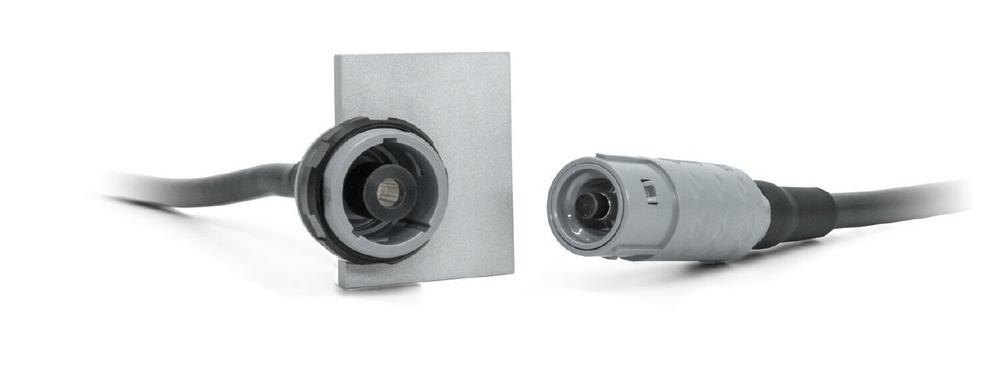
State-of-the-art technologies in use for automotive testing
Many new trends surround the future of mobility. One of these trends is e-mobility. The climate protection targets from the Paris Climate Agreement require the world’s most important industrialized countries to massively reduce greenhouse gas emissions by 2050. The transport sector is also affected by this. In addition to the performance of the vehicles, the sustainability of the drive batteries plays a decisive role.
To ensure this, vehicle manufacturers and workshops need a wide range of technology solutions for measurement technology and automotive diagnostics. In order to remove only the damaged components in the event of a partial battery defect during servicing, the defect must be identified and the new cell to be inserted must match the state of charge of the remaining cells. Battery balancing can save not only resources but also costs.
Another challenge is that automotive testing is becoming increasingly extensive and complex. Modern vehicles have a multitude of sensors and electronic systems that interact with each other and require precise tuning. Extensive testing, which also takes into account the interaction with other systems and components, ensures that these systems function correctly.
In order to meet the challenges, the use of state-of-the-art simulation and test systems in the automotive testing sector requires vibration and shock resistance in addition to high contact reliability. Therefore, component manufacturers must also ensure a robust and reliable design. In the field of plug-in connections, in addition to the high number of mating cycles, the stress in the workshop environment and optimum user-friendliness must also be taken into account.
For ODU, safe contacting in a small installation space is possible by using the MEDI-SNAP® 3.5 connector to transmit power for the HV tools used to precondition the drive batteries of electric cars. In addition to the transmission capability of power, it is possible to accommodate fluids, coax or fiber optics. Further advantages offer:
– Single Power Contact Technology for up to 100A and 1000V
– up to 41 signal contacts
– Weight savings of up to 75% due to plastic housing
The weight savings and robust design make the ODU MEDI-SNAP® ideal for use in harsh workshop environments. This makes them flexible in use and easy to handle. Each connector is uniquely pluggable due to its mechanical coding, and the up to seven different colors support the user with a better visual connection for safe and intuitive operation. Connectors from ODU support the high safety standards and user-friendliness, helps to avoid errors during application and additionally saves time and resources.
The ODU Group is one of the world’s leading suppliers of connector systems, employing 2,600 people around the world. In addition to its company headquarters in Muehldorf a. Inn (Germany), ODU also has an international distribution network and production sites in Sibiu/Romania, Shanghai/China, and Tijuana/Mexico. ODU combines all relevant areas of expertise and key technologies including design and development, machine tooling and special machine construction, injection, stamping, turning, surface technology, assembly and cable assembly. The ODU Group sells its products globally through its sales offices in China, Denmark, France, Germany, Hong Kong, Italy, Japan, Korea, Austria, Romania, Sweden, UK and the US, as well as through numerous international sales partners. ODU connectors ensure a reliable transmission of power, signals, data and media for a variety of demanding applications including medical technology, military and security, automotive, industrial electronics, and test and measurement.
ODU GmbH & Co. KG
Pregelstraße 11
84453 Mühldorf a. Inn
Telefon: +49 (8631) 6156-0
http://odu-connectors.com/de/
Produkt Marketing Spezialistin
E-Mail: tanja.stilkerich@odu.de
