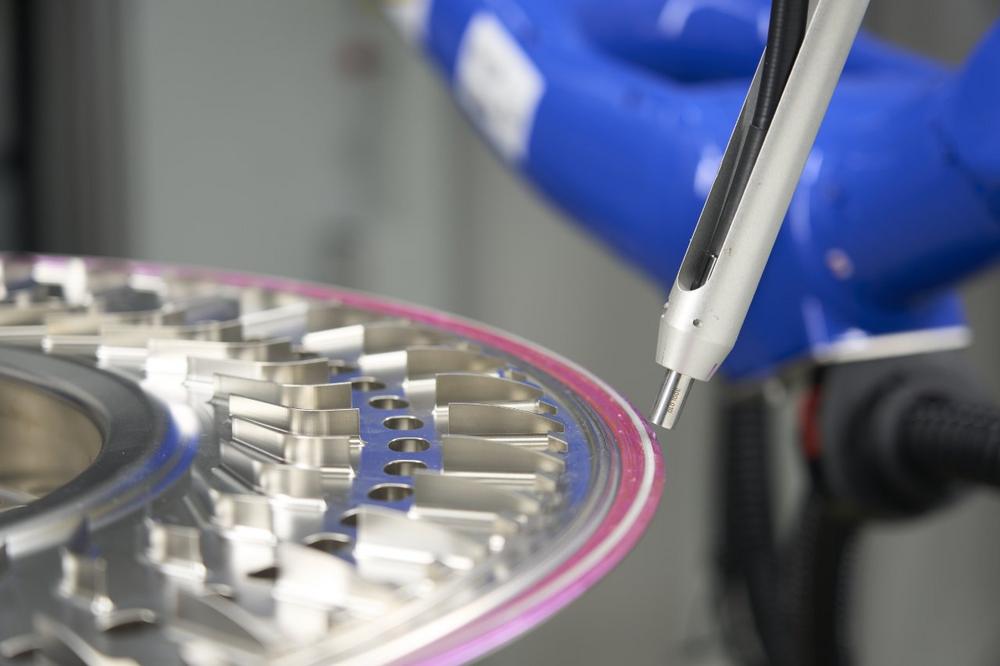
Dymax SpeedMask®: Process Automation Shortens Throughput Times and Reduces Costs
Surface treatment, for example thermal spraying, is a key manufacturing process used on aero engine parts. In this process, certain surfaces must be temporarily masked with millimeter precision to protect them from inadvertent treatment during the process. For a long time, maskants were manually applied by affixing adhesive tapes, silicone rings, masks, or metal covers, all of which required a great deal of time and care. Growing product demand and increasingly complex shapes made it challenging for MTU to provide a precise and cost-effective temporary protection for sensitive component surfaces. When Thomas Kaltenecker, production planner at MTU Aero Engines, became acquainted with Dymax’s light-curable maskants, he was certain the material would reduce challenges and improve the overall process. Dymax SpeedMask® maskants are easy to apply even to the most complex shapes and geometries and offer excellent properties to withstand high temperatures during finishing processes. Moreover, Dymax maskants can be seamlessly integrated into automated dispense and curing systems – in other words, exactly what MTU was looking for.
Programmable robotic arms, together with the Dymax SpeedMask®, perform this difficult task with ease. With various dispensers, the gel-like material is applied fully automatic with high precision to the surface or even sprayed to cover a larger area of the component. A brief exposure to UV light at the proper intensity and wavelength ensures that the material cures within seconds. The masking can be removed just as quickly after going through the various surface treatments without leaving any residue. This not only saves manufacturing time and production costs, but also has a positive effect on the sustainability of the process, as the error rate is reduced to nearly zero tolerance levels.
Thomas Kaltenecker enthusiastically stated, "Several hundred components in our portfolio undergo various surface treatment processes during their production, such as thermal coating, shot peening, electroplating, etc. The respective Dymax SpeedMask® masking processes can be adapted quickly and easily for this, resulting in significant time savings in our production process."
Virginia Hogan, Senior Global Business Development Manager at Dymax, added, "We are delighted that Dymax was able to support a total solution for MTU Aero Engines. Our application engineers, system integration, and internal sales teams worked together to not only provide a great maskant but deliver a fully automated dispense and curing machine. We are happy to continue to support MTU in making them more capable and their process more efficient."
Dymax is specialized in advanced light-curing materials and leading supplier of systems solutions to increase efficiency in production processes. The Wiesbaden, Germany, based company not only develops oligomers, adhesives, coatings and light-curing systems for applications, but also assists manufacturers in developing individual process solutions. Major markets to be served include medical device, electronics, aerospace and automotive.
Dymax Corporation is headquartered in Torrington, Connecticut, USA. Alongside Germany, further subsidiaries are located in Ireland, Hong Kong, Singapore and Korea. Dymax employs more than 450 people worldwide.
DYMAX Europe GmbH
Kasteler Straße 45
65203 Wiesbaden
Telefon: +49 (611) 962-7900
Telefax: +49 (611) 962-9440
https://de.dymax.com/
Product Management EMEA
E-Mail: lduhmmccann@dymax.com