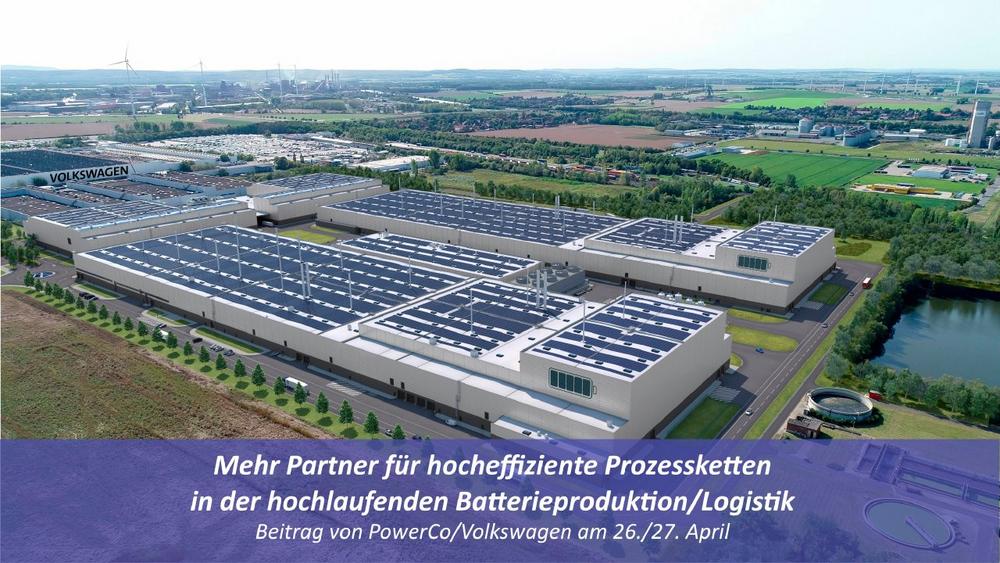
Batterieproduktion/Logistik 2024+ | Anspruch und Umsetzung in der Automobilindustrie
Tatsache ist, dass sich aus den Antriebsvarianten auch neue Komponenten für den Antriebsstrang ergeben und dies von Grundstoffen, Zellen, Montagekomponenten bis hin zum Thermomanagement und zur Steuerung im gesamten Einbauraum und Netzwerk.
Aber wer soll diese Komponenten bereitstellen? Wie kann die Wettbewerbsfähigkeit hier bei den Komponenten und über die ganze Lieferkette abgesichert werden, wenn die europäische Autoindustrie hier gerade erst durchstartet, besteht hier doch noch eine große Lücke gegenüber den Herstellern und Zulieferern in Fernost, die bereits vor mehreren Jahren mit größeren Volumina begonnen haben.
Über das Produkt-Know-How eines batterieelektrischen Antriebes mit allen Komponenten hinaus, ist das Management der Lieferketten für die Batterieproduktion und -logistik von besonderer Bedeutung. Das beginnt bei den Einzel- und Modul-Komponenten mit den hierfür relevanten Versorgungsketten, dann weiter mit den hierfür erforderlichen Verpackungs-/ Transporteinheiten bis hin zu einer gut überlegten und synchronisierten Prozesskette bis zum Einbau und im späteren Verlauf dann auch über die Stationen einer möglichen Wiederverwendung und eine möglichst nachhaltige Entsorgung.
Die Planung, der Aufbau der Fabriken und Liefernetze sowie die Operations globaler Produktions- und Logistiknetzwerke wird so über das Produkt-Know-How hinaus, deutlich anspruchsvoller.
Um die bisherige Wettbewerbsposition zu behaupten und weiter auszubauen, werden durchaus auch neue Partner gesucht und integriert. Partner, die in der Lage sind, Teilprozesse der Komponentenherstellung, der Batterieproduktion, der Versorgung, der Entsorgung und Wiederaufbaus eigenständig oder im Netzwerkbetreiben und dabei produkt- und prozessnahe Innovationen für die gesamte Produkt- und Prozesskette bereitstellen.
Deutlich wird der Anspruch un die Kompetenz auch im Beitrag von PowerCo/Volkswagen, die den neuen Weg zur Weiterentwicklung in eine anspruchsvolle Antriebswelt auch über den eigenen Konzern hinaus vorantreibt.
PowerCo/Volkswagen – Sarah Süß, Leiterin Customer Logistics & Operations Logistics, Salzgitter und Thorsten Raettig, Leiter Inbound Operations Logistics, Salzgitter
Logistik hocheffizienter Prozessketten im Netzwerk der Batterieproduktion – Herangehensweise und Umsetzung von der Standortplanung bis zur Umsetzung im Liefernetzwerk
Im Juli 2022 wurde in Salzgitter der Grundstein für die neue Batteriefabrik gelegt. Anlässlich der Grundsteinlegung stellte der Konzern erstmals das Konzept der Standardfabrik vor: Salzgitter soll Blaupause für Zellfabriken in ganz Europa sein und neue Maßstäbe für Nachhaltigkeit und Innovation setzen.
„Was wir mit Fahrzeug-Plattformen wie MQB und MEB millionenfach bewiesen haben, legen wir auch dem Aufbau der Zellwerke zugrunde: Wir standardisieren auf Basis europäischer Normen und skalieren. Das ermöglicht Tempo und Kostenoptimierung bei höchster Qualität“, erklärt PowerCo CEO Frank Blome.
Beim Thermomanagement arbeitet Volkswagen an komplett neuen Lösungen. Wo heute eine Vielzahl von Einzelmodulen und langen Schlauchverbindungen zum Einsatz kommen, übernimmt dies künftig ein extrem kompaktes, integriertes Thermo-Modul. Es steuert die gesamte Klimatisierung einschließlich der Hochvoltbatterie und hat damit großen Einfluss auf Reichweite sowie Schnellladefähigkeit des Fahrzeugs. Das neue All-in-One-Modul ist dabei deutlich leichter, robuster und effizienter als heutige Systeme.
Batterie-Module haben ein erhebliches Gewicht und an den Transport werden hohe Sicherheitsanforderungen gestellt (Gefahrgut). Der Pulswechselrichter ist das Gehirn des elektrischen Antriebsstrangs und maßgeblich verantwortlich für Effizienz und Performance. Dank des Baukastenprinzips kann damit künftig die gesamte Bandbreite vom Einstiegsmotor bis zum Sportwagen mit 500 kW und mehr Leistung realisiert werden. Die Technologie wird aktuell zur Serienreife entwickelt und kann bereits mit der nächsten MEB-Generation zum Einsatz kommen.
Wie die Transformation für eine der Supply Chain mit all den dabei relevanten Innovationen und Vorgehensweisen insgesamt erfolgreich gelingen kann und welche Lösungen hier jetzt schon erfolgreich eingeführt/eingesetzt werden, wollen wir beim nächsten Automobilkongress am 26./27. April 2023 in Saarbrücken in Vorträgen, Werksbesuchen und Workshops diskutieren (www.automobilkongress.de).
Der Jahreskongress des AKJ-Automotive beschäftigt sich deshalb am 26./27. April mit den Themen, die sich auf der Grundlage der erkennbar neuen Herausforderungen für die Produktion und Logistik mit den jetzt relevanten Konzepten und Möglichkeiten auseinandersetzen.
Ergänzt werden die Beiträge durch Werksbesuche bei Bosch Homburg, Nobilia Saarlouis und Schaeffler Homburg sowie durch Workshops nach den Vorträgen zur Batterielogistik/Produktion und CO₂-Rechnung/Grüne Logistik.
Den Automobilkongress des AKJ mit dem inhaltlichen Motto
AUFBRUCH – Strategien und Wege für eine nachhaltige Weiterentwicklung –
Transformation im Markt, im Produkt, in der Fabrik und der Supply Chain.
Die beteiligten Unternehmen/Personen an den Vorträgen, Moderationen, Werksbesuchen, Workshops und Diskussionen: BMW, Bosch, CLAAS, Daimler Truck, Dräxlmaier Group, Fordwerke, ISW/Universität Stuttgart, HFT Stuttgart, Hörmann Automotive, htwsaar, IPL Prof. Schmidt, Magna Steyr, NGK Spark Plug Europe, NIO Europe, PwC, REHAU Automotive, Rhenus Automotive, Schaeffler Technologies, Schaltbau, SMR Automotive Global, Volkswagen/PowerCo, Wirtschaftsministerium des Saarlandes.
Vertieft wird der Erfahrungsaustausch mit den Teilnehmern, Referenten, Moderatoren und Ausstellern nach den Vorträgen noch einmal zusätzlich in der Abendveranstaltung, den Pausen, in den digitalen „Innovation-Pitches“ sowie in den getrennt mit den Ausstellern und den Interessenten vereinbarten Digital-Räumen.
Falls Sie selbst nicht teilnehmen können, würden wir uns freuen, wenn Sie prüfen könnten, ob ggf. auch andere Vertreter Ihres Unternehmens Interesse an
- den Vorträgen am 26. April und der Netzwerkveranstaltung am Abend
- der begleitenden Ausstellung am 26./27. April mit neuen Fallbeispielen
- den geplanten 3 „Benchmarking-Live-Besuchen“ bei Bosch in Homburg, Schaeffler in Homburg und dem neuen Nobilia-Produktionswerk
- oder den 2 Workshops „A Batterieproduktion und Logistik“, „B – CO2-Rechnung und Logistik“ nach den Vorträgen am Nachmittag des 27. April 2023 und den damit zusammenhängenden Gespräche haben.
Einige der Beiträge werden wir gemeinsam mit dem diesjährigen Montagekongress des ZeMA einbringen. Hinzu kommen weitere Beiträge in den Sessions des Montagekongresses, der ebenfalls am 26. und 27. April in Saarbrücken durchgeführt wird.
AKJ Automotive c/o FITT gGmbH
Saaruferstraße 16
66117 Saarbrücken
Telefon: +49 (681) 95431-0
Telefax: +49 (681) 95431-99
http://www.akjnet.de
Projektleiter
Telefon: +49 (681) 9543112
Fax: +49 (681) 9543199
E-Mail: joerg.kuntz@akjnet.de
Institutsleiter
Telefon: +49 (681) 954310
Fax: +49 (681) 5867425
E-Mail: kjschmidt@iplnet.de

