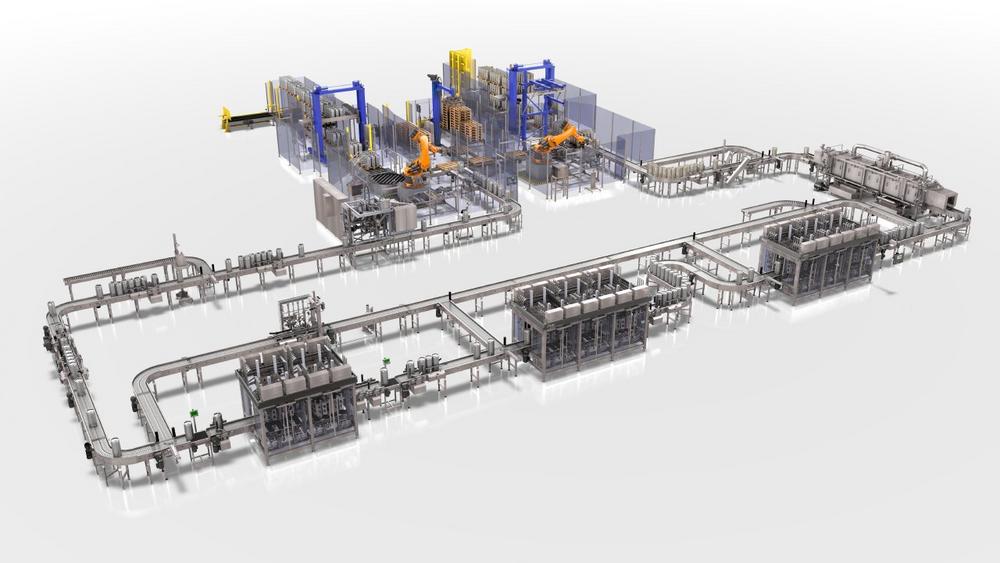
The fully automatic Transversal kegging line from KHS for greater line efficiency
Compared to standard market systems, the Innokeg AF-C Transversal kegging machine scores on not one but several counts, declares Roger Daum, keg product manager at KHS. “The biggest and most obvious difference lies in its innovative conveying system. The conventional transversal conveyor setup used to date has separate belts for infeed and discharge upstream and downstream of the actual machine. The KHS design is consciously different and transports the kegs through the middle of the paired opposite processing stations on a single conveyor belt. On this they are pushed in and out of the line to the side.” The great advantage of this concept is that on the Innokeg AF-C Transversal there are no conveyors separating the operator from the machine. The stations are thus freely and much more easily accessible for maintenance and repair. The space-saving system also has a smaller footprint in the production shop. Moreover, with its inverse ratio of conveying to processing stations (compared to standard machinery) the KHS system is more powerful and can process up to 500 kegs per hour.
Modular and flexible
Another key difference of KHS’ keg engineering is its modular design that means lower procurement costs and that the Innokeg AF-C Transversal can grow to accommodate rising production capacities. “We combine two modules with two respective processing stations in a single block frame. Thanks to its compact design the block fits into a standard overseas container,” is how keg product manager Daum explains the principle of the system. Within this frame all kinds of cycle are feasible. “A machine can be configured with up to four blocks with two modules each. This is equivalent to 16 treatment heads that can function as a pre-, main or combined washer or filler respectively,” Daum emphasizes. This provides plenty of scope when configuring the overall line: twelve washing stations can be combined with eight racking stations, for instance, to balance the different cycle times. Individual modules in the block can initially be left empty and simply fitted with further processing stations at a later date should the necessity arise.
All-rounder for all formats
Another distinctive feature of the KHS Innokeg AF-C Transversal is that it can process practically all standard market container sizes and formats. Apart from the fact that no format parts have been used anywhere on the conveying system, thus rendering changeovers superfluous, if required request the entire line can be adjusted to different keg heights and diameters fully automatically. This optional system also recognizes whether the incoming kegs are returnable or one-way containers. The latter then travel straight to the filler through the deactivated washing machines without any conversion or treatment.
Right down the line
Before the kegs on the kegging line reach the Transversal modules, they are lifted from the pallet by the KHS Innopal RK palletizer with its six-axis articulated robot and placed on the conveyor. An on-demand turner with a fitting position detector and decapper ensures that the kegs are properly aligned and prepared for washing and racking. They are again separated and centered prior to exterior washing. In the washing machine a height control unit makes sure that slim kegs especially aren’t downed by the high water pressure of the cleaning nozzles.
The counterflow and pulsed cleaning processes yield optimum results at the pre- and main washing phases. Between these two steps the kegs are filled with caustic and left to soak, with the length of the conveyor determining the duration of the soaking time.
Filling is precise and regulation-compliant – thanks to the KHS Direct Flow Control filling system and gross/tare weighing that complies with the European Measuring Instruments Directive. Finally, ‘bad’ kegs or incorrectly filled containers that fall short of their nominal filling volume, for example, are emptied and removed from the line.
The kegs are then checked for leakage before they are sealed with a cap – if intact – and labeled by inkjet. Faulty kegs are discharged where necessary. At the end of the line the kegs are set down on pallets by a second KHS palletizing robot. This is equipped with double keg grippers whose heads can also be changed over fully automatically. “With the Innokeg AC-F Transversal, when it comes to efficiency and flexibility KHS scores on the washing and racking of kegs right down the line, so to speak,” concludes Daum.
At a glance: the Innokeg AC-F Transversal
- Less space needed thanks to the central conveyor segment
- Optimum access for maintenance and repair
- Modular design for flexible expansion
- Suitable for almost all market-standard returnable and non-returnable kegs
- Fully-automatic adjustment to different formats
- Up to 500 kegs per hour
The KHS Group is one of the world’s leading manufacturers of filling and packaging systems for the beverage and liquid food industries. Besides the parent company (KHS GmbH) the group includes various subsidiaries outside Germany, with production sites in Ahmedabad (India), Waukesha (USA), Zinacantepec (Mexico), São Paulo (Brazil) and Kunshan (China). It also operates numerous sales and service centers worldwide. KHS manufactures modern filling and packaging systems for the high-capacity range at its headquarters in Dortmund, Germany, and at its factories in Bad Kreuznach, Kleve, Worms and Hamburg. The KHS Group is a wholly owned subsidiary of the SDAX-listed Salzgitter AG corporation. In 2021 the KHS Group and its 4,954 employees achieved a turnover of around €1.245 billion.
KHS GmbH
Juchostr. 20
44143 Dortmund
Telefon: +49 (231) 569-0
Telefax: +49 (231) 569-1541
http://www.khs.com
Presse- und Öffentlichkeitsarbeit
Telefon: +49 (251) 625561-243
E-Mail: deppe@sputnik-agentur.de