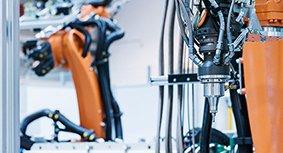
RAMPF Bonding & Casting Technology For Groundbreaking Electric Mobility Production Platform
Cell contact systems are a fundamental element of electric drivetrains. They connect the individual battery cells to modules and ensure the drivetrain is electrified. In addition, they use integrated sensor technology to carry out important battery management functions, including measuring voltage and temperature.
Based in Reutlingen, Germany, MANZ AG is a market leader in automating complex, high-precision production facilities for microelectronics components, specializing in the automated manufacture of cell contact systems at an early stage. The company’s pioneering modular LightAssembly platform combines all the necessary technologies such as assembly, bonding, and soldering, and even functional tests so as to meet the market’s high requirements in terms of quality, speed, and cost-efficiency.
DR-CNC dispensing robot for automated bonding and casting processes
MANZ develops product-specific production solutions for cell contact systems that are used with lithium-ion batteries, catering specifically to the needs of the automotive industry. DR-CNC dispensing robots from RAMPF Production Systems were integrated into two of these highly complex assembly lines to carry out fully automated bonding and casting processes.
Specifically designed to be integrated into production lines, the DR-CNC dispensing robot is equipped with cutting-edge control technology that ensures perfect interplay between the dispensing process and motion sequences.
The double-axis system enables continuous production without any interruptions for maintenance and cleaning, while the swiveling work-piece holder operates without media supply. The dispensing processes for the bonding and casting materials are precisely coordinated with the respective curing process, and the quality of the process is constantly monitored via an integrated camera system.
The dispensing robot is equipped with the intuitive RAMPF HMI (human-machine interface) for the dispensing process and controlling the CNC axes. All parameters relevant to the process are mapped in real time and support the proactive maintenance of the systems. Together with the fully redundant design of the dispensing system, this predictive maintenance is a key component of RAMPF’s holistic, failsafe service concept for the long-term availability and maximum productivity of the dispensing robots.
Stefan Huber, Director of Project Management at RAMPF Production Systems – “The production solution for lithium-ion batteries developed by MANZ provides the highest production speeds, precision, and quality, and sets new standards for the electric mobility sector. This holistic concept is also in line with our own approach of automating production processes with integrated dispensing technology. The customized solutions we have developed offer a high level of flexibility and can rapidly be integrated into production lines.”
RAMPF Production Systems is one of the world’s leading suppliers of innovative systems for processing single-, dual-, and multi-component reactive plastic systems.
In addition to its core competence of mixing and dispensing technology, the company based in Zimmern ob Rottweil, Germany, provides product-specific automation concepts with integrated parts transport and heat treatment, assembly and joining technology, as well as logistic and quality assurance solutions.
The customer-specific solutions include integrating both surface activation processes as well as testing and measuring technology to safeguard production processes.
Prototypes and small series for customers are produced in the application-engineering center.
This wide-ranging expertise enables RAMPF Production Systems to provide its customers with complete solutions for their production facilities.
RAMPF Holding GmbH & Co. KG
Albstraße 37
72661 Grafenberg
Telefon: +49 (7123) 9342-0
Telefax: +49 (7123) 9342-1111
http://www.rampf-group.com
PR
Telefon: +49 (7123) 9342-1045
Fax: +49 (7123) 9342-2045
E-Mail: Benjamin.Schicker@rampf-gruppe.de
