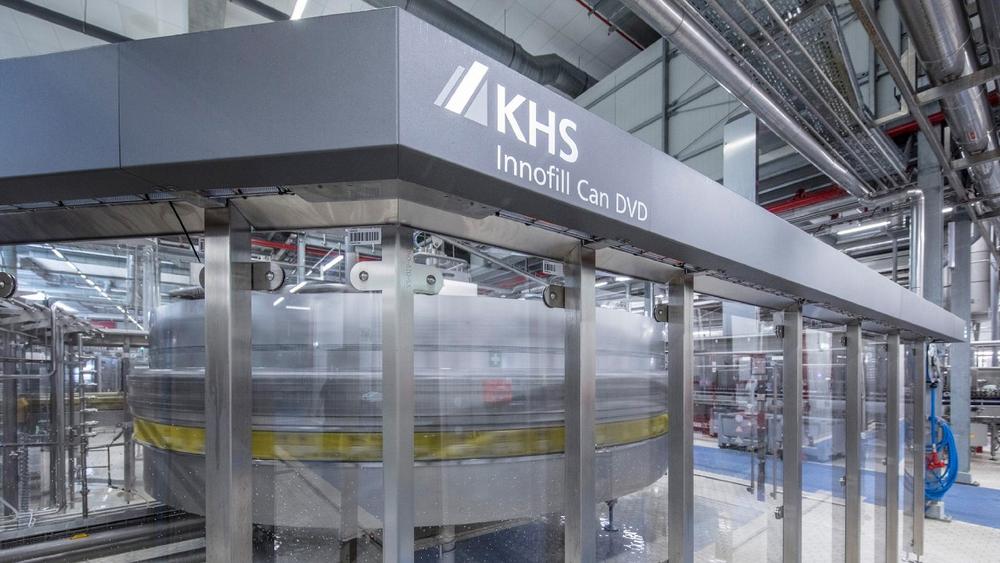
Paulaner and KHS: successful partnership through effective service contracts
Every beverage producer aims to operate its production line as efficiently as possible. To this end, its plant engineering must run smoothly and reliably. Ideally, unplanned machine stops that interrupt the filling process should be prevented to avoid any potential consequential costs or damage. For production loss has a detrimental effect on the overall performance, pushes consumption values up, lowers the efficiency of resources and narrows the profits.
To counter this, lines must be subjected to regular and – in the best case – predictive maintenance. “Compared to conventional, reactive service that only comes into play in the event of a specific failure, with preventive service productivity can be increased by up to 4%,” explains Miriam Seilkopf, the person responsible for service contracts at KHS.
The Dortmund systems supplier offers various service modules that cater for the different requirements of its customers and can be configured as packages. “The various components can be individually combined here so that our customers benefit from precisely those services that are relevant to them, coupled with maximum cost transparency,” Seilkopf continues. Even if all combinations are theoretically possible, KHS recommends its three Basic, Advanced and Comfort service packages that follow on from one another.
Fast relief
The Basic package focuses on providing fast relief as and when needed: the 24/7 HelpDesk and ReDiS, for example, are two tools that help to keep unplanned downtime as brief as possible. On the hotline experts are available round the clock to provide technical support and answer any questions on spare parts. With their expertise they help to remedy faults in an uncomplicated process – and without delay wherever possible. ReDiS, KHS’ remote diagnostic service, permits quick and precise online problem identification through remote diagnosis of customer lines and machines. It also enables components to be installed and commissioned, software configurations to be optimized and updates to be installed.
One example of preventive rather than reactive maintenance in the Basic package are inspections: KHS service engineers log the current state of the equipment using machine-specific checklists and thus identify the spare and wear parts needed in good time. If there is an inordinate amount of wear, they analyze the cause of this and make suitable suggestions as to where and how the system can be optimized. The coaching module helps to secure the best possible line operation: an extensive transfer of knowledge from KHS engineers to the operating personnel is ensured by training on the job.
Regular overhauls
In the Advanced package, in addition to inspections overhauls are included. On the one hand, these have a positive impact on the state of the machinery, with wear parts detected during inspection being replaced. On the other, regular overhauls have a preventive function. The system is restarted as soon as all maintenance work has been completed. By way of supplement to the coaching module in the Basic package, at a refresher workshop training units are revised and processes optimized or faults analyzed together with the customer according to requirements.
Above and beyond the actual replacements made during overhauls, the Advanced package can include the wear parts themselves plus consumables. The former are delivered punctually depending on the operating hours and current state of the machine.
Best possible performance
Finally, with the highest-level Comfort package beverage producers secure themselves long-term machine or line efficiency and the best-possible performance and predictability. This is ensured by embedded engineers, for instance: experienced KHS specialists who are permanently assigned to the customer’s site for the entire term of the contract. Besides carrying out time- and condition-based maintenance work, they make suggestions for improvement in daily maintenance tasks and format changeovers, support operating personnel during fault analysis and troubleshooting or show where there is potential for optimization in day-to-day operation. One of the key requirements for minimum downtime is the maximum availability of spare parts: based on KHS’ years of experience, the recommended spare parts list (RSPL) makes sure that all critical spare parts are available on site; the exact scope thereof can of course be agreed individually with the plant operator.
Individuality is generally writ large when it comes to KHS service contracts, Seilkopf emphasizes. “Even if a customer has opted for a specific service package, he or she can of course book additional services if needed. Bottlers’ requirements also increase as the level of complexity grows.”
One good example of an individual partnership such as the above is the cooperation with the new Paulaner Brewery built to the west of Munich in 2015. KHS has six lines in operation here: there are three returnable glass lines, one of which is for swing-top bottles, with a respective maximum capacity of 50,000 bottles per hour. They all feature various compelling packaging options from six packs through cartons to crates. There is also a non-returnable glass line for export products, a keg line for up to 1,000 kegs an hour and a canning line, originally for a total of 30,000 containers per hour. In 2021 the latter was replaced by a new, much more powerful line processing up to 90,000 cans per hour.
Transfer of knowledge
“When we moved from our former site on Nockherberg to Langwied, we were well aware that we wouldn’t just step off the truck and everything would carry on of its own accord,” Rainer Kansy remembers. Kansy is head of Operational Technology at the Paulaner Brewery Group and responsible for investments, maintenance, engineering, energy supply and disposal and manages a team of around 60 flexibly organized employees. “During commissioning, at the time we went for an all-inclusive service contract with an initial term of five years that was then extended for a further two years. We wanted to have a partner at our side who would ramp up the new systems with us and bring them up to speed.” The core of the agreement was year-round support including annual overhauls and all spare parts – from KHS, including the third-party equipment supplied in conjunction with the lines. This also encompassed the on-site presence of service engineers – a total of ten people during the initial launch phase, then five following the successful production start and ultimately three. “During this time our intensive exchange of knowledge with KHS proved extremely successful,” Kansy says. “In particular, this included planning annual overhauls of the big, critical units. When you realize that all together our lines total over 100 single machines, you can imagine what a complicated task this is. With large components such as the bottle washer it sometimes takes a week for everything to be taken apart and put back together again. Precise schedules need to be drawn up – sometimes for an entire line, sometimes just for a single machine – that are exactly coordinated with our production plans and take up as little time as possible, always designed to best suit the situation on hand.”
New service agreement
The exchange of knowledge to date has covered lots of different training topics and measures for improvement jointly developed by Paulaner and KHS, one of the latter being to optimize the respective degrees of efficiency. “Together we monitored our spare parts to ascertain which were really needed and which not,” states Kansy. “But now, after seven years, we’ve reached a point where our engineers need to continue on their own to become even better.”
For this reason, in 2022 the brewery again sat down with KHS to negotiate a new service agreement suitable for the current state of its operations. In the future Paulaner will thus manage without the year-round support of service engineers on site. However, there will still be a KHS coordinator who will act as an interface between the brewery group and the Dortmund engineering company’s five German production sites. This person will perform coordination and administrative tasks on the brewery premises. First and foremost, these include spare parts management, for which KHS maintains a consignment warehouse – less than 200 meters from the filling lines. “Given the size of our company, the warehouse is just as essential as having a direct contact on site,” Kansy believes. “Even if video calls are becoming more and more common, in our field of business, where everything moves very fast, they’re simply no substitute for personal contact.”
Every minute counts
A fast direct line and short distances are the be-all and end-all of this close partnership, stresses Jürgen Thielen, head of Service at KHS’ Business Center Central Europe. “You of course hope that situations such as machine downtime caused by a technical fault don’t occur,” he adds. “But if this does happen, every minute counts. “We then do all we can at KHS to help the brewery, whether this be at the weekend or in the middle of the night.” Kansy can confirm that this works very well. “It may sound a bit strange but I’m most pleased with our cooperation when we really do have a worst-case scenario on our hands and KHS can convince us in situations like these with its fast reaction and support.” Part of this support is full connection to the KHS Connect online customer portal agreed under the new service contract. It allows Paulaner to view warehouse stock and prices in real time or trigger orders.
For more information go to:
www.khs.com/en/media
https://www.khs.com/en/media/trade-shows-and-events/drinktec-2022
Subscribe to our newsletter at: http://www.khs.com/en/media/publications/newsletter.html
The KHS Group is one of the world’s leading manufacturers of filling and packaging systems for the beverage and liquid food industries. Besides the parent company (KHS GmbH) the group includes various subsidiaries outside Germany, with production sites in Ahmedabad (India), Waukesha (USA), Zinacantepec (Mexico), São Paulo (Brazil) and Kunshan (China). It also operates numerous sales and service centers worldwide. KHS manufactures modern filling and packaging systems for the high-capacity range at its headquarters in Dortmund, Germany, and at its factories in Bad Kreuznach, Kleve, Worms and Hamburg. The KHS Group is a wholly owned subsidiary of the SDAX-listed Salzgitter AG corporation. In 2021 the KHS Group and its 4,954 employees achieved a turnover of around €1.245 billion.
KHS GmbH
Juchostr. 20
44143 Dortmund
Telefon: +49 (231) 569-0
Telefax: +49 (231) 569-1541
http://www.khs.com
Presse- und Öffentlichkeitsarbeit
Telefon: +49 (251) 625561-243
E-Mail: deppe@sputnik-agentur.de
