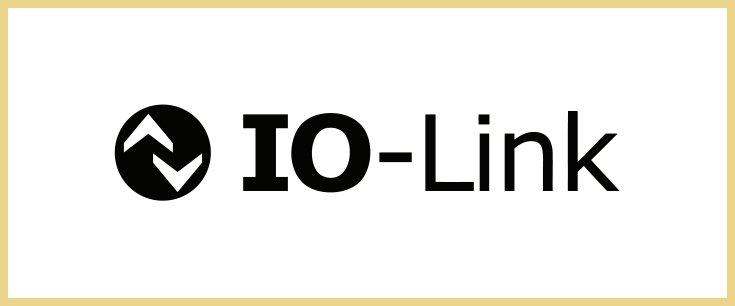
Inductive displacement transducers with IO-Link module IEIO25
With the use of low-cost 3-wire cables, sensors and actuators can be easily integrated into a control system ‚on the last few meters’ using decentralized IO-Link masters in a star topology. The IO-Link masters are then integrated into a higher-level bus system, such as PROFINET. This saves costs and is flexible, as it can be easily extended/modified. The input and output data of the peripheral sensors can be displayed and formatted in a user-friendly way using the IODD file. With IO-Link, sensor/actuator systems can therefore be quickly set up and put into operation. All necessary parameters can be automatically transferred for immediate operation in the event of a device replacement.
TWK now also offers IO-Link for its inductive displacement transducers. The modular design makes it possible to combine the actual transducer, which consists of a half-bridge coil system, with the new IEIO25 IO-Link electronics module. This module complements the range of IE25 electronics modules with SSI and CANopen interfaces. The proven IW10 (up to 8mm stroke), IW101 (up to 15mm) and IW120 (up to 200mm) models are available as displacement transducers. Due to the robust and encapsulated, yet lightweight construction of the coil system in a stainless-steel tube, the transducers have convincing technical values. Up to 0.25% linearity (model dependent), ambient temperature up to 100°C or shock resistance up to 2500 m/s². For optimum mounting, optional mechanical versions are available with spring and/or ball joints. An M8 connector cable is used for connection to the IEIO25 module, which can be a few meters away and communicates with the IO-Link master via the 3-wire cable with M12 connector.
The IEIO25 scans the coil system and transmits the position value via IO-Link with 12-bit resolution and a cycle time of less than 5 ms. This is important for real-time applications. The process data also includes bytes for the controller temperature and an error bit to indicate a device error. The controller can perform a position preset or load default values via the control byte (master output data). Object access can be used to parameterize or read out a wide range of customized data. For example, resolution, measuring range, installation data or the operating time. All common EMC industry standards are met to ensure trouble-free operation.
The next step will be an all-in-one device, where the electronics including the IO-Link interface are integrated in a displacement transducer with an outer diameter of only 25mm. This device will extend our proven IWx250-series.
Displacement transducers are used in a wide range of applications. They can be used to align work pieces or to check the accuracy of their dimensions. For example, transducers can be used for thickness control. They are also used to position and check punches in presses during the pressing process. Or for recording the current position of a linear (oscillating) machine carriage for x-ray sheet metal inspection. In this way, defects in the sheet can be precisely located even when the sheet is in motion.
TWK-ELEKTRONIK GmbH
Bismarckstraße 108
40210 Düsseldorf
Telefon: +49 (211) 96117-0
Telefax: +49 (211) 637705
http://www.twk.de
Marketing-Team
Telefon: +49 (211) 96117-0
E-Mail: info@twk.de

