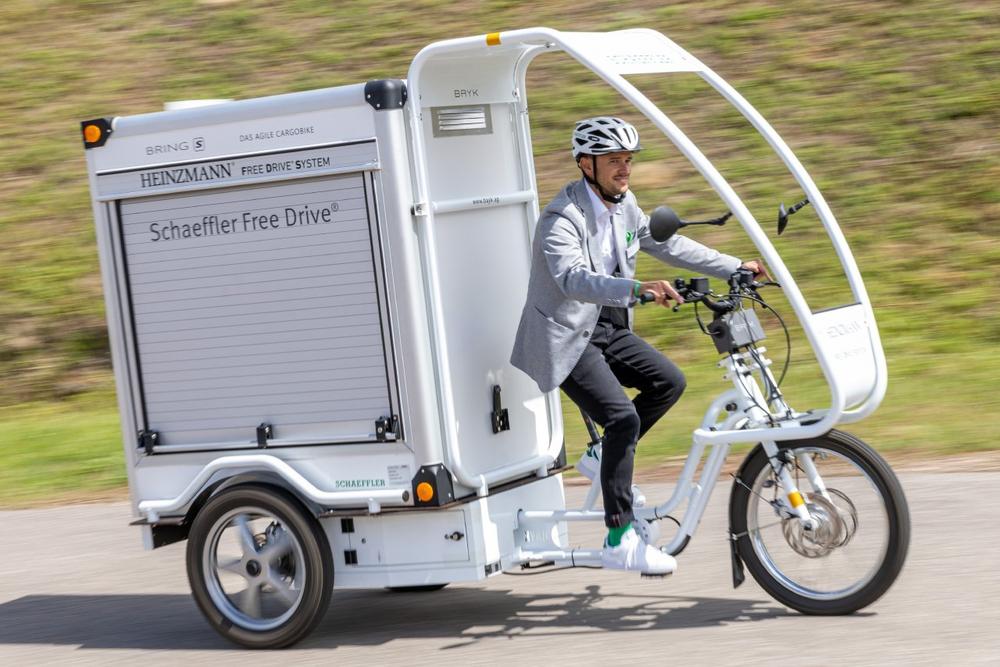
Fleet start for Schaeffler’s chainless drive for e-cargo bikes
- Schaeffler supplies first customer fleets with drive systems for electric cargo bikes
- A drive especially developed for electric cargo and utility bikes for inner-city goods transportation
- Innovative bike-by-wire concept opens the way for new business models in urban micromobility
Electric cargo and utility bikes are becoming an increasingly common sight in big cities, where they are the ideal solution for speedy, climate-friendly transportation and distribution of food, mail, medicine and more. To help with this trend, Schaeffler has been partnering with two-wheeler electric drive specialist Heinzmann GmbH & Co. KG to develop an innovative chainless drive system called Free Drive. Now, the first customer fleets using this drive hit the roads in urban traffic. “We need to rethink mobility for tomorrow’s cities,” said Matthias Zink, CEO Automotive Technologies at Schaeffler AG. “Electric cargo bikes fill an important gap here, particularly in last-mile goods delivery.” Schaeffler sees this as a growth market. In 2021, the global electric cargo bike market was valued at USD 630 million, nine percent up on the prior year, and is projected to grow to USD 2.14 billion by 2032 (source: Persistence Market Research).
Schaeffler and Heinzmann first unveiled its innovative chainless drive system to the public in August 2021, and have been using the time since then to get it ready for fleet production. Following successful field testing during the last month, production is now getting underway, with plans to steadily increase capacity over the next few years. The first customer to put in an order for the Free Drive, which boasts highly efficient power transmission from pedal to wheel, is CIP Mobility GmbH. CIP’s mocci Smart Pedal Vehicles set new standards in efficient, low-maintenance and sustainable commercial-sector mobility in cities and industrial zones. Developed as an innovative micromobility platform, the mocci cargo bikes break with many established conventions in the bicycle industry, combining smart hardware with intelligent software and cutting-edge materials. “The partnership between Schaeffler and CIP leverages innovative power and performance to strengthen Germany’s position as an R&D and production location,” said CIP co-founder Dimitrios Bachadakis.
No chain, no wear
The Free Drive is an optimally matched system that consists of a pedal generator, drive motor, customer-specific battery solution, and human-machine interface (HMI). It’s sold by Heinzmann to bicycle manufacturers and fleet operators. Core component of the system is its pedal generator developed by Schaeffler. It produces constant pedal resistance and provides electricity for the motor in the rear-wheel hub. It is designed in such a way that pushing the pedals requires significantly less muscle power than with conventional e-bike drives – a major benefit for cargo bike riders, especially on long delivery routes. Surplus electrical energy is stored in the bike’s battery for later use. In this way, the Free Drive can deliver a total drive output of 250 watt.
One of the key benefits of this serial hybrid drive for bikes is that it has no chain, belt, gear rings, sprockets, or other mechanical drive components, so it is much less prone to mechanical wear than conventional e-bikes. “With the Free Drive, replacing worn-out drive chains is a thing of the past,” said Dr. Jochen Schröder, Head of Schaeffler’s E-Mobility business division. This robust design cuts down on maintenance, which is a major plus for operators of cargo bike fleets as their assets will spend more time on the road and less time in the repair shop. Meanwhile, riders will appreciate not having to worry about getting chain lubricant on their clothing.
More freedom of design thanks to electric power transmission
While the architecture of conventional e-bike drives is largely dictated by the need for a mechanical connection between the pedals and the motor, the Free Drive – as its name suggests – allows considerable freedom of design. “The chainless drive system opens up completely new possibilities in bike architecture and pedal configuration – including designs with two, three or four wheels, with or without a roof”, Jochen Schröder explained. The digital bike-by-wire concept also means that gear shifts and changes between operating modes are performed by software. To make this possible, all components of the system sold by Heinzmann communicate with each other via a CAN connection.
mocci goes with Free Drive
The Smart Pedal Vehicles by mocci are an innovative and sustainable solution for companies seeking to make their urban operations flexible, fast, and eco-friendly. Thanks to the Free Drive system, they also offer a completely new riding experience that is customizable, safe, and fully connected. Another innovative feature is that mocci’s structural components, e.g frames, wheels and forks frames, are made of recyclable, high-performance plastics rather than steel or aluminum. Compared to a classic spoke wheel the front and rear wheels consist of a single structural component, which makes them less vulnerable. The frame is made using a scalable injection molding process that emits about 68 percent less CO2 than processes used to produce conventional aluminum frames. “In 2023, we will supply vehicles to a wide range of B2B customers – which means we will have a decisive impact on the shape of inner-city mobility,” said CIP co-founder Dimitrios Bachadakis.
As a leading global supplier to the automotive and industrial sectors, the Schaeffler Group has been driving forward groundbreaking developments in the fields of motion and mobility for more than 75 years. With innovative technologies, products, and services in the fields of CO₂-efficient drives, electric mobility, Industry 4.0, digitalization, and renewable energies, the company is a reliable partner for making motion and mobility more efficient, intelligent, and sustainable. The technology company manufactures high-precision components and systems for powertrain and chassis applications as well as rolling and plain bearing solutions for a large number of industrial applications. The Schaeffler Group generated sales of approximately EUR 13.9 billion in 2021. With around 83,000 employees, Schaeffler is one of the world’s largest family companies. With more than 1,800 patent applications in 2021, Schaeffler is Germany’s second most innovative company according to the DPMA (German Patent and Trademark Office).
Schaeffler AG
Industriestraße 1-3
91074 Herzogenaurach
Telefon: +49 (9132) 82-0
Telefax: +49 (9132) 82-3584
http://www.schaeffler-group.com
Telefon: +49 (7223) 94136-36
E-Mail: annett.fischer@schaeffler.com