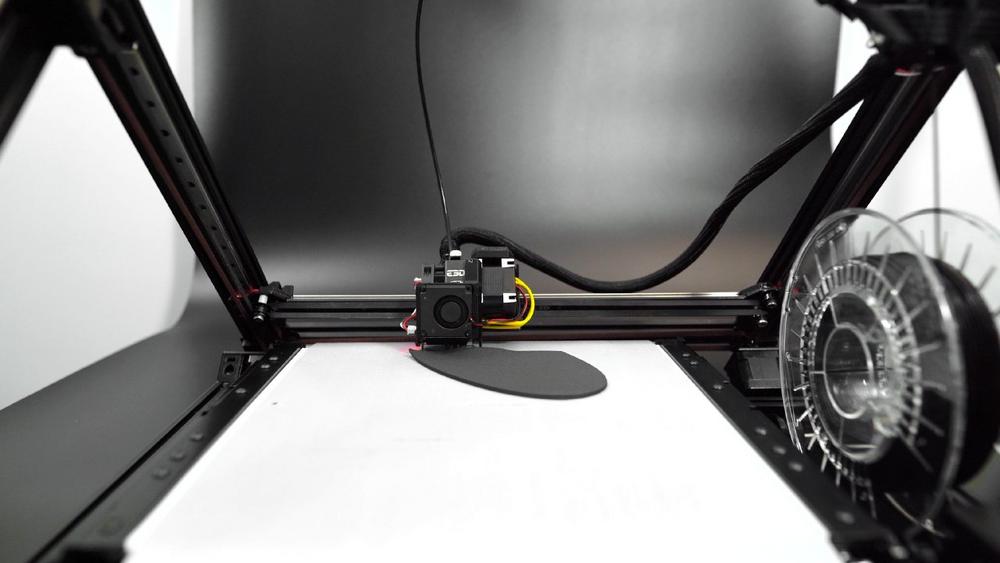
Bachelor thesis confirms financial viability of 3D belt printers compared to Cartesian 3D printers
The bachelor’s thesis "Economic viability and applicability of 3D belt printers for serial production in manufacturing companies"[1], which was submitted to the Industrial Engineering and Management WIM degree programme at Düsseldorf University of Applied Sciences in August 2022, analyses the economic viability and profitability of 3D belt printers compared to typical Cartesian 3D printers.
Based on five sample objects to be implemented (a ring, a motor angle, a housing, an insole and a cable duct), an economic efficiency calculation was carried out to determine the machine hour rate. It was found that the variable costs for the 3D belt printer (iFactory3D One Pro) were lower in each case than for the regular 3D printer (Ultimaker S3 / S5). Using the 3D belt printer, all five parts could be produced at a lower unit price. That’s because, due to the 45° printing angle, less material is required for 3D belt printing, and complex geometries can be printed without support structures. Another advantage of the 3D belt printer is the unrestricted length of the installation space. Where two Cartesian models had to be used to print the parts, the 3D belt printer was able to handle all selected component dimensions and produce parts in one piece, non-stop. This eliminates additional staff costs and waiting times, because the 3D belt printer can run for weeks and produce continuously.
Example cable duct: 3D belt printer reduces printing time, unit price and staff costs
For a long part like the cable duct, the high savings per part are due to the fact that with the One Pro – in contrast to the S3 or even the larger S5 from Ultimaker – the required 1.50 m could be printed continuously in one piece. Using a conveyor belt instead of a rigid and thus limited print bed means that there is no limit to the dimensions in the z-axis. For the assembly space of the S3, on the other hand, the cable duct was divided into a total of eight pieces that had to be printed in two print runs, as only four at a time can fit in the print area. Result: the printing time for the S3 is 66% longer. The required restart of the printing process adds working hours to the production costs. Overall, the unit price for the long part printed on the S3 is approx. 3.5 times higher than for the One Pro 3D belt printer.
When producing larger quantities of small printed parts, such as a ring (spacer) or motor angle, on a Cartesian printer, the objects have to be removed manually from the build plate after 50 or 30 printed parts, respectively, when the construction panel is at maximum capacity. This step is eliminated with the continuously running 3D belt printer, which in turn saves staff costs. Due to the savings in variable costs, in any comparison, the One Pro always reaches a point where the total production costs with it are cheaper. With the Ultimaker S3, the total fixed costs are around 9% lower, which matches the small price difference in acquisition costs. However, thanks to lower operating costs – both for staff and electricity – and lower material consumption, the use of the belt printer always pays off sooner or later, depending on the part.
Artur Steffen, CEO of iFactory3D, said: "Due to the automation associated with it, a 3D belt printer can significantly reduce manufacturing costs and compete with injection moulding technology. So, for SMEs and individual entrepreneurs, using 3D printing technology in batch production is worthwhile. iFactory3D brings automated serial production to additive manufacturing."
Contact for more information and interview requests:
Andrea Krug, Krug Communications Ltd, Tel. +44 (0)7740 245 867, Mail: andrea@krugcomms.com
Artur Steffen, CEO, iFactory3D, Mail: artur.steffen@ifactory3d.com
About iFactory3D (https://ifactory3d.com/en/)
Founded in 2020 by Artur Steffen and Martin Huber, iFactory3D is a young 3D technology company and currently the only B2B company in the world developing 3D belt printers. Optimising suppliers and simplifying development processes is a real game changer in today’s world, effectively saving time, money and CO2. iFactory3D offers more and more industries the opportunity to manufacture independently and locally again and to implement innovations in a timely manner. As the world of manufacturing shifts towards customisation, adaptability and local locations, agile manufacturing is becoming more and more clearly the future of manufacturing technology. With its innovative products, iFactory3D automates additive manufacturing.
[1] Original title: „Wirtschaftlichkeit und Anwendbarkeit von 3D-Fließbanddruckern in der Serienproduktion in produzierenden Unternehmen“
iFactory3D automates additive manufacturing through its cutting-edge technology – 3D belt printing.
Founded in 2020 by Artur Steffen and Martin Huber, the company is working on an industrial revolution to make additive manufacturing competitive with mass production in terms of automation and scale, without losing the clear benefits of 3D printing: Flexible and individualized production on demand, resulting in less waste. In addition, it eliminates long transportation routes and complicated supply chains with specialized manufacturing processes in Asia.
iFactory3D brings series production back to the customer – local supply with maximum independence for producers.
iFactory3D stands for innovation & productivity, for reliability & flexibility, and sees itself as an enabler: With the practically unlimited possibilities of a 3D belt printer, barriers can be easily overcome, and more groundbreaking ideas have the chance to be implemented economically and efficiently.
iFactory3D GmbH
Wanheimer Str. 43
40472 Düsseldorf
Telefon: 021115859748
http://ifactory3d.com/
Communication & Social Media Marketing Coordinator
Telefon: 021115856575
E-Mail: corinna.marmetschke@ifactory3d.com

