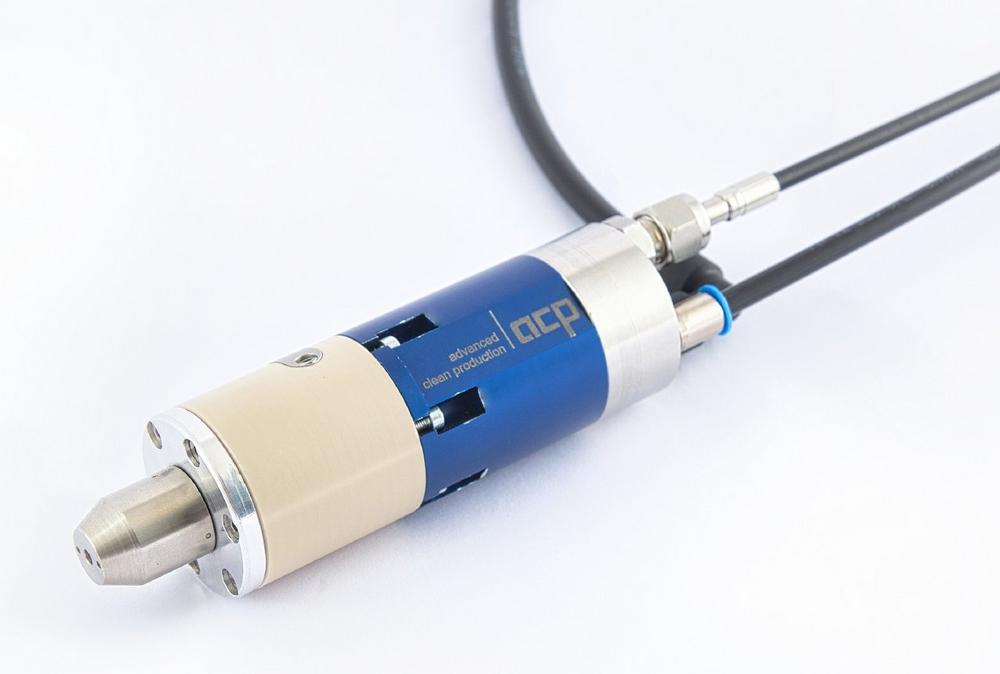
Improved cleaning performance and lower media consumption
For some time now, the trend in industrial parts cleaning has been towards dry processes that are capable of removing particulate and filmic contamination reliably and, if necessary, selectively. There is also a growing demand for integrating such processes into production lines in a simple and space-saving way. The quattroClean snow jet technology from acp systems AG, which uses liquid, climate-neutral carbon dioxide as a cleaning medium, meets all these requirements.
Pulsed nozzle saves operating costs
To extend the range of application of the cost-effective and sustainable cleaning process, the company has designed an innovative two-substance ring nozzle that generates a pulsed jet. The wear-free nozzle is equipped with a valve specially developed by acp for this purpose which enables pulse times as fast as 20 milliseconds. In contrast with pilot-operated standard valves, the direct control of the valve prevents icing and thus ensures reliable operation and consistently superior results. The jet and pause times can be set independently of each other, so that the pulses can be optimally adapted to the respective application and also to the part-specific cleaning sequence. At the same time, the pulsed jet reduces CO2 and compressed air consumption. Depending on the pulse time, savings between 10 and 15 percent can be achieved. At the inaugural FiT2clean Awards 2022, where the Fachverband industrielle Teilereinigung e.V. (FiT) annually honors outstanding achievements and solutions for parts cleaning, acp systems‘ innovation won third place.
New applications in cleaning, deburring and machining
The pulsed jet of CO2 and compressed air has a higher kinetic energy than a continuous jet, making it slightly abrasive. This opens up potential applications where conventional CO2 snow jet cleaning previously had to pass. These include, for example, removing loosely adhering welding beads after welding processes and cleaning off particulate contamination adhering to metallic components due to dried-on process media. The pulsed nozzle also has its advantages when it comes to cleaning off flux residues and particles from bonding surfaces.
It can also be deployed to remove partial film residues after hot stamping or laminating aluminum onto plastic parts. In addition, the pulsed jet of CO2 and compressed air has sufficient cleaning power to remove fine burrs from aluminum and zinc die castings. Furthermore, the technology can be used to simultaneously deburr and clean hard and brittle plastics such as PEEK and PPS. When machining these plastic and aluminum parts, the new two-substance ring nozzle also offers optimization potential. If used as an alternative to conventional cooling lubricants, the cold snow crystals made of carbon dioxide ensure a higher metal removal rate, thus improving productivity and reducing tool wear. The workpieces and machine also stay cleaner.
Four mechanisms of action guarantee excellent results
The wear-free two-substance ring nozzle is the “heart” of the process. Liquid carbon dioxide is fed through it and expands on exiting to form fine snow crystals. These are then bundled by a separate jacket jet of compressed air and accelerated to supersonic speed. When the easy-to-focus jet impacts on the surface to be cleaned or deburred, a combination of thermal, mechanical, solvent and sublimation effects takes place. The interaction of these four mechanisms of action reliably removes particulate and filmic contamination as well as fine burrs. The detached contaminants or burrs are carried away from the part by the aerodynamic force of the jet of compressed air and removed from the process chamber by an integrated extraction system. Since CO2 sublimates at atmospheric pressure, the parts are immediately dry and can be further processed straightaway. When the quattroClean snow jet technology is used in machining applications, the chips generated are both clean and dry, making them easy to recycle.
The scalable quattroClean process can be adapted to different component geometries for partial or full-surface cleaning in a space-saving and efficient manner. Process parameters are determined via trials in the company’s own technical center. Based on standard modules, the cleaning systems are designed to match the cleaning task and cycle time specified by the customer. The company builds stand-alone systems as well as solutions for integration into automated and/or interlinked production lines.
acp systems AG, 71254 Ditzingen, Germany, Phone +49 7156 480140,
Based in Germany, acp systems AG is a global technology leader in advanced clean production, related process automation and systems integration. Core technologies include quattroClean snow jet cleaning, microdosing and intelligent handling solutions for flexible materials and foils. The company’s patented quattroClean technology is a dry, gentle and resource-saving process, which removes particulate and filmic contamination from almost any technical material. It is also suitable for cleaning electronic and electromechanical components with reproducible results. The scalable quattroClean system can be used for full-surface or partial cleaning, e.g. to selectively clean welding, bonding, and sealing surfaces. Since 1997, acp systems AG assists its customers in developing, planning and integrating highly automated production processes, especially in the electronics, medical and automotive industries. (www.acp-systems.com).
acp systems AG
Berblingerstr. 8
71254 Ditzingen
Telefon: +49 (7156) 48014-0
Telefax: +49 (7156) 48014-10
http://www.acp-systems.com
Public Relations
Telefon: +49 (711) 854085
