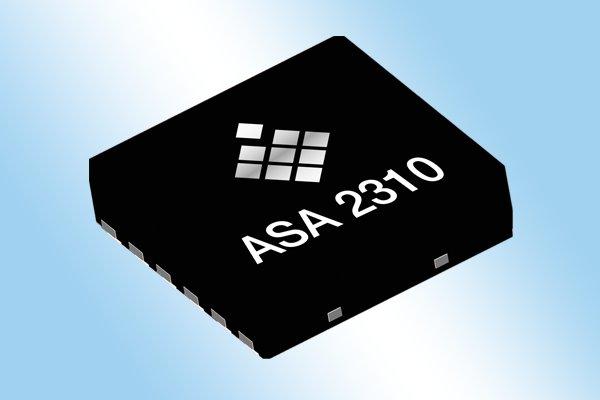
TDK introduces high-speed TMR front-end IC for demanding EV motor control applications
– The new TMR analog front-end ASA 2310 offers signal conditioning optimized for TMR-bridge angle sensors including enhanced applicative compensation features and safety supervision
– Rotor position sensing solutions based on the ASA 2310 with its high-robust output buffer offer easy-to-use differential or single-ended SIN/COS outputs for remote sensing applications with best-in-class EMC performance
– Rotor position sensing solutions based on analog TMR sensors of the TAS family and the ASA 2310 provide smaller and more flexible sensor systems compared to inductive resolvers
TDK Corporation (TSE:6762) complements the existing TMR sensor portfolio with the new Micronas signal-conditioning integrated circuit (IC) ASA 2310 for high-speed automotive and industrial electric motor applications. ASA 2310 is a low-drift, low-noise, customer-programmable TMR front-end IC with differential or single-ended SIN/COS inputs and analog outputs. Samples of ASA 2310 are now available. The start of production is planned for the end of 2023.
The ASA 2310 is designed to interface the high-precision analog TMR sensors of the TAS family. The sensors, powered and monitored by the ASA 2310, are detecting magnetic-field direction in x-y plane, and providing a SIN/COS analog voltage output which is used as input for the ASA 2310. The sensor interface and signal conditioning of the ASA 2310 are optimized for the TMR-Bridge signals. Major characteristics like gain, offset, (absolute) 0-angle, and orthogonality can be adjusted using the integrated signal path by programming the non-volatile memory of the ASA 2310. The different coarse gain settings ensure that the device can support various TMR full- and half-bridges from TDK. The amplified single or differential ended output signals of the ASA 2310 can be used to calculate the rotation angle of a magnet with very high accuracy by an external A/D-converter and an electronic control unit (ECU).
New rotor position sensing solutions based on the ASA 2310 offer a high resolution and accurate position measurement at very high rotation speeds of up to 650,000 rpm. This enables high-speed motors to maximize torque and increase efficiency which is essential for hybrid and electric vehicles to obtain maximum range. In addition, the sensor system configuration works independently of the motor pole pair number and therefore does not require complex hardware changes, a major advantage over inductive resolver technologies. This gives more flexibility in the development of the hybrid and electric powertrains of the future.
With its overvoltage and reverse polarity protection (+/-18V) the ASA 2310 features excellent robustness against electrical challenges. Compared to off-the-shelf amplifier ICs, the ASA 2310 is more appropriate for safety-critical applications since the signal-conditioning IC simplifies the external circuitry resulting in a low FIT rate. Moreover, the total system size, BOM, and assembly process costs are reduced.
This product is defined as SEooC (Safety Element out of Context) ASIL B ready according to ISO 26262. To enable the most efficient failure localization and elimination, the ASA 2310 provides a single-point fault metric (SPFM) of more than 97% which exceeds even the standard requirements of an ASIL B classification. If ASIL decomposition is applied on the system level, the IC can be integrated in systems up to ASIL D. Besides various integrated safety monitoring of the IC itself and the external TMR-bridges, the ASA 2310 features an optional and unique fluxless self-test allowing the system to test the full signal path inside the device before the ordinary operation starts. In an application setup, the test can be used to check integrity of the whole signal path including wiring, external output capacitors and ECU. Finally, the variety of safety monitoring helps to increase diagnostic coverage and simplify the external safety supervision on the ECU side.
“The ASA 2310 is a high-performance IC that extends the functionalities of a very precise analog TMR sensor and reduces the influence of noise and parasitic components caused by remote application setups where the sensor module is separate from the ECU and connected by a long wire-harness,” says Frederik Berstecher, Product Marketing Manager for „Fast Hall & TMR“ at TDK-Micronas. “When combining it with TDK’s TMR TAS sensor family, customers can commercially scale their application setups depending on accuracy, EMC or functional safety requirements since the ASA 2310 can operate up to four TMR half-bridge sensors at the same time. Thus, rotor position sensor solutions based on the ASA 2310 can be used for a wide variety of safety-critical applications like power steering, brake boosters, or traction motors.”*
While the TMR TAS sensors are available in a wide package portfolio (single-die, dual-die), the ASA 2310 signal-conditioning IC is offered in a very compact 3 x 3 mm DFN12 SMD package. A reference evaluation board consisting of magnet design and sensor + signal conditioning chipset is available on request from TDK.
Glossary
- TMR: Tunnel Magneto-Resistance
- PMHF: Probabilistic Metric for Random Hardware Failures
- SPFM: Single-Point Fault Metric
- LFM: Latent Fault Metric
Main applications*
- Brushless DC (BLDC) and permanent-magnet synchronous motor (PMSM) commutation in a safety relevant environment with long wire-harness between sensor and ECU
- Traction motor rotor position for electric vehicles (BLDC, PMSM, PMSR,…)
- Electric power steering motor
- Replacement of resolvers
- Brake booster
- LIDAR mirror
Main features and benefits**
- Support of various TMR full- and half-bridges from TDK
- Various analog output configurations
– Differential or single-ended SIN/COS analog output signals (no demodulation necessary)
– Non-ratiometric or ratiometric analog output related to the supply voltage - Intrinsic signal conditioning with on-chip calibration and integrated safety monitoring reduce effort on ECU side
- Optimized signal conditioning for TMR signals, like output gain, offset, 0-angle and orthogonality correction
- Integrated, protected supply for the external TMR-bridges
- Fast response time and high output bandwidth for applications up to 650,000 rpm
- Operating supply voltage: 3 V to 5.5 V
- Abs. max. supply voltage: ±18 V
- Programming via the IC’s output pin. No additional programming pin required
- Low current consumption
- Optimized for automotive environments with a wide ambient temperature range from -40 °C to 160 °C and integrated protection circuitry with excellent ESD and EMC robustness
- ISO 26262 development: ASIL B ready SEooC (Metrics (PMHF, SPFM, LFM) according to ASIL C)
- Very small DFN12 3×3 mm package
Key data
Type ASA 2310 Package DFN12 (3 x 3 mm) Output formats Single-ended or differential SIN/COS analog output Angular error*** ± 0.5° or less (drift over temperature and supply variation without external compensation) Delay Time Max. 3 µs Safety ASIL B ready development according to ISO 26262 (Metrics (PMHF, SPFM, LFM) according to ASIL C)
* Any mention of target applications for our products are made without a claim for fit for purpose as this has to be checked at system level.
** All operating parameters must be validated for each customer application by customers’ technical experts.
*** Using a chip set solution from TDK.
TDK-Micronas is the center of competence for magnetic-field sensors and CMOS integration within the TDK group. TDK-Micronas has gained operational excellence for sensors and actuators production in over 25 years of in-house manufacturing. It was the first company to integrate a Hall-effect based sensor into CMOS technology in 1993. Since then, TDK-Micronas has shipped over six billion Hall sensors to the automotive and industrial market. The operational headquarters are located in Freiburg im Breisgau (Germany). Currently, TDK-Micronas employs around 1,000 people.
About TDK Corporation
TDK Corporation is a world leader in electronic solutions for the smart society based in Tokyo, Japan. Built on a foundation of material sciences mastery, TDK welcomes societal transformation by resolutely remaining at the forefront of technological evolution and deliberately “Attracting Tomorrow.” It was established in 1935 to commercialize ferrite, a key material in electronic and magnetic products. TDK‘s comprehensive, innovation-driven portfolio features passive components such as ceramic, aluminum electrolytic and film capacitors, as well as magnetics, high-frequency, and piezo and protection devices. The product spectrum also includes sensors and sensor systems such as temperature and pressure, magnetic, and MEMS sensors. In addition, TDK provides power supplies and energy devices, magnetic heads and more. These products are marketed under the product brands TDK, EPCOS, InvenSense, Micronas, Tronics and TDK-Lambda. TDK focuses on demanding markets in automotive, industrial and consumer electronics, and information and communication technology. The company has a network of design and manufacturing locations and sales offices in Asia, Europe, and in North and South America. In fiscal 2022, TDK posted total sales of USD 15.6 billion and employed about 117,000 people worldwide.
Micronas
Hans-Bunte-Strasse 19
79108 Freiburg
Telefon: +49 (761) 517-0
Telefax: +49 (761) 517-2174
http://www.micronas.com
Public Relations Manager
Telefon: +49 (761) 517-2531
E-Mail: julia.andris@micronas.com