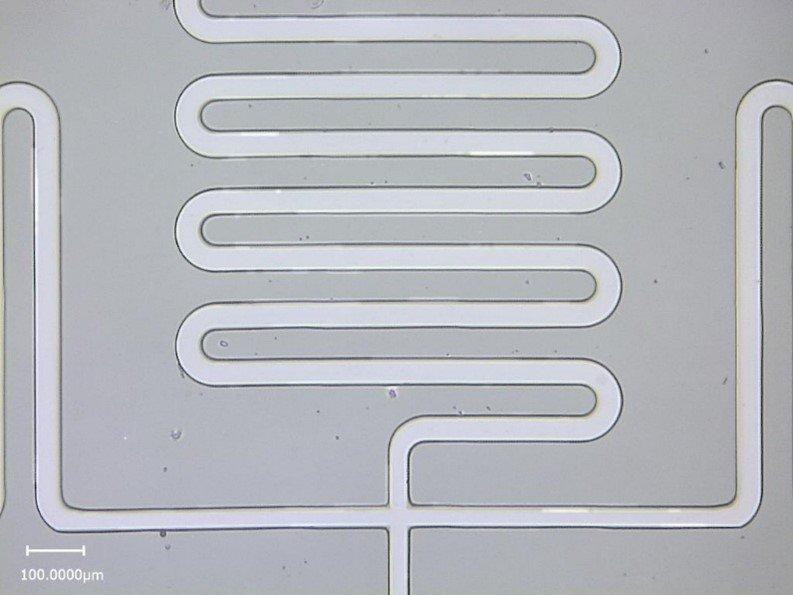
Use of plasma for bonding, activation and etching
All measurements took place under normal laboratory conditions (p = 1.3 bar; T = 25 °C; r.l. = %) and the plasma treatment under a fume bonnet.
"The piezobrush® PZ3 has far exceeded our expectations. It can be used in a wide range of applications, such as plasma bonding of microfluidics made of PDMS, produced via soft lithography processes, or for etching thin-film material (e.g. parylene) and stands out above all due to its performance and easy handling compared to other plasma devices. We are thrilled and can recommend the device to everyone."
– Inola Kopic, Chair of Neuroelectronics at TUM
Bonding PDMS to glass
A standard process for the production of microfluidics is soft lithography with silicone (PDMS). Here, the channels are moulded from a so-called master mould and then closed by bonding to another surface. Usually, the PDMS is bonded to glass via plasma. In this process, OH groups are induced on the PDMS and glass surfaces and then brought into contact with each other. Stable Si-O-Si bonds are formed with the elimination of water molecules, which ideally prevents the PDMS from being removed.
The aim of this investigation was therefore to test whether plasma treatment with the piezobrush® PZ3 handheld device changes the surface sufficiently for the bond between glass and PDMS to form.
For the investigation, a microfluidic structure was softlithographically imprinted with 1.5 mm thick PDMS (see figure 1). The structure was then bonded to a 1 mm thick glass plate. Both surfaces (approx. 2 cm2) were treated for 1 min at 100% power. The PDMS was placed on the glass and lightly pressed on. Subsequently, the microfluidic was placed on the glass and pressed on. To check the adhesion, an attempt was also made to remove the PDMS from the glass pane with tweezers. The bond between polymer and glass is so stable that only small pieces can be broken out, but the PDMS layer cannot be removed from glass.
Surface activation of polyimide films
In addition to the bonding of microfluidic structures made of PDMS on glass, the hydrophilicity of PI films before and after plasma treatment was also investigated. In microfabrication, surfaces are often modified to make them more hydrophilic. Hydrophilic surfaces are advantageous, for example, in centrifugal coating or in subsequent ink printing processes, as the liquid can be better distributed on the surface.
One indicator for checking whether a surface is hydrophilic or hydrophobic (water-repellent) is the contact angle (CA). For this, a drop of a liquid (for example water) is placed on the surface to be tested and the angle formed between the drop and the substrate is measured. If the angle is > 90°, the surface is said to be hydrophobic. If, on the other hand, the angle is < 90°, the surface is hydrophilic. This method was used by the TUM team to characterize the substrate. Two cleaned 75 µm thick PI films were used as substrates. One of these foils was then additionally treated with plasma (1 min at 100 % power). Using a contact angle measuring device from Dataphysics, a drop of the test liquid, in this case ultrapure water, was applied to the surfaces and the contact angle on both foils was then measured. The result can be seen in Figure 2 and Figure 3.
It is clearly visible that the contact angle (CA) on both surfaces is < 90°. This in turn means that both substrate surfaces are hydrophilic. However, it is astonishing that the contact angle on the treated substrate decreases significantly (CA = 20.7 °) already after a one-minute application with piezobrush® PZ3 and thus the surface becomes more hydrophilic.
Etching Parylene-C
Parylene has found wide acceptance as a coating material in the microelectronics and medical industries. In this context, removal in delimited areas is of particular interest. One method for this is etching with oxygen plasma. To check whether the piezobrush® PZ3 is suitable for etching parylene-C, a series of tests was carried out. For this purpose, a 1 mm thick glass substrate coated with 5 µm parylene-C was masked with Kapton tape and treated for a duration of 20 min (corresponds to 4×5 min) at 100 % power with the handheld plasma device. Subsequently, the difference in thickness of the parylene layer between the etched area and the area protected by the tape was measured using a profilometer (Keyence VK250).
Figure 4 shows the result after plasma treatment. The lower picture shows the difference in height between the glass substrate and the parylene layer. The plasma device was able to etch away the entire 5 µm thick layer within 20 min. Thus, the device is even suitable for etching parylene layers in the µm range.
Conclusion
In conclusion, it can be said that the plasma handheld device can be used in a wide variety of areas, be it microfluidics, electronics or microfabrication, and that despite its compact size, it is possible to achieve excellent results compared to conventional plasma systems.
relyon plasma GmbH
Osterhofener Str.6
93055 Regensburg
Telefon: +49 (941) 60098-0
Telefax: +49 (941) 60098-100
http://relyon-plasma.com/
Marketing Manager
Telefon: +49 (941) 60098230
E-Mail: c.wimmer@relyon-plasma.com
