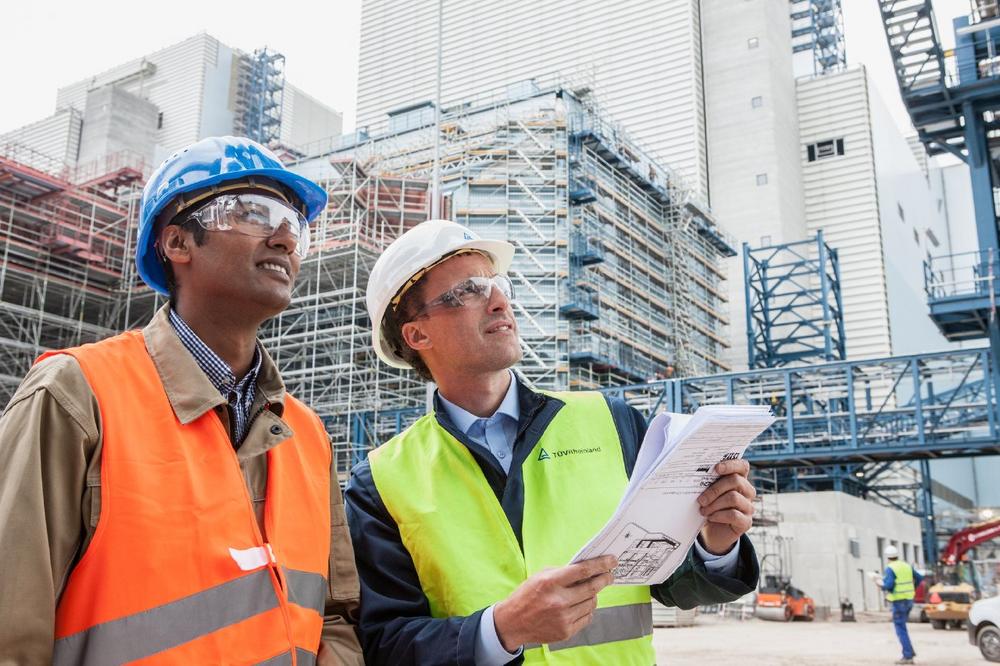
TÜV Rheinland: Fewer accidents thanks to sustainable safety culture
Winning the hearts and minds of the workforce
Behavior-based safety (BBS) looks at the employee behaviour and identifies the root causes to behaviour, which is often a result of workforce attitudes to, and perceptions of, the organization’s safety message. ”A common factor for bypassing safety rules is time pressure: For example, employees don’t take the time to get a ladder, but instead climb on their office chair to get something from the top of a cabinet,” explains George Bradley. If this unsafe behaviour is paired with praise for the speedy completion of the task, this unsafe behavior is reinforced and might be copied by other co-workers. The aggregate of habits shapes a company’s safety culture.
Managers and employees share the responsibility
”A sustainable improvement in the safety culture means replacing bad habits with good ones. Managers play an important role in this process, because they act as role models and represent the corporate philosophy,” stresses Bradley. Managers should therefore always comply with the applicable occupational safety rules, even – or especially – under time pressure. In addition, they must effectively lead good safety practices with employees in a motivating, rather than accusatory manner. "Positive reinforcement instead of blame is a core element of effectively leading a sustainable safety culture,” says Bradley.
Specially trained TÜV Rheinland industrial and organizational psychology experts train managers to improve their communication skills and leadership ability in this domain. However, a sustainable safety culture is not a top-down strategy. Instead, it should encourage all employees to become actively involved.
Wanted: Professional implementation with a 360° view
Behavior-based occupational safety leads to significant safety culture improvements and consequently to a sustainable return on investment. Expertise in all aspects of occupational safety and a profound understanding of the interactions between technology, organization and people are essential prerequisites. “Our experts tailor the measures to be taken individually to a specific company while making sure to include already existing tools. Behavior-based occupational safety is not a one-off intervention with an immediate effect, but rather a process," explains occupational safety expert George Bradley.
In the field of sustainable safety culture, TÜV Rheinland cooperates exclusively with SeaChange. The Irish company specializes in behavior-based occupational safety and has already achieved an average accident reduction of up to 50 percent in a wide range of client companies using this methodical and evidence-based approach.
At www.tuv.com/safetyculture there is detailed information on sustainable safety culture as well as case studies.
Sicherheit und Qualität in fast allen Wirtschafts- und Lebensbereichen: Dafür steht TÜV Rheinland. Das Unternehmen ist seit mehr als 150 Jahren tätig und zählt zu den weltweit führenden Prüfdienstleistern. TÜV Rheinland hat mehr als 20.000 Mitarbeiterinnen und Mitarbeiter in über 50 Ländern und erzielt einen Jahresumsatz von rund 2,1 Milliarden Euro. Die hoch qualifizierten Expertinnen und Experten von TÜV Rheinland prüfen rund um den Globus technische Anlagen und Produkte, begleiten Innnovationen in Technik und Wirtschaft, trainieren Menschen in zahlreichen Berufen und zertifizieren Managementsysteme nach internationalen Standards. Damit sorgen die unabhängigen Fachleute für Vertrauen entlang globaler Warenströme und Wertschöpfungsketten. Seit 2006 ist TÜV Rheinland Mitglied im Global Compact der Vereinten Nationen für mehr Nachhaltigkeit und gegen Korruption. Website: www.tuv.com
TÜV Rheinland
Am Grauen Stein
51105 Köln
Telefon: +49 (221) 806-2148
http://www.tuv.com
Senior Communication Manager
Telefon: +49 (221) 806-5210
E-Mail: Alexander.Schneider@de.tuv.com
