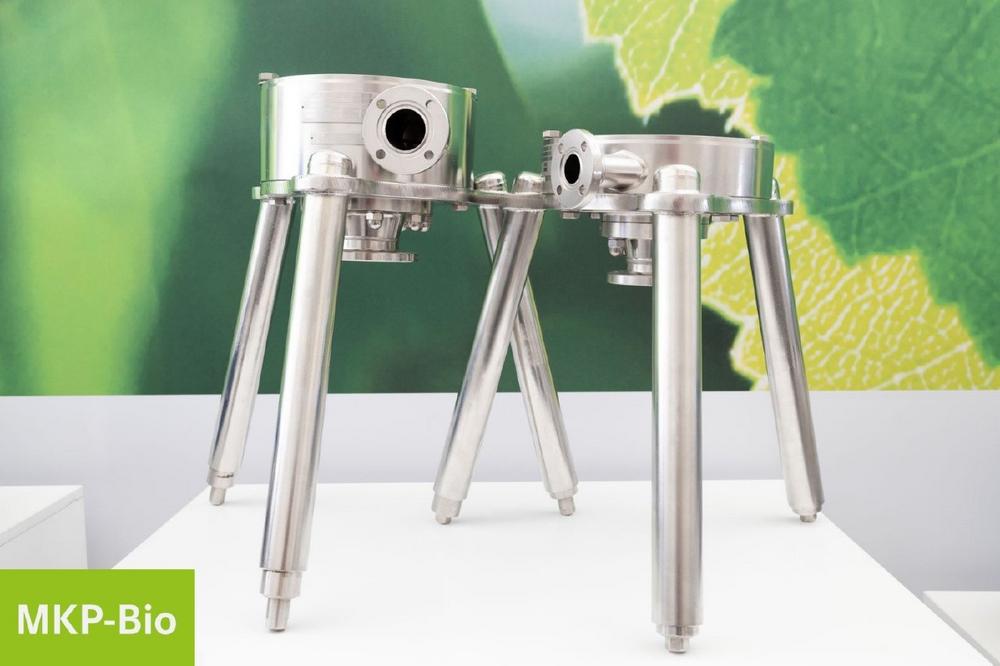
Customized pump solutions: efficient – hygienic – bacteria-tight
With the corona pandemic, pharmaceutical manufacturers have come under extraordinary pressure – sometimes to the limits of their performance capabilities – with the rapid development, approval and production of suitable vaccines, as well as the provision of sufficient quantities of test fluids and disinfectants. Military conflicts, climate change and supply chain failures are making food production more difficult worldwide.
Despite and due to all priority and urgency on the one hand and resource/cost pressures on the other, the quality of the products is of paramount importance. Production plants in the pharmaceutical and food industries must fully meet the operating company’s high standards as well as applicable regulations and laws with respect to quality, validity and safety. In addition to trained and qualified personnel, this occasionally necessitates aseptic process conditions in the production.
Manufacturers of process plants and components and the companies that operate them have to comply with the requirements and rules of the applicable directives, regulations and laws, e.g.:
- 3-A (US Sanitary Standard)
- EHEDG (European Hygienic Design Engineering and Design Group)
- FDA (Federal Drug Administration)
- GMP (Good Manufacturing Practice)
The goal is to design plants and components in such a way that the materials that come in contact with the product do not contaminate the pharmaceuticals, active ingredients and foodstuffs and that all components and surfaces are easy to clean and sterilise. Both the production and cleaning processes must be reliable and capable of being validated. Hygienic pumps play a key role in the pumping of fluids in both primary and secondary processes (product pumping, process water, CIP/SIP cleaning).
CP Pumpen was one of the first manufacturers to successfully establish a magnetic drive process pump on the market that was developed, tested and approved in accordance with the EHEDG guidelines.
The MKP-Bio series from the Swiss pump manufacturer from Zofingen has met the strict requirements for a dead-space-free construction according to hygienic design, 100% emptying of residues, CIP/SIP capability, etc. for over 20 years. The special feature of the single-stage centrifugal pump is the seal-free construction: Whereas a sealing gap separates the product side from the atmosphere side in pumps sealed by mechanical seals, magnetic drive pumps are hermetically sealed and free from dynamic shaft/casing seals. This means that in the event of a leak or an unforeseen standstill, no germs, bacteria or microorganisms can pass through a sealing gap and contaminate the product side.
The pump interior consists of a few sturdy individual parts. The impeller can simply be removed without tools for validation. The parts that come into contact with the media have a minimum surface quality of Ra 0.8, the inner edges have a radius of R 3 and the surfaces have a minimum inclination of 3°. Thanks to their vertical installation, the MKP-Bio pumps can be emptied completely through the suction branch without additional flushing, emptying or venting connections. The existing pump connections can be used for CIP and SIP.
Author: Stefan Bartosch, Area Sales Manager South Germany, CP Pump Systems
CP Pumpen AG
Im Brühl
CH4800 Zofingen
Telefon: +41 (62) 74685-85
Telefax: +41 (62) 74685-86
http://www.cp-pumps.com
Manager Marketing und Communications
Telefon: +41 (62) 7468-532
Fax: +41 (62) 7468-586
E-Mail: sarah.brutschi@cp-pumps.com
Telefon: +41 (62) 74685-26
Fax: +41 (62) 74685-86
E-Mail: semi.trabelsi@cp-pumps.com

