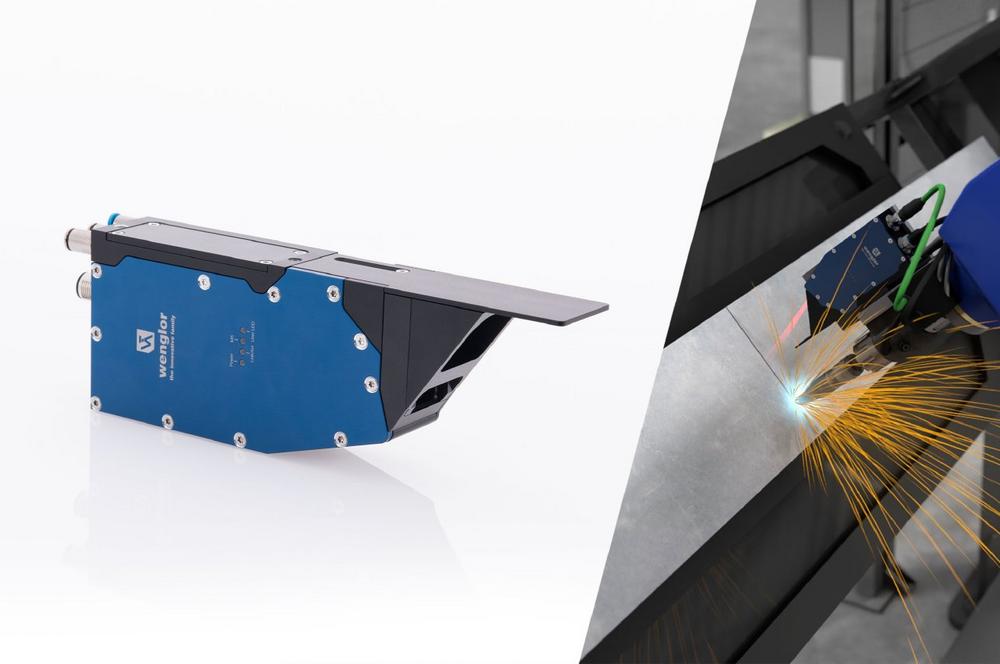
Automated Weld Seam Tracking: weCat3D MLZL 2D/3D Profile Sensors Enable Exact Seam Placement in Robot Welding Cells
A 2D/3D profile sensor made for welding robots: The slimline housing of the MLZL with integrated cooling and rinsing enables easy and space-saving installation directly on the welding torch. Thanks to the small housing dimensions of only 33 × 183 × 69.8 mm, the robot can therefore also operate in narrow corners. "The MLZL 2D/3D profile sensor does not require any additional protective housing, nor does it need to be tilted for alignment," explains wenglor product manager Dr. Sascha Reinhardt. "The design also offers sufficient protection against welding spatter and disturbing ambient light." Despite the harsh industrial environment, the welding sensor provides high-quality profiles for precise joint detection. Optionally equipped with a red or blue laser, users can choose between three laser classes: 2M, 3R or 3B. "The MLZL relies on the advanced laser technology of the weCat3D series and thus delivers outstanding profile quality for optical seam tracking," says Dr. Reinhardt. "This sensor has been specially adapted and optimized for the high demands in welding robots, but in particular for the complex task of optical tracking of weld seams – both in terms of hardware and software."
wenglor engineers tested and developed the special triangulation sensor as part of an EAP (Early Adopter Program) together with customers from the welding industry. The feedback and know-how collected from this program ultimately flowed into the MLZL. “We were able to incorporate many practical experiences directly into the development and thus obtained extremely precise information in advance about what is important in automated welding processes, where users face the greatest hurdles and what their wishes are.”
Software Update with New Function: uniVision 2.5.0 for Welding Applications
In its current update 2.5.0, the configurable standard software uniVision receives a stand-alone module specifically for weld seam tracking. For users, this means that welding applications can be set up in just a few clicks. “Thanks to the robust algorithms, tracking points can be reliably determined even in the event of faults in the joint course, such as with datum points. Predefined templates, where all common joint types are saved, significantly reduce the configuration work,” explains Dr. Reinhardt. The results can then be visualized on a web-based basis. Several interfaces are available for direct integration into robot controls from Kuka, Fanuc, ABB, Kawasaki and Yaskawa as well as their software. In concrete terms, this means: Welding processes can now be implemented with less effort, more functions and better results.
The Welding Solution for Every User
The new combination of software and hardware offers flexible welding solutions for every user. We always differentiate between applications with or without robot integration. The most convenient and comprehensive system consists of a sensor, control unit with pre-installed uniVision software application and optional robot interface. “For this purpose, the system was developed as a complete solution as part of the EAP. However, there are also other combinations with or without control unit and customer-specific integration software, meaning that we can offer the right solution to suit every individual customer requirement,” Dr. Reinhardt continues.
That’s uniVision, the All-in-One Software
The parameterizable uniVision standard software is used to analyze images and height profiles in the field of industrial image processing. Two and three-dimensional data from smart cameras, vision systems, smart 2D/3D profile sensors and IPCs (control units) with 2D/3D profile sensors can also be evaluated. Up to 25 different software modules and different templates are available to users in total depending on the selected hardware.
The Highlights at a Glance
• Compact housing (33 × 183 × 69.8 mm)
• Robust design with high IP67 protection
• High profile quality (1,280 points per profile)
• Large working range from 74 to 158 mm
• Large measuring range in X from 39 to 62 mm
• Integrated cooling and rinsing
• Laser class 2M, 3R or 3B
• Red light or blue light
• Special uniVision software module for weld seam tracking
• Robot interfaces for ABB, Fanuc, Kuka, Yaskawa and Kawasaki
• Industrial interfaces PROFINET and EtherNet/IP™ for easy integration into controls
wenglor develops innovative automation technologies, such as sensors, security and 2D/3D camera systems with state-of-the-art communication standards for the global market. Founded as a two-man business in 1983, the family company has since evolved into one of the most important international sensor suppliers with around 1,000 employees around the world. The company with headquarters on Lake Constance in Tettnang, Germany, meets industrial automation challenges for customers in all industry sectors – from automotive manufacturing to the packaging industry. More than 60,000 customers from 45 countries all over the world are already placing their faith in wenglor’s innovative products.
wenglor sensoric group
wenglor Straße 3
88069 Tettnang
Telefon: +49 07542 5399 0
Telefax: +49 07542 5399 988
http://www.wenglor.com
Pressereferent
Telefon: +49 (7542) 5399-718
E-Mail: fabian.repetz@wenglor.com

