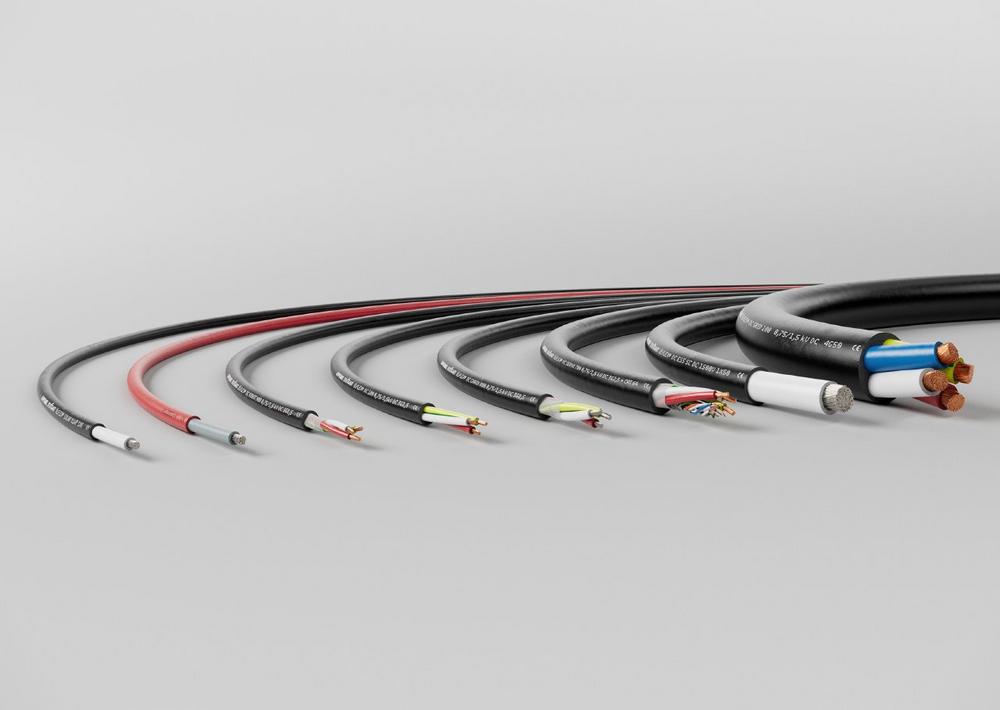
The LAPP direct current portfolio
Particularly if the source for electricity generation comes from renewable energies such as photovoltaic systems, use of direct current is particularly efficient. These energy sources produce direct current (DC), which must be converted into alternating current (AC) via inverters. On the other hand, if the end consumer is once again a digital device such as a laptop, smartphone, an LED lamp or charging station for electric vehicles or an intelligent production unit in a factory, this will require a double conversion, as these end consumers only work with direct current (DC). Huge conversion losses are incurred as a result. Even intelligent production units (e.g. speed-controlled drives or robots) in a factory often contain an internal DC intermediate circuit, for which no conversion stage is necessary with a DC supply. Experts assume that the consistent use of direct current in industry not only makes it possible to integrate renewable energy sources more easily, but also avoids conversion losses between AC and DC in the single-digit percentage range, depending on the application. In addition, the use of DC offers further advantages in terms of energy efficiency. Fewer conversion steps and fewer cores with often reduced conductor cross-sections also result in material savings and increased resource efficiency compared to AC. This means that direct current will play a key role in industrial power supply in the future.
"Sustainable energy efficiency and the rapid switch to renewable energies can only be successfully designed if we consistently switch more and more to direct current and avoid conversion losses. We need a turnaround," stresses Dr Karsten Fuchs, an engineer in the Innovation and Advanced Technology Department at Lapp Holding SE. Therefore, the global market leader for integrated solutions in the field of cable and connection technology addressed the topic of direct current at a very early stage and is active in the development of cables and wires for low-voltage direct current networks for industrial applications. Based on these findings, LAPP was the first in the world to present its DC portfolio.
These include, for example, the ÖLFLEX® DC GRID 100 – a direct current cable for energy distribution in buildings and for connecting industrial facilities. It is ideal for setting up energy-saving DC grids in industrial plants in the low-voltage range, for example for use in control systems, motors and frequency converters. The flexible, direct current cable for buried installation with colour code according to EN 60445 has good installation properties thanks to the design fine-wire, flexible design of its conductors. It can be used in dry, damp and wet environments and withstands high mechanical loads. It can be laid directly underground or can be routed openly in cable trays.
Its DC portfolio also includes the ÖLFLEX® DC 100 however with new core colour coding as per the DIN EN 60445 (VDE 0197) standard for direct current cables, which was updated in 2018. Other cables include the ÖLFLEX® DC SERVO 700 DC hybrid cable for stationary applications, the ÖLFLEX® DC CHAIN 800 made of TPE for moving applications, or the first DC robot cable ÖLFLEX® DC ROBOT 900 with core insulation made of TPE and a sheath made of PUR, as well as the halogen-free, highly flame-resistant single-core cable ÖLFLEX® DC ESS SC for DC applications up to 1.5 kV for use in energy storage systems (ESS).
However, DC cables and other components alone are far from sufficient for reliable operation. Current construction sites can be found, for example, in the norming and standardisation of DC technology. LAPP was therefore a supported partner in the research project DC industry2. In the DC Industrie2 project, the researchers and 40 partners set themselves the task of developing and testing concepts for an intelligent DC supply system. The German Federal Ministry for Economic Affairs and Climate Protection (BMWK) supported the project, which ran until March 2023. LAPP researched the long-term stability of insulation materials for DC cables and wires.
Long ago, LAPP and Ilmenau Technical University had discovered in experiments that insulation materials exhibit a different ageing behaviour in a DC field than in an AC voltage field. For example, researchers from Ilmenau Technical University loaded single cores with different insulation materials in a water bath at 80°C with 1 kV DC voltage over a period of 2,500 hours to track the effects in fast motion. The results were that some cables with PVC or halogen-free insulation were much quicker than all test pieces with TPE insulation. Further research is required in order to make more accurate statements, especially with regard to the appropriate test methodology. Nevertheless, there is no reason to omit cables with higher-quality PVC insulation in DC voltage applications.
LAPP has also been a founding member of the Open Direct Current Alliance (ODCA) since autumn 2022. This is an alliance of companies, research institutes and the ZVEI that aims at giving new impetus to DC technology. Subsequently, the ODCA is the international and practical continuation of the German direct current research projects DC-Industrie and DC-Industrie2 and, since 2016, has worked with over 40 partners from industry and research to implement the energy revolution in industrial production. It also collaborates closely with the Current/OS foundation.
The ODCA focuses on six key topics:
- Building an international DC ecosystem and establishing DC technology for many applications.
- Close collaboration between users, planners, manufacturers, suppliers, research institutions, standardisation organisations and associations.
- International dissemination of knowledge and solutions on direct current grids.
- Protection of investment through the development and establishment of an innovative and sustainable direct current system.
- Platform for designing further research projects.
- Informing and convincing politics and society about the opportunities of direct current on the way to a resource-saving, CO2-neutral world.
"DC technology will decisively change industrial production and will be used in individual infrastructure projects in future". The time is ripe for a turning point," says Jürgen Beck, Product Manager at U.I. Lapp GmbH.
Headquartered in Stuttgart, Germany, LAPP is a leading supplier of integrated solutions and branded products in the field of cable and connection technology. The company’s portfolio includes standard and highly flexible cables, industrial connectors and screw technology, customised system solutions, automation technology and robotics solutions for the intelligent factory of the future, as well as technical accessories. LAPP’s core market is in the industrial machinery and plant engineering sector. Other key markets are in the food industry, logistics, as well as the energy and the mobility sector.
The company was founded in 1959 and is still fully owned by the founding family to this day. In the 2021/22 financial year, it generated a consolidated turnover of EUR 1,864 million. LAPP (including its non-consolidated companies) currently employs approximately 5,055 people across the world, produces at 19 international sites and has over 41 sales companies. LAPP also cooperates with around 100 international offices.
U.I. Lapp GmbH
Schulze-Delitzsch-Str. 25
70565 Stuttgart
Telefon: +49 (711) 7838-01
Telefax: +49 (711) 78382640
http://www.lapp.com
Telefon: +49 (711) 7838-5702
E-Mail: ann-kathrin.hoffmann@lapp.com
Telefon: +49 (711) 7838-01
Fax: +49 (711) 7838-2640
E-Mail: irmgard.nille@in-press.de