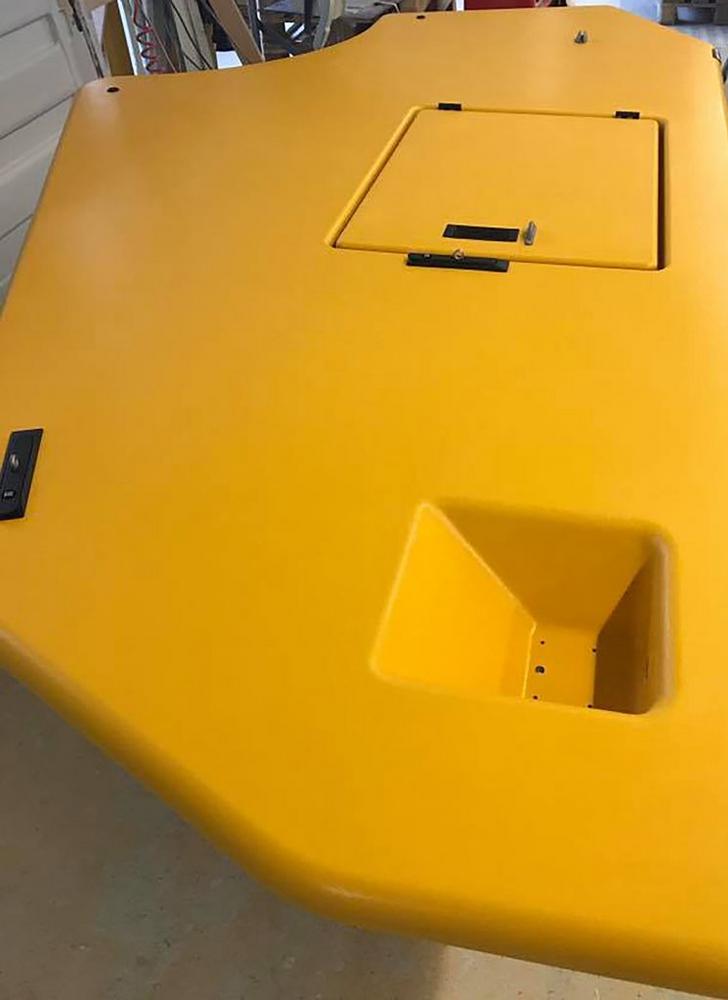
FreiLacke low-styrene gel coats ready for market
Gelcoats are durable coloured coatings that are applied directly to the moulds to afford the mouldings long-term protection from moisture, UV rays and impact damage. They contain not insubstantial amounts of styrene, a material that is hazardous to health and which can give off unpleasant smelling vapours even in smaller concentrations below the official workplace threshold. “Companies are frequently called upon to reduce odour emissions,” said lab technician Carolin Neubert, who is also responsible for composite development at FreiLacke. “Which is why institutions for statutory accident insurance and prevention carry out regular checks of the so-called MWC value (Maximum Workplace Concentration) at both the manufacturers and the users.”
GRP specialists Oechsle were also faced with this challenge and discussed the reduction of odour emissions with their longstanding partner FreiLacke, which has been supplying the plastic specialist since 1997. “Based on the manufacturing process the components are coated in the afternoon; that involves around 25 sizeable components inside a single hall. In certain circumstances that could lead to a high concentration of styrene emissions, especially given that we are quite busy and demand is steadily increasing. To prevent any problems arising we turned to our suppliers directly at the end of 2019,” explained deputy general manager Thomas Oechsle. “Although we continually maintain ongoing productive contact with FreiLacke anyway.”
50 monomers tested
Coating specialists at FreiLacke have long been researching styrene-free and low-styrene coating systems. “Following discussions with raw material manufacturers and in the wake of various trade fair visits, we have repeatedly tested a variety of monomers in respect of styrene. Styrene has the major benefit of having an extremely low viscosity while at the same time being highly reactive. As a result of its functional groups, it binds very well within the gelcoat,” explained Neubert. These then were the challenges that the monomers had to live up to. The FreiLacke lab tested the characteristics of around 50 different monomers in total. Neubert herself had previously worked on the development of UV coatings and knew the respective suppliers. “That’s why I was tasked with the project from the outset,” she declared. “As a result of this previous experience we were quickly able to begin initial testing soon after receiving the request from Oechsle.”
9 months from initial request to the finished product
On behalf of Oechsle we tested the monomers in relation to their processing, reactivity, weather resistance, viscosity and shelf life – and always in comparison with products containing styrene. “Using an alternative monomer we were ultimately able to manufacture a low-styrene gelcoat that achieved better results in terms of weather resistance and shelf life than the standard system,” reported the lab technician. After commensurate production testing at Oechsle and further tests, Oechsle ultimately gave the new system the green light. “During processing, the laminator himself observed no apparent difference. Although he did comment that the odour was suddenly much reduced,” said Thomas Oechsle, speaking of the conversion within the company. He explained with satisfaction how development had taken but a mere nine months.
Additional colours ordered
Carolin Neubert explained that the reduction level differs from gelcoat to gelcoat. The styrene content at Oechsle dropped between 17 and 23 percent – in other words by almost a quarter in some cases. “Due to the base resin used in the gelcoats (ortho and/or ISO NPG) we still have a percentage of styrene within the systems, but no additional styrene is added to set the viscosity or reactivity. And that was the major challenge: given that the processing quality and physical data needed to effectively remain the same as the systems with styrene content,” said the coating specialist.
After Oechsle had successfully introduced the first two gelcoats for machine components, the customer readily enquired about additional colours. Furthermore, the new system is now also the subject of discussion at other customers of the Black Forest coating specialists; with developments ongoing.
Systematic solutions.
FreiLacke has stood for innovative paints and coatings since 1926. The family-owned company has already entered its third generation and develops customised solutions for clients from the wheel and vehicle manufacturing industries, as well as those in the fields of mechanical and apparatus engineering, job coating, rail vehicles, wind power, functional furniture, storage technology, construction and sanitation, directly through its 600 employees at its Döggingen base in the Black Forest.
As a modern family-run company now in its third generation, the safeguarding of the head office is just as important as our worldwide sales and our international subsidiaries and partners.
The product range of Europe’s leading system coating provider covers the entire spectrum from industrial coatings, powder coatings and electrodeposition coatings to composite solutions.
International sales are handled by a global network of subsidiaries and partners around the world.
Environmental protection has always been a key priority for FreiLacke.
Therefore, the company makes every effort to develop environmentally friendly products, reduce emissions, packaging materials and waste and use resources sparingly.
In 2019, FreiLacke was honoured as one of the top 100 employers in Germany in the “Great Place to Work” competition and attaches great importance to training with a quota of 10%.
FreiLacke | Emil Frei GmbH & Co. KG
Am Bahnhof 6
78199 Bräunlingen
Telefon: +49 (7707) 151-0
http://www.freilacke.de
Head of Marketing
Telefon: +49 (7707) 151-270
Fax: +49 (7707) 15155-270
E-Mail: o.zanner@freilacke.de
Emil Frei GmbH & Co KG
Telefon: +49 (7707) 151-0
E-Mail: info@freilacke.de
Oechsle GmbH
Telefon: +49 (7161) 817800
E-Mail: info@oechsle.net
