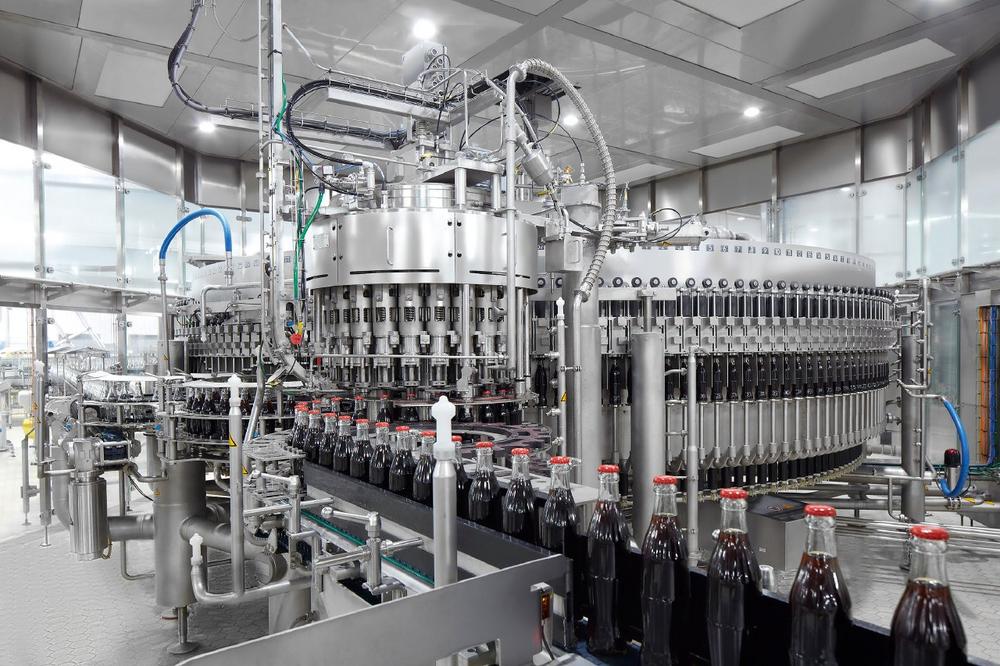
Gut sortiert
Als der Getränkehändler Wilhelm Müller im Juli 1950 die Abfüllrechte für Coca-Cola in Deutschland erwirbt, schafft er die unternehmerische Basis für den Betrieb, der sich noch heute in Mannheim befindet. Erfolgten viele Arbeitsschritte wie Sortierung und Qualitätssicherung anfangs manuell, wird 1965 die erste vollautomatische Anlage in Betrieb genommen: Sie entnimmt die leeren Flaschen aus den Getränkekisten, setzt die vollen wieder ein und inspiziert jede einzelne mit Hilfe von Prüfeinrichtungen automatisch.
In den Sechziger- und Siebzigerjahren hält Müller 18 Jahre in Folge den Verkaufsrekord aller selbstständigen Coca-Cola Konzessionäre in Deutschland. Nachdem er 1971 auf dem Höhepunkt seines Erfolgs verstirbt, übernimmt seine Frau die Führung des Unternehmens. Die Witwe trifft 1983 die mutige Entscheidung, ein ganz neues Werk zu bauen – am heutigen Standort in Mannheim-Vogelstang. Schon kurz nach der Eröffnung werden auf einer neuen Anlage mehr als 30.000 Flaschen pro Stunde abgefüllt.
Hightech in Mannheim
Heute ist die Produktionsstätte Teil von Coca-Cola Europacific Partners Deutschland (CCEP DE), dem größten Getränkehersteller in der Bundesrepublik. „Unter unseren älteren Mitarbeitenden gibt es noch viele, die sich gerne an die Ära der sogenannten Cola-Müllers erinnern“, sagt Christopher Bee. Der 39-Jährige ist seit sieben Jahren in Mannheim beschäftigt, seit September 2021 in der Funktion des Betriebsleiters. Und tatsächlich gehört der Wilhelm Müller-Stiftung nach wie vor das weitläufige Firmengelände – erst vor zwei Jahren wurde der Mietvertrag um 30 Jahre verlängert. „Bei unserer technischen Ausstattung erinnert allerdings nichts mehr an die Vergangenheit. In den Jahren 2018 und 2019 haben wir insgesamt etwa 50 Millionen Euro in zwei neue Abfüllanlagen investiert. Das waren die bisher größten Investitionen in der Geschichte unseres Standorts. Damit gehören wir in Mannheim zu den technisch fortschrittlichsten Werken von Coca-Cola in Deutschland und Europa.“
Eine der beiden neuen Produktionsstraßen ist eine Mehrweg-Glaslinie des Dortmunder Systemanbieters KHS. „Auf ihr füllen wir insgesamt sechs verschiedene Flaschen ab, davon vier im 200- und zwei im 330-Milliliter-Format. Die kleineren Größen kommen vorwiegend in der Gastronomie zum Einsatz, wo die Verpackung noch ein bisschen mehr hermachen muss als im Einzelhandel. Deshalb gibt es dort für die Marken Coke, Fanta, Sprite und mezzo mix jeweils ein eigenes Flaschendesign. Bei den größeren Behältern, die zusätzlich im Einzelhandel vertrieben werden, verarbeiten wir zwei Formate: Die sogenannte Konturflasche für die Produkte der Coke Familie sowie unsere grüne Multiflasche für Fanta, Sprite und mezzo mix.“
Herausragendes Merkmal der KHS-Linie ist die Sortieranlage, mit der das Leergut dem Reinigungs- und Füllprozess vollautomatisch sortenrein zugeführt werden kann. „Im Prinzip laufen der Sortier- und der Füllprozess auf zwei separaten Anlagen ab. Speziell für unsere Hauptsorten, die 200- und 330-Milliliter-Coke-Flaschen, nutzen wir einen Strang, der die beiden Abschnitte miteinander verbindet. Hier werden die Behälter, die im Wesentlichen sortenrein aus dem Markt zurückkommen, direkt aus der Sortierung in die Produktion geleitet. Sie müssen nicht mehr den Umweg über das Leergutlager nehmen. Das reduziert den Aufwand beim Handling.“ Die anderen fünf Sorten werden aus dem Sortierprozess zunächst in Getränkekisten, dann auf Paletten gepackt, bevor sie bis zu ihrer Befüllung zwischengelagert werden.
Intelligenter Auspacker
Die einzige manuelle Tätigkeit, die angesichts des hohen Automatisierungsgrades der Anlage erforderlich ist, findet gleich zu Beginn der Sortierung statt: Wenn die Kisten ankommen, werden sie von oben gescannt. Liegen zum Beispiel Fremdkörper wie Pappbecher oder Folie darauf, kann die Kiste nicht identifiziert werden. Dann muss in der Handsortierung das störende Element entfernt werden, bevor es wieder in den automatischen Prozess eingeschleust wird. „Der Auspacker ist so intelligent, dass er die größte der Flaschensorten auf ein Band setzt“, erklärt Bee. „Die kleineren werden auf einen anderen Transporteur abgestellt, wo sie vereinzelt und mit Hilfe von Kamerasystemen und Pushern auf verschiedene Bahnen gelenkt werden. Unser Ziel ist es, die Behälter dabei so wenig wie möglich zu manipulieren, also mit der Maschine in Berührung kommen zu lassen. Auf diese Weise können wir die Gefahr möglichst geringhalten, dass bei der hohen Geschwindigkeit etwas umfällt.“ Mit einer Leistung von bis zu 66.000 Flaschen pro Stunde verfügt die Sortieranlage über eine höhere Kapazität als die Mehrweg-Glaslinie, die bis zu 60.000 Flaschen pro Stunde abfüllen kann. Dadurch gerät CCEP in Mannheim mit seinem Leergut selbst in der Hochsaison selten in einen Stillstand.
Hohe Flexibilität
Im ungleichmäßigen Rücklauf der leeren Flaschen kommt es häufig zu Peaks, erklärt Bee. Ein gutes Beispiel sind Musikfestivals, in deren Anschluss mit einer höheren Anzahl von Glasflaschen als üblich zu rechnen sei. „Die Besonderheit der Anlage ist, dass sie auf diese Spitzen individuell reagieren kann“, sagt Bee. „Um das zu ermöglichen, haben wir während der Inbetriebnahme mit einem externen Dienstleister eine Live-Simulation durchgeführt. Auf Basis der Ergebnisse konnten wir im engen Austausch mit KHS Optimierungen und Feinjustierungen am Layout vornehmen, die zu einer Verbesserung der Performance geführt haben. Das war sehr hilfreich, vor allem da wir während der Pandemie aufgrund von Schließungen in der Gastronomie nicht unter realen Bedingungen arbeiten konnten.“
Ein Highlight der neuen Mehrweg-Glaslinie von KHS ist für Christopher Bee die Doppelend-Flaschenreinigungsmaschine Innoclean DM: „Bei jeder abgefüllten Flasche sparen wir im Schnitt bis zu 40 Prozent Wasser und Energie im Vergleich zu Anlagen früherer Generationen“, betont Bee. Dafür sorgt zum Beispiel die Frischwasserregelung, die sich mittels Regelventil automatisch an die jeweils aktuelle Maschinenleistung anpasst. Gut für die Energiebilanz seien ebenso die neuen Eco-Carrier: Sie wiegen rund ein Viertel weniger als bisherige Flaschenkörbe und verfügen über seitliche Öffnungen, die ein besseres Ausspülen erlauben. Das reduziert die Laugen- und Wärmeverschleppung und damit den Kühlbedarf innerhalb der Maschine. Und steht einmal kurzzeitig kein Leergut bereit, wechselt die Reinigungsmaschine in einen energiesparenden Ruhezustand, den neuen Standby-Modus: Dafür verringert das Liquid Efficiency Spraying System (LESS) den Druck der Spritzpumpen während der Stillstandszeiten auf 0,3 bar und senkt so den Stromverbrauch um bis zu 80 Prozent.
Auf dem Weg zu Netto-Null-Emissionen
Wie in immer mehr Unternehmen, spielt das Thema Nachhaltigkeit bei CCEP eine große Rolle: Bis 2030 sollen die Treibhausgasemissionen in Europa im Vergleich zu 2019 um 30 Prozent sinken. Und bis 2040 will CCEP hier das Ziel von Netto-Null-Emissionen erreichen und keine Auswirkungen mehr auf das Klima haben. Berücksichtigt werden dabei nicht nur die Emissionen aus dem Kerngeschäft. Vielmehr sucht man entlang der gesamten Wertschöpfungskette nach signifikanten Einsparpotenzialen bei den Treibhausgasemissionen. Das betrifft die Investition in einen energie- und ressourcensparenden Maschinenpark ebenso wie die 2.300 Dienst- und Nutzfahrzeuge, die bis 2025 komplett auf E-Antrieb umgestellt werden. Weitere Emissionen vermeidet Coca-Cola in Deutschland durch sein engmaschiges Produktions- und Distributionsnetzwerk, das Getränke weitgehend regional herstellt und ausliefert. Wo das nicht möglich ist, setzt der Getränkehersteller verstärkt auf den Schienenverkehr: 2021 wurde mit DB Cargo ein Güternetz aufgebaut, das 13 Standorte miteinander verbindet. Im gleichen Jahr konnten so bereits 1,7 Millionen Lkw-Kilometer und 1.000 Tonnen CO2 eingespart werden.
Coca-Cola und KHS: Erfolgreiche Zusammenarbeit an mehreren Standorten
Im Coca-Cola Netzwerk ist Mannheim auf dem Weg zu einer klimaschonenderen Produktion das jüngste von insgesamt drei Großprojekten, die KHS in den vergangenen Jahren mit CCEP Deutschland umgesetzt hat. Den Anfang machte 2015 eine Dosenlinie im rund 70 Kilometer entfernten Karlsruhe. „Die Linie mit einer Leistung von bis zu 120.000 Dosen pro Stunde überzeugt beispielsweise durch unseren ressourcensparenden Tunnelpasteur“, sagt Robert Fast, Projektleiter bei KHS. „Er nutzt Wasser, das aus dem Leerdosen-Rinser aufgefangen wird. Und der Einsatz ionisierter Luft im Prozesswasser ermöglicht es, den Einsatz von Chemikalien gegenüber dem Standardverfahren zu reduzieren.“ Ebenso klimafreundlich sei die Verpackungsmaschine, erklärt Fast. Deren Gasbrenner im Schrumpftunnel reduziere den Verbrauch von elektrischer Energie um bis zu 75 Prozent sowie den CO2-Ausstoß um bis zu 60 Prozent.
Im niederrheinischen Mönchengladbach hat KHS 2017 eine Einweg-PET-Linie mit einer Kapazität von bis zu 42.000 Flaschen pro Stunde installiert. „Einer der Gründe, warum wir den Zuschlag erhalten haben, war unser umfassendes Konzept für Strom-, Wasser- und Gaseinsparungen“, berichtet Fast. „Ein Beispiel ist die Streckblasmaschine InnoPET Blomax. Sie erzielt durch ihre Near-Infrared(NIR)-Technologie des Ofens, in dem die Preforms vor dem eigentlichen Streckblasvorgang aufgeheizt werden, eine Senkung des Energiebedarfs.“
Dass Investitionen in diesem Umfang nicht die Regel sind, weiß natürlich auch Christopher Bee. Umso glücklicher schätzt er sich, dass er diese Erfahrung in „seinem Werk“ machen durfte. „Zu sehen, wie ein Standort sich weiterentwickelt und die ganze Bandbreite der Produktion abbildet, ist schon etwas Besonderes“, sagt er lächelnd. „Dabei ist klar, dass wir das in uns gesetzte Vertrauen in Form von sehr guter Leistung zurückgeben werden.“ Das hätte der „Cola-Müller“ sicher genauso gesehen.
Auf einen Blick: Coca-Cola Europacific Partners
Mit 33.200 Mitarbeitenden und 1,75 Millionen Kunden in 29 Ländern ist Coca-Cola Europacific Partners (CCEP) eines der führenden Konsumgüterunternehmen weltweit. Der Getränkehersteller produziert und verkauft beliebte Getränkemarken wie Coca-Cola, Fanta und Sprite – in Europa, im Pazifik und in Indonesien. Die CCEP Deutschland GmbH ist Teil von CCEP und mit einem Absatzvolumen von mehr als 3,5 Milliarden Liter (2021) das größte deutsche Getränkeunternehmen. Bundesweit beschäftigt der Abfüller rund 6.500 Mitarbeitende.
Die KHS Gruppe ist einer der weltweit führenden Hersteller von Abfüll- und Verpackungsanlagen in den Bereichen Getränke und flüssige Lebensmittel. Zur Unternehmensgruppe zählen neben der Muttergesellschaft (KHS GmbH) diverse ausländische Tochtergesellschaften mit Produktionsstandorten in Ahmedabad (Indien), Waukesha (USA), Zinacantepec (Mexiko), São Paulo (Brasilien) und Kunshan (China). Hinzu kommen zahlreiche internationale Verkaufs- und Servicebüros. Am Stammsitz in Dortmund sowie in ihren weiteren Werken in Bad Kreuznach, Kleve, Worms und Hamburg stellt die KHS moderne Abfüll- und Verpackungsanlagen für den Hochleistungsbereich her. Die KHS Gruppe ist eine 100-prozentige Tochtergesellschaft der im SDAX notierten Salzgitter AG. 2021 realisierte die Gruppe mit 4.954 Mitarbeitenden einen Umsatz von rund 1,245 Milliarden Euro.
KHS GmbH
Juchostr. 20
44143 Dortmund
Telefon: +49 (231) 569-0
Telefax: +49 (231) 569-1541
http://www.khs.com
Presse- und Öffentlichkeitsarbeit
Telefon: +49 (251) 625561-243
E-Mail: deppe@sputnik-agentur.de

