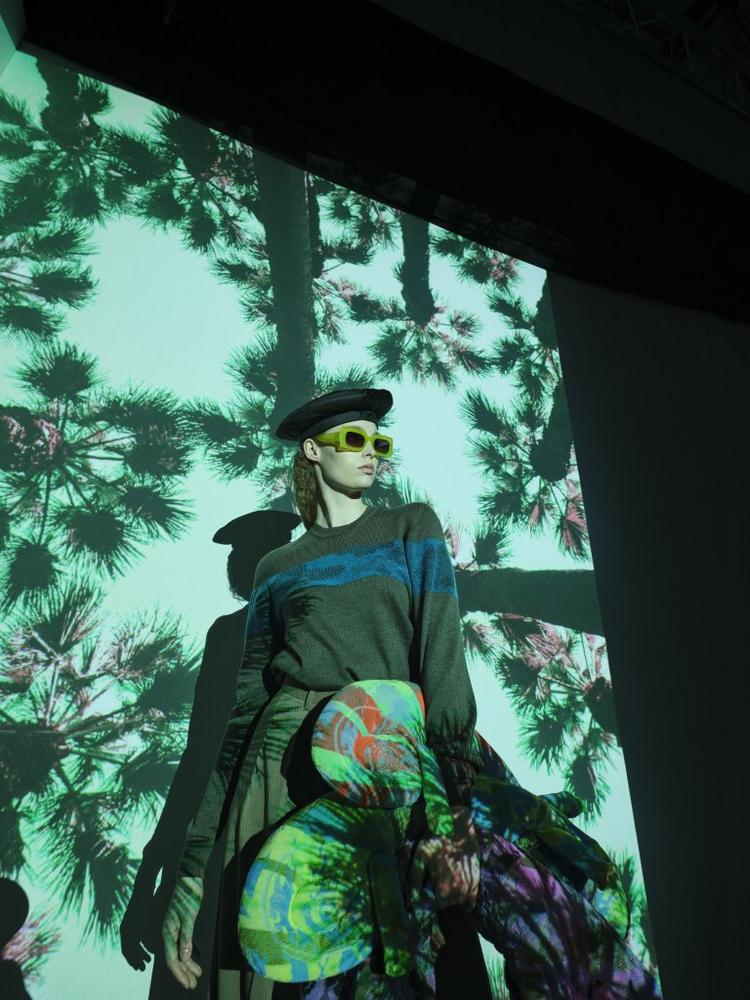
Knit and go
Adidas investigated the manufacturing potential behind digitalisation as well as customers’ needs for individualisation through its Storefactory activities. It launched at the end of 2016 and ended in March 2017. Ulrike Schlenker from KARL MAYER Corporate Communication wanted to know how the market and production technology for 3D knitted fabrics for immediate use have developed since then, so she asked an expert: Michael Händel, Vice President Sales & Service at KARL MAYER STOLL Textilmaschinenfabrik GmbH.
US: What is the current technology like in STOLL knitting machines used for the automated production of 3D flat knitted articles?
MH: Generally speaking, STOLL flat knitting machines can produce any 3D knitted fabric, and every modern STOLL flat knitting machine can be used for process automation. All the latest generation models have interfaces for using automation software through which they can be integrated into the complete workflow, from design creation to the finished product – all developed in-house by STOLL. STOLL offers autocreate® for the simple definition of workflows. Whether different pattern variations, sets of different sizes or customised on-demand articles, STOLL autocreate® allows for the creation of knit patterns in fully automatic sequences without manual intervention. The data required for this is imported via open interfaces from other programs or physical data storage. STOLL has developed CREATE PLUS to convert all design data into a final knitting program for the machine.
CREATE PLUS and autocreate® make every latest-generation STOLL flat knitting machine an indispensable automation module for 3D flat knitting production.
US: The Knit-For-You project focused on 3D knitwear for the fashion sector. Where and how are STOLL machines used today for 3D knitting?
MH: 3D knitted fabrics and STOLL flat knitting machines are used for clothing as well as in the technical textiles sector.
Knit-and-wear articles along with seamless and close-to-skin designs are especially in demand in the fashion segment. Our current WONDERFUL trend collection has great examples of this. The manufacturers produce exclusive designer pieces, which is where the impressive design possibilities of 3D flat knitting really come into their own. They also produce standard goods, such as seamless knitted sweaters, which can be produced in only a few process steps and at low cost. Low material waste also offers advantages in terms of sustainability.
These same advantages come into play in the technical textiles sector when it comes to the production of articles for the automotive, sports, furniture and medical segments.
Examples include form-knitted covers for upholstered furniture and car seats, 3D bandages and orthoses, and even sports shoes. This allows for significant streamlining of processes, especially in the footwear sector, as demonstrated by a project carried out in conjunction with DESMA: the complete shoe upper was produced in a single piece on a STOLL knitting machine. All that remained was for the sole to be moulded onto the product.
US: What are the major locations in Europe for the production of 3D flat knitwear?
MH: The real hub for 3D flat knitted fabrics is Italy, where they mainly produce exclusive articles for the fashion industry. Germany also enjoys a long tradition in this area, with other major 3D flat knitting locations to be found in Poland and France, and a number of prominent, specialised industry players in Switzerland and Austria.
KARL MAYER Holding SE & Co. KG
Industriestraße 1
63179 Obertshausen
Telefon: +49 (6104) 402-0
Telefax: +49 (6104) 402-600
http://www.karlmayer.com
media contact
Telefon: +49 (6104) 402-274
Fax: +49 (6104) 40273274
E-Mail: ulrike.schlenker@karlmayer.com

