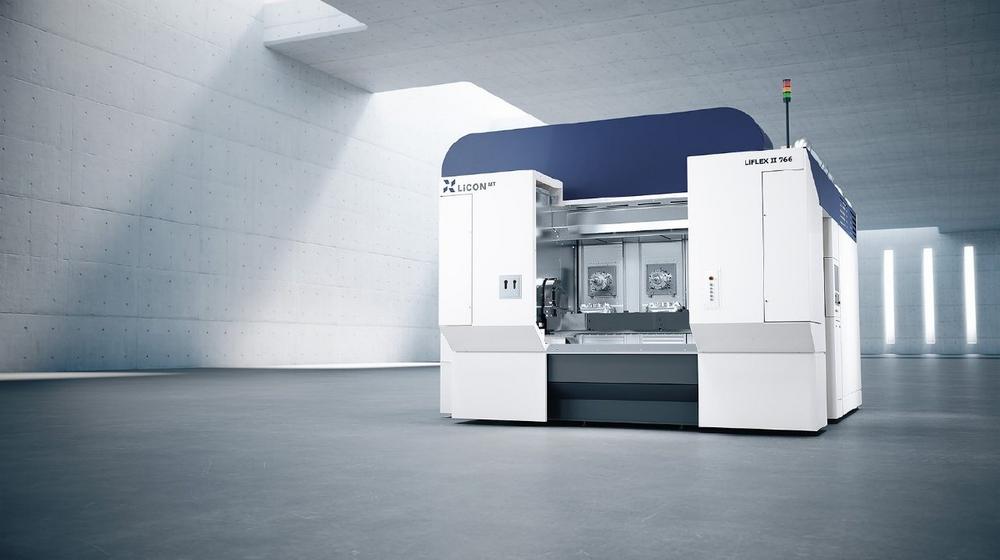
Twin-spindles for more competitiveness
For the enterprise Hengst Filtration, sustainability plays an important role. As a leading manufacturer of filtration solutions, this company not only produces parts which protect the environment and health, but also values ecological sustainability. In order to achieve this, Hengst is constantly looking for new solutions.
A recent application consisted of adding machining of new car and truck filter housings that had been die cast. Based on this, Hengst Filtration invested in two automated machining cells built by the machine builder LiCON from Laupheim in Baden-Württemberg. As a world-wide system supplier, LiCON provides highly efficient solutions ranging from individual machines to fully automated production lines. At the heart of the automated LiCON production cell at Hengst Filtration are five twin-spindle machines Type LiFLEX II 766, that were delivered production-ready to the facility in Nordwalde.
LiFLEX Twin-Spindle Machines have competitive advantages
In the larger cell, Hengst Filtration produces truck filters on three of the five LiFLEX twin-spindle machines. The other two LiFLEX twin-spindle machines produce car filters for a premium customer. With the decision to go with the LiCON twin-spindle machines and their advantages, Hengst ensures that they are both economical and sustainable.
Higher output per square meter
The installed twin-spindle machines, provide the same output as single-spindle machines, but require 40 % less floorspace. Therefore, the productivity per square meter is significantly improved. This was just one reason for the investment in LiCON twin-spindle machines.
Complete machining of the parts in one clamping
In the Hengst-Production line they had primarily used 4-axis single-spindle machines. For machining of five sides of the parts at least two clampings were needed. With the new LiCON 5-axis machines the parts could be completely machined in one clamping. This avoids re-clamping errors.
„For easy scalability it is important that the workpieces are completely machined in one machine. Based on this, every additional machine will expand capacity. With the LiCON machining centers, this succeeded not only with the car filter housings but also with the truck filter housings", raved project leader Hans-Joachim Daum, Industrial Engineer at Hengst Filtration.
„The cubic working envelope of the machining centers is designed with window fixtures in mind, so that five-sided machining is possible. Hengst Filtration really desired that the ramp-up time is optimized, so the customer initially purchased one machine per part type”, explained Nils Baumgartner, Key Account Manager at LiCON.
Minimal quantity lubrication replaces coolant and saves energy
Typically, emulsion had been used as the lubrication method, however in this case Minimum Quantity Lubrication (MQL) was installed. A tool-specific oil mist mixture is transported to the cutting edge through cooling channels in the tool. During the process development, the tool and process specific dosage parameters can be optimized and saved in the NC program. This ensures that the machined parts are “quasi-dry“ when they are removed from the machining center. The previous contamination of machine and the environment using coolant is avoided. The circulation of coolant via pumps and drive motors is eliminated which results in significant energy savings.
A LiFLEX twin-spindle machine requires approximately 15 Kilowatts for MQL. In comparison to using coolant in machining centers there are savings in electrical energy of at least 10 kWh per machining center. Over a year’s time of 5000 operating hours there are savings of 50,000 kWh per machining center and 250,000 kWh for all five machining centers.
Similar Technology for different workpieces thanks to modular loading systems
At Hengst Filtration two distinctly different size parts are machined using the same technology. On this basis, the machining of a large part and a small part on the same size machine was selected, however they are distinctly different in the loading concept. In this case, the modular LiCON concept is of benefit. The LiFLEX II 766 can be loaded three ways: direct load of the A-axis, double trunnion concept with two A-axes or a pallet changer. For machining of the large parts with their commensurate longer machining cycles, the LiFLEX II 766 i DL B2 direct load was chosen. For load and unload of the parts, the machine is idle. However, this operation is so small relative to the cycle time that a second set of clamping devices for loading parallel to the main time would not be worthwhile. Additionally, the added effort of monitoring part quality is reduced by 50 %.
For the smaller product used in cars there is a completely different scenario. Marco Gerhard, Industrial Engineer at Hengst Filtration, explains his project as follows: „Due to the smaller cubic size of the car housings, the cycle time is significantly shorter than of the truck filter housings, so that unloading/loading simultaneous to machining is the more economical solution of the three variations. Therefore, the pallet-changer version machining center was installed. In this machine it is even possible to mount two fixtures per spindle side. Therefore, two filter housings are machined per spindle, thus resulting in four completed parts per cycle. This improved the net cycle time per part by 15 %.“
Automation properly configured and still flexible
For machining of the large parts, three machining centers were installed. These were loaded via a robot mounted on a gantry, so that the parts would be loaded/unloaded from above. The LiCON designed gripper consisted of four grippers so that two finished parts would be unloaded and therefore two raw parts could be loaded by the robot in the same position. This ensures that the raw parts will be targeted properly in the fixtures. The machining of the smaller parts consists of two machining centers opposed to each other, with one robot being able to service both machines. In both production cells the raw parts are manually loaded onto a raw part conveyor. The buffer is large enough to allow for unattended operation during operator lunch breaks. „Flexibility is important. On that basis we also wanted access to the machines for manual loading. This allows us to process smaller lots of older designs, on one of the three twin-spindle machines. This makes the gantry robot a ‘good concept’", cited the Production Manager, Michael Cedrola.
Industry 4.0
Production systems with a high level of automation, as described here, allow for transparent data management. So all the parameters of this project can be observed per part type. Countless relevant data is transferred from the machining centers to a central data storage.
In addition to this, other sensor systems such as drill breakage monitoring as well as machining quality (as a function of vibrations) can be analyzed for further service requirements.
Single source integrated solutions
Alf Bönisch, the Team Leader of Industrial Engineering at Hengst Filtration, states that it is important that extensive projects like this should have as few points of contact as possible to ensure success. „LiCON supplies the entire installation as a turnkey-supplier including fixtures and automation. Therefore, responsibility is with one source.
The robot hand is very complex. It has four grippers: for holding two raw parts and two finished parts. For an effective interface to both fixtures, it was beneficial that both fixture and robot grippers were developed and built by the same supplier. To minimize the process development time, LiCON simulated the entire process virtually and qualified the system using simulation programs. This saved valuable time,“ explained Bönisch making the decision in favor of LiCON for this project.
FACTBOX HENGST Filtration
Hengst Filtration produces filter and components for various applications, primarily for the automobile industry, industrial applications and ventilation technology. In 2019 Hengst-Group employed more than 3,200 employees in 20 different locations and generated annual sales of 483 million Euro. It was founded as Ing. Walter Hengst KG in 1958 in Münster, Westphalia. At the beginning of 1988 the oil filter cannister with automatic drain system was introduced. Thereby followed numerous innovations such as metal-free filter inserts, fluid management modules and oil mist systems. The modular kit „Blue-Engine-Care-System (BECS)“ for engine optimization, the disc separator with electrical drive Blue.tron and the gas monitoring system Blue.max are proprietary developments of Hengst. In 1999 the globalization of the company began with continuous worldwide growth. The 2000s saw the acquisition of various enterprises so that Hengst Group is now active on all continents with its own development, production, and sales locations. More information at www.hengst.com
LiCON MT is a global system supplier of modular machining centers for high-precision production machining of complex parts. Its customers include all the world’s leading car manufacturers, their suppliers and an increasing number of companies from various industries. In addition to product development the core expertise of this technology leader is the very high machining expertise as well as in-house design and production of motor spindles. Additionally, system integration with customized adaptable automation concepts as well as software development using LiCON MT engineers: in times fragile relationships require larger vendor deliverables (single sourcing). With subsidiaries and service facilities in Europe, US and China, LiCON employs more than 200 people. More information at www.licon.com
Licon mt GmbH & Co. KG
Im Rißtal 1
88471 Laupheim
Telefon: +49 (7392) 962-0
Telefax: +49 (7392) 962-257
http://www.licon.com
Telefon: +49 (7392) 962-186
Fax: +49 (7392) 962-257
E-Mail: eva.richter@licon.com
