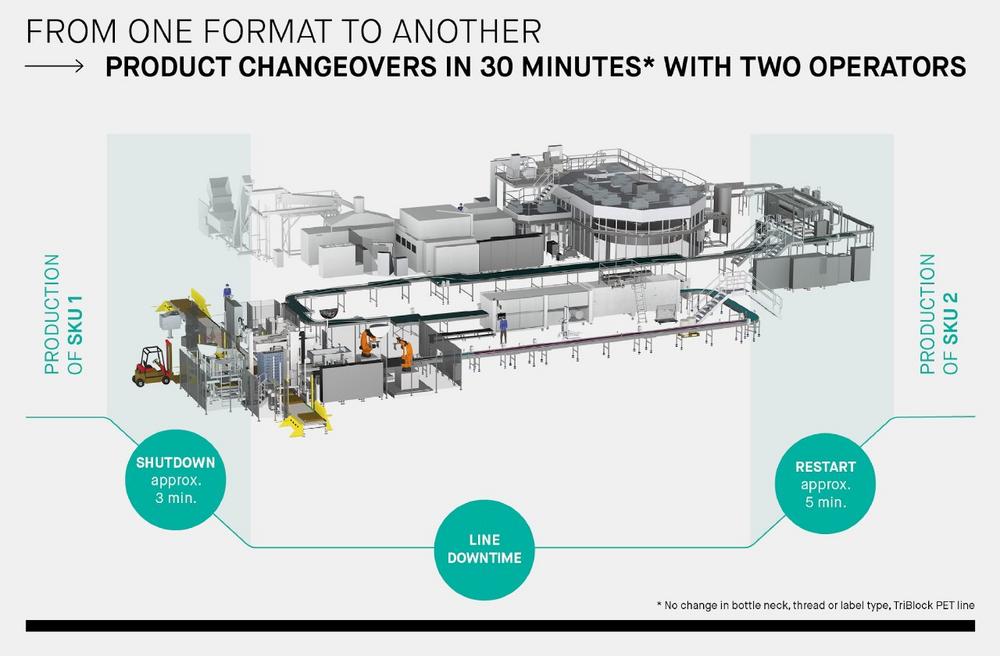
No time to lose: KHS InnoPET iflex automated line changeovers
Beverage producers today face a growing number of challenges, particularly regarding the filling and packaging of their products. Consumers are becoming ever more environmentally aware and demanding ‘green’ packaging that has as little impact on the climate as possible while expecting this to be convenient, safe and inexpensive. End users also want to be able to choose from an increasingly diverse range of beverages and packaging styles.
The resulting constant rise in item variety means that beverage producers need to frequently changeover their lines. This naturally affects the overall equipment efficiency (OEE)[1] and often costs them lots of time and money – and this against a background of increasing regulation and growing economic pressure. On the one hand, the beverage industry is subject to strict provisions governing the avoidance of plastic waste, the recycling of containers and secondary packaging and the reduction of carbon emissions. On the other, it needs to boost efficiency and productivity in order to cut operating and personnel costs – not least by using technical equipment that is easy to operate.
Modular automation concept
This is where KHS comes in with its new InnoPET iflex, a modular automation concept that has initially been developed for PET lines with a large number of SKUs. With fast, reliable and reproducible changeovers it significantly boosts the OEE. If no changes to the bottle neck, thread or label type need to be made, formats can be switched over from one SKU to another in 30 minutes – including running the system empty and starting it up again.[2] A simple product changeover can even be performed within ten minutes.[3] These figures apply to outputs of up to 50,000 bottles per hour holding between 330 milliliters and 1.5 liters of still or carbonated beverage.
“With the iflex option from KHS up to 80% of all manual line conversion tasks are superfluous,” explains Denis Hanau, head of the PET Project Processing Product Division at KHS. “Some process steps already require hardly any operator intervention at all. Full automation wouldn’t be economically viable here, however, meaning that some tasks are either semiautomatic or carried out by hand as in the past. This means that our system saves a total of 3.5 operator hours during format changeovers right down the line.”
This is facilitated by machine options that are carefully coordinated with one another and whose degree of automation has been specially optimized to yield shorter changeover times. Parallel to this, supporting software solutions ensure that changeover routines are documented and can be exactly reproduced by the operator at all times. “Thanks to the drastic reduction in the amount of downtime, our system can improve the OEE by up to 20%,” Hanau emphasizes. “With its new option KHS therefore not only increases flexibility with smaller batches or just-in-time production; above all, it also improves the balance between the range of SKUs on the one hand and the cost ratio on the other. And this ultimately strengthens our customers’ competitiveness.”
Varying levels of automation
There are basically two options available on the InnoPET iflex: automated and guided. As the name indicates, in the former the machine is largely automated for quick format changeovers and very efficient line conversion by processes that run in parallel. The most time is saved here: if hygiene-relevant components are replaced by hand during format changeovers, foam cleaning then needs to take place which can take around 30 minutes.
With an automatic changeover, there is no longer any need for cleaning. With its considerable time savings and high reproducibility, the automated iflex variant is designed primarily for beverage producers whose production operations involve very frequent product changeovers. “Bottlers who opt for KHS’ automated line changeovers don’t necessarily have to invest in a new line,” Hanau emphasizes. “On request, some iflex options such as the robotics for automated blow mold changeovers can be retrofitted on select machines.”
Like a pit stop
The guided variant takes the operator through the changeover as quickly, reliably and efficiently as possible. The manual tasks required are displayed on the HMI and in part on a mobile industrial tablet in the form of animated step-by-step instructions for all necessary actions. The completed process steps and work progress are visualized and safety instructions issued.
“This application is recommended to all beverage producers who run product changeovers,” Hanau states. “It’s also attractive to customers who don’t have enough qualified personnel for the night shift, for instance. You can compare this process to a pit stop that can only be performed by experienced personnel and where each task has to be carried out with absolute precision. Our guided option has the job of making operators fit for the quickest possible assignment on the line.”
Superordinate line control
The individual machine conversions are coordinated and synchronized by the superordinate Innoline Flex Control line management system. This is the machinery’s communicative backbone that establishes a link between the filling system and the customer’s ERP. “Strictly speaking, this is nothing more than a MES extension with line conversion functions,” says Hanau. Part of this comprises the KHS Innoline MDI OM interface that automatically initiates the line for the next product type when a predefined number of bottles has been reached, for example. It enables order and material handling, including starting and stopping orders, through a website integrated on the HMI. “And so that our customers don’t need to compromise on flexibility at all, the KHS control system is of course also compatible with third-party systems,” the KHS project manager concludes.
For more information go to:
https://www.khs.com/en/media/trade-shows-and-events/drinktec-2022
Subscribe to our newsletter at: http://www.khs.com/en/media/publications/newsletter.html
[1] Overall equipment efficiency (OEE) is a key figure for measuring the productivity of technical systems or machines.
[2] Non-returnable PET line with an InnoPET TriBlock stretch blow molder/labeler/filler block and two operators.
[3] Depending on the products.
The KHS Group is one of the world’s leading manufacturers of filling and packaging systems for the beverage and liquid food industries. Besides the parent company (KHS GmbH) the group includes various subsidiaries outside Germany, with production sites in Ahmedabad (India), Waukesha (USA), Zinacantepec (Mexico), São Paulo (Brazil) and Kunshan (China). It also operates numerous sales and service centers worldwide. KHS manufactures modern filling and packaging systems for the high-capacity range at its headquarters in Dortmund, Germany, and at its factories in Bad Kreuznach, Kleve, Worms and Hamburg. The KHS Group is a wholly owned subsidiary of the SDAX-listed Salzgitter AG corporation. In 2021 the KHS Group and its 4,954 employees achieved a turnover of around €1.245 billion.
KHS GmbH
Juchostr. 20
44143 Dortmund
Telefon: +49 (231) 569-0
Telefax: +49 (231) 569-1541
http://www.khs.com
Presse- und Öffentlichkeitsarbeit
Telefon: +49 (251) 625561-243
E-Mail: deppe@sputnik-agentur.de

