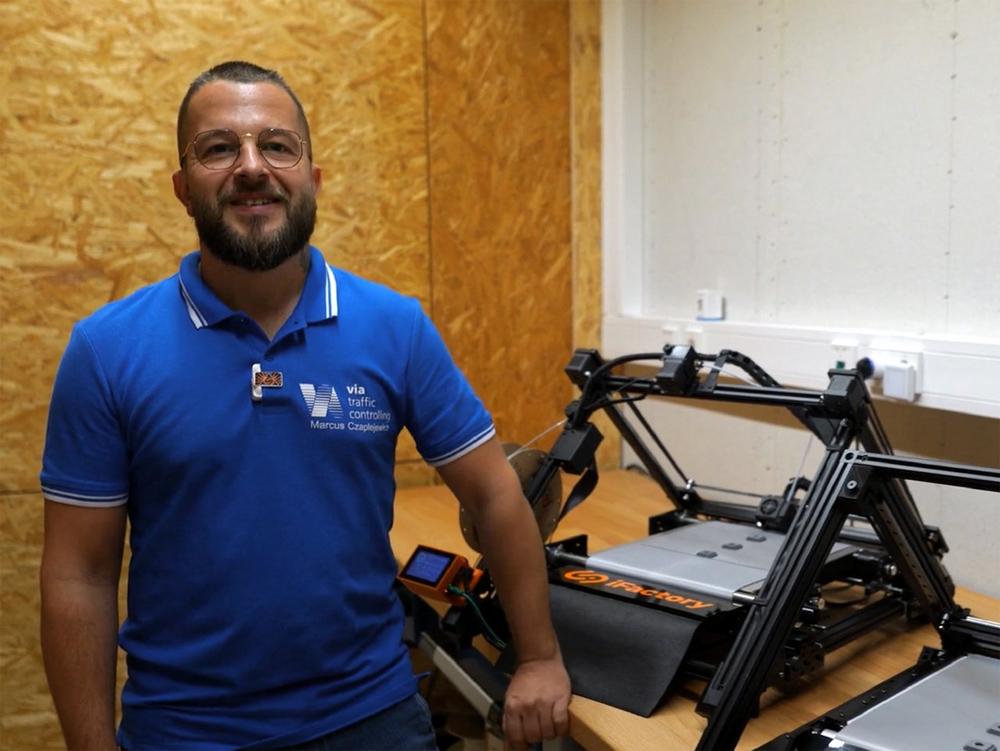
Profitable serial printing
via traffic controlling GmbH is an international supplier of speed display panels, traffic counting devices and radar detectors. In order to be able to implement prototype development promptly and flexibly itself and produce components in high volumes at low cost, the company opted for a belt printer from the Düsseldorf-based startup iFactory3D, currently the only B2B company in the world to develop 3D belt printers. These are particularly attractive for industries that work on a large scale, where they are especially suitable for prototyping and the production of spare parts.
The belt printer works around the clock and was purchased for precisely this reason. A production series can be started – even with different objects thanks to the queue function – and runs for days without having to be supervised. This means that via traffic controlling can react flexibly to demand and receive the required items in the shortest possible time without having to pre-produce. Another advantage is that the printer can be loaded with particularly large filament spools and automatically pauses printing when the filament runs out. After refilling, the printer starts up seamlessly so that no material is lost.
Advanced technology
The special feature of the 3D printers from the German company iFactory3D is the generous build volume: "Infinite" x 280 x 170 mm. In addition, the exchangeable hotend is angled at 45 degrees to largely eliminate the need for support structures in overhangs during the printing process. This means that also hollow structures can be produced additively, which offers new possibilities for subsequent modification with fillers, or produces particularly lightweight components. This saves material, but also effective printing time and manual post-processing, since no support has to be laboriously removed from the actual printed part. With external dimensions of 620 x 540 x 380mm, the printer fits comfortably on any workbench. With a maximum nozzle temperature of 260°C, the system can print with various thermoplastic filaments, e.g. PETG, PLA, PC, ABS etc.
Return on Investment
The 3D belt printer significantly contributes to profit optimization – in contrast to the previous system, via traffic controlling saves about 70% of the manufacturing costs of one of their best-selling products. Whereas the acquisition of a component previously cost about 15-17 € per piece, the iFactory3D printer has reduced the cost per part with accessories to about 3 €. The purchase costs had already been amortized after just under 8 weeks.
For via traffic controlling, 3D belt technology is clearly the future. Production manager Marcus Czaplejewicz states: "With a belt printer, you are no longer restricted to certain dimensions in the build space. In the past, we gave a lot of things to suppliers, who then printed prototypes for us. Such a prototype often doesn’t work right away and the adaptation then costs a lot of time. Now we can simply manufacture large parts here in-house, adapt them and tinker with them until the prototype is suitable for series production. You’re no longer limited and you can just print a lot of little things without supervision."
About iFactory3D (https://ifactory3d.com)
Founded in 2020 by Artur Steffen and Martin Huber, iFactory3D brings automated batch production to additive manufacturing. Optimizing suppliers and simplifying development processes is a real game changer in today’s world, effectively saving time, money and CO2. iFactory3D offers more and more industries the opportunity to manufacture independently and locally again and implement innovations in a timely manner. As the world of manufacturing shifts towards customization, adaptability, and local locations, agile manufacturing is becoming increasingly clear as the future of manufacturing technology. With its innovative products, iFactory3D automates additive manufacturing.
About via trafficcontrolling GmbH (https://www.viatraffic.com)
via traffic controlling GmbH, based in Leverkusen, Germany, was founded in 1991 and is an expert in traffic safety and innovative traffic technology. The company is an international supplier of speed display panels and developer of high-performance radar technology as well as traffic data acquisition including the associated software application. Whether speeding, inner-city traffic calming or automatic traffic counting, via traffic controlling designs and develops individual solutions for different road traffic requirements – in Europe, North and South America, Africa and Asia. Customers include companies such as Adam Opel AG, Airbus, Bayer Healthcare, Miele, RWE Systems, but also cities and municipalities, private initiatives, associations, ports, airports and other private or public institutions.
iFactory3D automates additive manufacturing through its cutting-edge technology – 3D belt printing.
Founded in 2020 by Artur Steffen and Martin Huber, the company is working on an industrial revolution to make additive manufacturing competitive with mass production in terms of automation and scale, without losing the clear benefits of 3D printing: Flexible and individualized production on demand, resulting in less waste. In addition, it eliminates long transportation routes and complicated supply chains with specialized manufacturing processes in Asia.
iFactory3D brings series production back to the customer – local supply with maximum independence for producers.
iFactory3D stands for innovation & productivity, for reliability & flexibility, and sees itself as an enabler: With the practically unlimited possibilities of a 3D belt printer, barriers can be easily overcome, and more groundbreaking ideas have the chance to be implemented economically and efficiently.
iFactory3D GmbH
Wanheimer Str. 43
40472 Düsseldorf
Telefon: 021115859748
http://ifactory3d.com/
Krug Communications Ltd
Telefon: +44 (7740) 245-867
E-Mail: andrea@krugcomms.com

