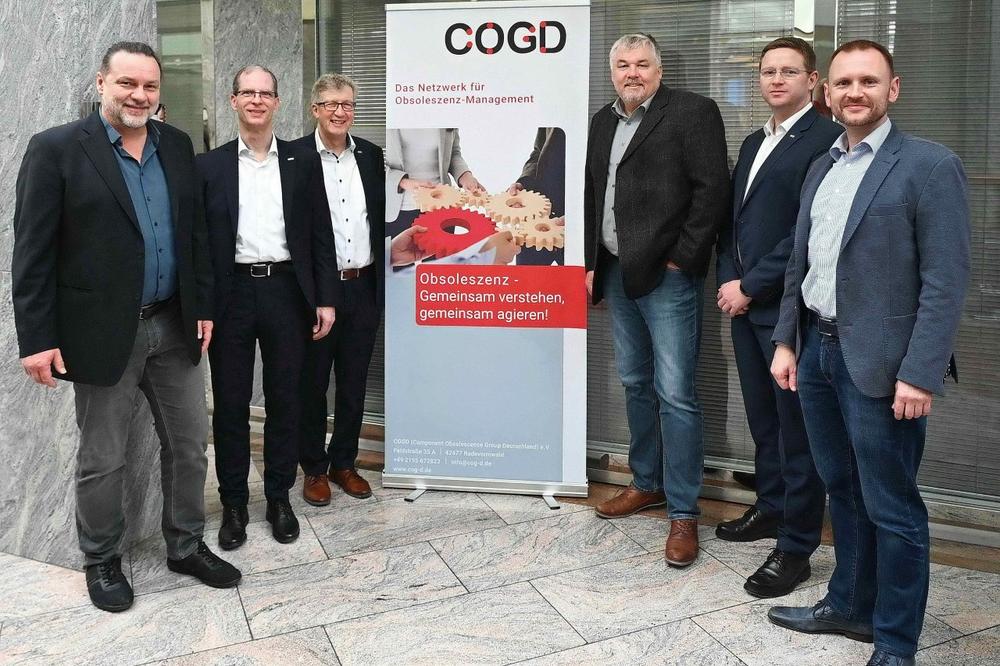
Newly elected COGD board sees further increase in obsolescence risks
This is a development that the non-profit industry organization COGD (Component Obsolescence Group Deutschland) e.V. is following with great concern. For 18 years, the 163 member companies of the industry organization have been jointly developing strategies and measures to minimize or at least curb the often very expensive effects of obsolescence. With success, as evidenced by the initiative launched by COGD to internationalize the smartPCN standard into IEC 62402, the SCIP cooperation with the law firm ReachLaw, and the cooperation with other important trade associations such as the FED, among others. Nevertheless, the recently elected eight-member board with its new chairman Axel Wagner (Legal Manager, Prettl Electronics Automotive), his deputy Joachim Tosberg (Lifecycle Manager, RAFI Group), treasurer Oliver Hoffmann (Director EMEA, SiliconExpert Technologies), Dr. Wolfgang Heinbach (Partner, Syliom Management Consulting ), Tim Kohlen (Business Development Manager DACH, America II Europe), Stefanie Kölbl (Division Manager TQ-Embedded, TQ-Systems), Frank Mützner (After Series Manager, Plastic Omnium Lighting Systems) and Dieter Paatsch (Electronic Components Management, Festo) have to meet a lot of challenges.
Quite a few manufacturers from sectors such as automotive, aerospace, military, rail, power plant, medical and automation technology, who often need spare parts for their equipment and systems for decades, had actually considered themselves to be in a good position in terms of supply security until the start of the Corona pandemic, but the last three years with their many disruptive factors acting in parallel on the global supply chains have taught quite a few of these companies better. However, the new COGD Chairman Axel Wagner also sees opportunities in the late realization that in our networked world, materials and components required for production and maintenance are not always available in sufficient quantities at all times: "Unfortunately, some mistakes and omissions of the past only become apparent in times of crisis. This is not necessarily tragic, as long as you learn from them. Unfortunately, the sum of potential disruptive factors has never been as high as it is today. Particularly in a country like Germany, which is poor in raw materials and is currently completely dependent on foreign suppliers in many areas, it should have long been standard practice to continuously check all suppliers and supply chains for potential risks of failure and to take appropriate active and reactive precautionary measures. Unfortunately, this is still not the case. I assume that in just a few years, hardly any industrial company will be able to get by without strategic obsolescence management. But until then, we as an industry association still have a lot of education and support work to do."
Deputy COGD Chairman Joachim Tosberg also emphasizes the increasing importance of comprehensive strategic obsolescence management for manufacturing companies. Obsolescence is not only caused by the discontinuation of electronic components, but increasingly also by a lack of raw materials and semi-finished products. Further trouble is threatened by stricter environmental laws and regulations such as REACH. It is not only the supply of the SCIP database with a vast amount of product data that proves to be problematic in practice or often impossible for correct implementation. The supply chain law and the digital product passport are already the next challenges, and their impact on supply security also needs to be examined intensively. Another cause for concern is the increasing shortage of qualified employees, the brain drain of know-how, e.g. for reasons of age, outdated software components that are no longer maintained and, above all, the issue of cyber security. Tosberg’s conclusion: "In view of these increasing potential obsolescence risks, it is now necessary to take preventive action quickly and more consistently than ever before, to develop forward-looking concepts that also ensure the availability of the required resources at all company levels in the long term."
COGD offers affected companies and individuals extensive support for this purpose. In addition to quarterly meetings with specialist presentations, reports from working groups and discussion groups, a variety of other platforms are available for the direct and indirect exchange of information on all aspects of obsolescence prevention and management. For example, at this year’s in-house exhibition on July 6 at the CongressForum Frankenthal, non-members will also have the opportunity to obtain information from 22 exhibitors directly on site about their services and products for obsolescence prevention. Detailed information on the Component Obsolescence Group Deutschland e.V. can be found on the association’s website at www.cog-d.de
The COGD (Component Obsolescence Group Deutschland) e.V., a chapter of the IIOM, is an association that deals with the causes and consequences of product discontinuations and their impact on the ability to deliver. It develops ideas, concepts and tools for the proactive avoidance and efficient handling of product discontinuations once they have occurred. The focus is on pragmatic "best practice" solutions that arise from the intensive exchange of experience between the member companies. The aim is to minimise the economic follow-up costs caused by product discontinuations. Further information can be found at www.cog-d.de.
COG (Component Obsolescence Group) Deutschland e.V.
Feldstraße 35 A
42477 Radevormwald
Telefon: +49 (2195) 672823
Telefax: +49 (2195) 6771824
http://www.cog-d.de
3W Media & Marketing Consulting
Telefon: +49 (8761) 759203
E-Mail: werner.wiesmeier@3wconsulting.de

