliver flexibility and speed plus security and stability in every situation.
The SSI Schaefer Group is the world’s leading provider of modular warehousing and logistics solutions. With headquarters located in Neunkirchen (Germany), SSI Schaefer employs approximately 10,500 associates globally, along with seven domestic and international production sites, and approximately 70 worldwide operating subsidiaries. Across six continents, SSI Schaefer develops and implements innovative industry-specific answers to its customers‘ unique challenges. As a result, it plays a key role in shaping the future of materials handling.
SSI Schaefer designs, develops and manufactures systems for warehouses and industrial plants. Its portfolio includes manual and automated solutions for warehousing, conveying, picking and sorting, plus technologies for waste management and recycling. In addition, SSI Schaefer is now a leading provider of modular, regularly updated software for in-house material flows. Its software team, with a headcount in excess of 1,100, develops high-performance applications, and provides customers with in-depth advice on the intelligent combination of software with intralogistics equipment. The SSI Schaefer IT offering, including its own WAMAS® and SAP products, delivers seamless support for all warehouse and material flow management processes. Solutions from SSI Schaefer improve the productivity and efficiency of customer organizations – not least through the highly precise monitoring, visualization, and analysis of operational metrics for proactive intralogistics management.
SSI Schaefer offers highly sophisticated, turnkey systems. As an international player, it can deliver one-stop solutions to all four corners of the earth. Its comprehensive portfolio encompasses design, planning, consulting, and customer-specific aftersales services and maintenance.
SSI SCHÄFER
Fritz-Schäfer-Strasse 20
57290 Neunkirchen / Siegerland
Telefon: +49 (2735) 70-1
Telefax: +49 (2735) 70-396
http://www.ssi-schaefer.de
Junior Project Manager CR & PR | Global Marketing
Telefon: +49 (2735) 70-9683
Fax: +49 (2735) 70-382
E-Mail: Annika.Nolte@ssi-schaefer.com
Marketing & Kommunikation
Telefon: +49 (2735) 70-252
Fax: +49 (2735) 70-382
E-Mail: melanie.kaempf@ssi-schaefer.de