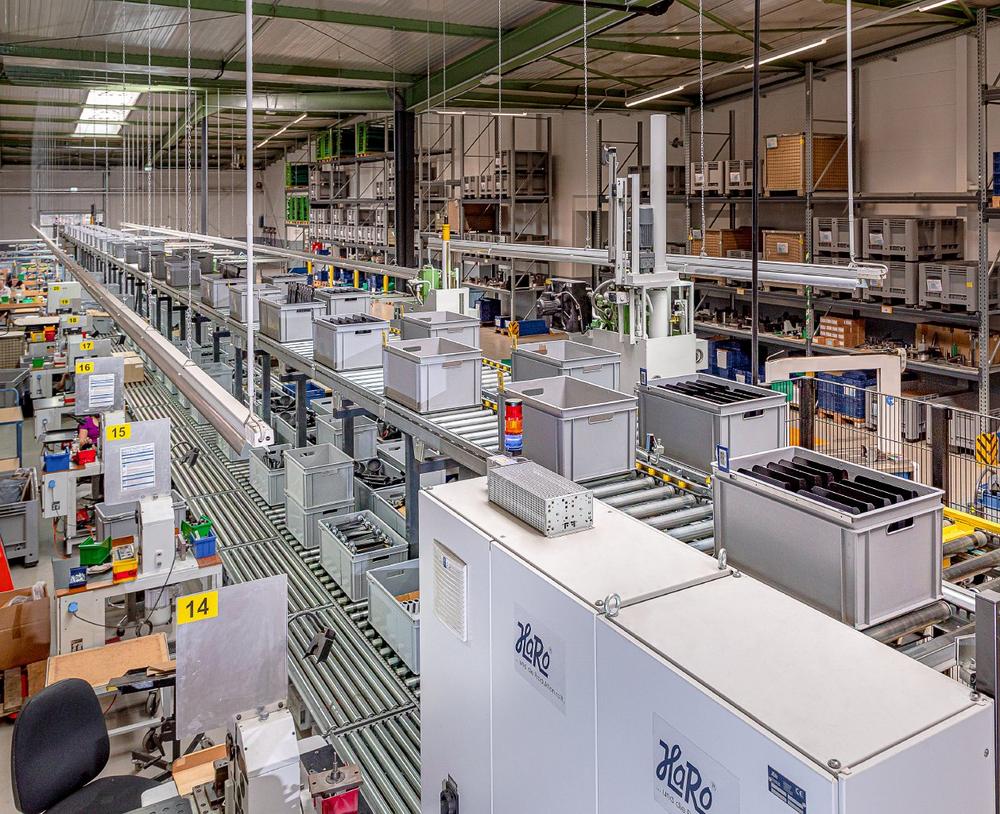
Kombination aus Montagelinie, Kommissionieranlage und Pufferstrecke
Die steigende Nachfrage nach Musikzubehör führte bald nicht nur zur Einstellung weiterer Mitarbeiter, sondern auch zur Entwicklung einer breiten Produktpalette – Mikrofonstative, Keyboard- und Gitarrenständer, Musikerstühle, Zubehör für mobile Geräte und seit 2020 auch Produkte für den Gesundheitsschutz sind nur eine Auswahl der Produkte, die das Familienunternehmen bis heute in seinem Portfolio hat.
Wachsende Produktpaletten erfordern auch wachsende Produktionsflächen, die in den vergangenen sieben Jahrzehnten ebenfalls stetig erweitert wurden und mittlerweile eine Fläche von über 5.000 Quadratmetern umfassen. Grund genug für die Werkstrukturplanung um Tilman Seubert, die internen Abläufe neu zu planen. In seiner Anfrage an die HaRo Anlagen- und Fördertechnik GmbH konnte er die Anforderungen konkret definieren: Auf zwei Förderbändern sollten die Fertigprodukte in der Produktionshalle künftig von den Mitarbeitern montiert und kommissioniert werden. Zusätzlich sollten die Transportbänder mit Rollenbahnen ausgestattet werden, die das Abstellen der Fördergüter für die Montage ermöglichen. Mit Blick auf eine zukunftsorientierte Anlage stellte das Familienunternehmen zudem die Anforderung, die Transportbänder so auszulegen, dass zu einem späteren Zeitpunkt eine zweite und dritte Linie über die neue Anlage installiert werden kann.
Für diese Anforderungen entwickelte die HaRo-Gruppe schließlich ein Konzept, das die richtigen Impulse setzen konnte. Markus Löseke, Konstruktionsleiter der HaRo-Gruppe, erläutert die Besonderheiten der neuen Anlage bei König & Meyer:
„Wir haben für unseren Kunden zwei identische Förderstrecken über zwei Ebenen entwickelt, die einen kontinuierlichen Prozess ermöglichen. Angetriebene Rollenbahnen transportieren das Fördergut jeweils über eine Strecke von rund 40 Metern. Zusätzlich befinden sich am Ende der Förderstrecke 28 Ausschleuser, über die die Ladungsträger für die Montagelinie ausgeschleust werden können."
Ist eine Charge fertiggestellt, wird sie wieder auf die angetriebene Rollenbahn zurückgeschoben und durchläuft den Kreislauf bis zur Entnahme für die Verpackung. Sollten einzelne Chargen auf der unteren Ebene nicht freigegeben werden, können die betroffenen Ladungsträger auf der zweiten Ebene gepuffert werden. Dies geschieht über eine App-Steuerung auf dem Tablet, die mit einem Scanner verbunden ist und die gekennzeichneten Behälter über den zweistufigen Vertikalförderer in die nächste Ebene befördert.
„Auf die gleiche Weise kommen die Behälter auch wieder in die erste Etage zurück, wenn die Chargenfreigabe erfolgt ist“, erklärt Markus Löseke.
Auch die Ladungsträger weisen eine Besonderheit auf, insnsgesamt vier verschiedene Größen sind im Produktionsprozess bei König & Meyer im Einsatz, teilweise mit einer Länge von bis zu 1,5 Metern. Kleine Umlenkrollen an den Aufgabestellen sorgen neben den angetriebenen Stahlstützrollen dafür, dass die Behälter trotz der uneinheitlichen Größen auf den Rollenbahnen zentriert werden.
Für die geforderte Kreisbewegung der Behälter wurde am Anfang und am Ende der Förderstrecken jeweils eine Pusher-Einheit installiert, die genügend Kraft aufbringen kann, um den voll beladenen Behälter quer zur Förderrichtung auf die gegenüberliegende Rollenbahn zu schieben.
Ein Konzept, das die Anforderungen des Musikzubehörherstellers überzeugte. Nicht nur, dass die neue, doppelstöckige und damit platzsparende Anlage einen kontinuierlichen und automatisierten Materialfluss ermöglicht, die HaRo-Förderanlagen sind als Baukastensystem jederzeit flexibel erweiterbar. Ein Vorteil, den sich König & Meyer bereits zunutze gemacht hat und auch bei seinem jüngsten Projekt auf das Know-how der HaRo-Gruppe setzte. So wurde nur ein Jahr später eine weitere Förderanlage installiert, um die Produktionshalle mit der neu errichteten Lagerhalle für den Palettentransport zu verbinden.
Realisiert wurde dieses Projekt mit einer bewährten Brückenlösung der HaRo-Gruppe, die neben angetriebenen Rollenbahnen und Kettenförderern auch zwei Vertikalförderer beinhaltet. In der Produktionshalle erfolgt der Palettenumschlag sowohl von Rollenbahn zu Rollenbahn als auch von Kettenförderer zu Rollenbahn. Angetriebene Rollenbahnen ermöglichen einen automatisierten und störungsfreien Transport innerhalb der Brückenstrecke. Darüber hinaus dient die Strecke auch in diesem Projekt als Puffermöglichkeit, um kurzfristige Produktionsspitzen abzufedern. Auf der Lagerseite wurde eine robuste Abnahmestation für die versandfertigen Paletten installiert, die dann mittels Gabelstapler an ihren Bestimmungsort transportiert werden.
Umgekehrt können aus dem neuen Lager auch Transportgüter an die Anlage übergeben und über den Senkrechtförderer und die Rollenbahnen in die Produktionshalle transportiert werden. Dieser Reversierbetrieb ermöglicht eine effektive Auslastung der Anlage ohne zusätzlichen Aufwand.
HaRo Anlagen- und Fördertechnik ist Hersteller von Förderanlagen für den innerbetrieblichen Materialfluss und automatisierte Lagerlogistik.
Als eine entscheidende Schnittstelle der Industrie 4.0 ist der automatisierte Transport von Waren, Paletten, Stückgütern, Halbzeugen und Versandartikeln ein breites Anwendungsportfolio für ein ebenso weitläufiges Kundenspektrum.
Sowohl horizontal als auch vertikal ist die HaRo Fördertechnik im In- und Ausland für Ihre Qualität bekannt. Von den Rollenbahnen über die Kettenförderer, bis hin zu den Vertikalförderer und Puffersystemen wird ein breites Spektrum an Möglichkeiten abgedeckt. Grundlage dafür ist ein ausgereifter Modul-Baukasten und die 60 jährige Erfahrung im Bereich der Fördertechnik.
Ein Höchstmaß an Flexibilität für individuelle Kundenanfragen wird gewährleistet, ob neue Anlage oder die Modernisierung einer bereits bestehenden kann jederzeit umgesetzt werden. Die Lagerplatzoptimierung und die einhergehende Effizienzsteigerung der Fertigungs- und Produktionsketten steht klar im Fokus.
Bauliche Hürden, z.B. die Überwindung mehrere Etagen oder der Transport über eine vierspurige Bundesstraße hinweg, stellen eine willkommene Herausforderung dar.
Die Hauseigene Fertigung, Lackiererei und elektrotechnische Fachabteilung für Schaltschrankbau und Programmierung sind ein weiteres Qualitätsmerkmal für die Fertigungstiefe und Know-How am Standort Rüthen.
Mittels der eigenen LKW-Flotte gelangt die fertige Anlage final zum Kunden und wird dort von HaRo-Personal fachgerecht montiert und in Betrieb genommen.
Das 1957 von Heinz Hackländer gegründete Familienunternehmen, mit seinem Ursprung in Wermelskirchen steht seit 1986 unter der Leitung von Christoph Hackländer.
Die Übergabe an die dritte Generation ist für die nächsten Jahre fest eingeplant und sichert somit den Fortbestand des Familienunternehmens am Standort Rüthen.
Bei HaRo bekommen sie alles aus einer Hand.
HaRo Anlagen- und Fördertechnik GmbH
Industriestr. 30
59602 Rüthen
Telefon: 02952 8170
Telefax: 02952 81730
https://www.haro-gruppe.de
Innendienst Leitung
Telefon: +49 (2952) 817-35
Fax: +49 (2952) 817-30
E-Mail: ne@haro-gruppe.de