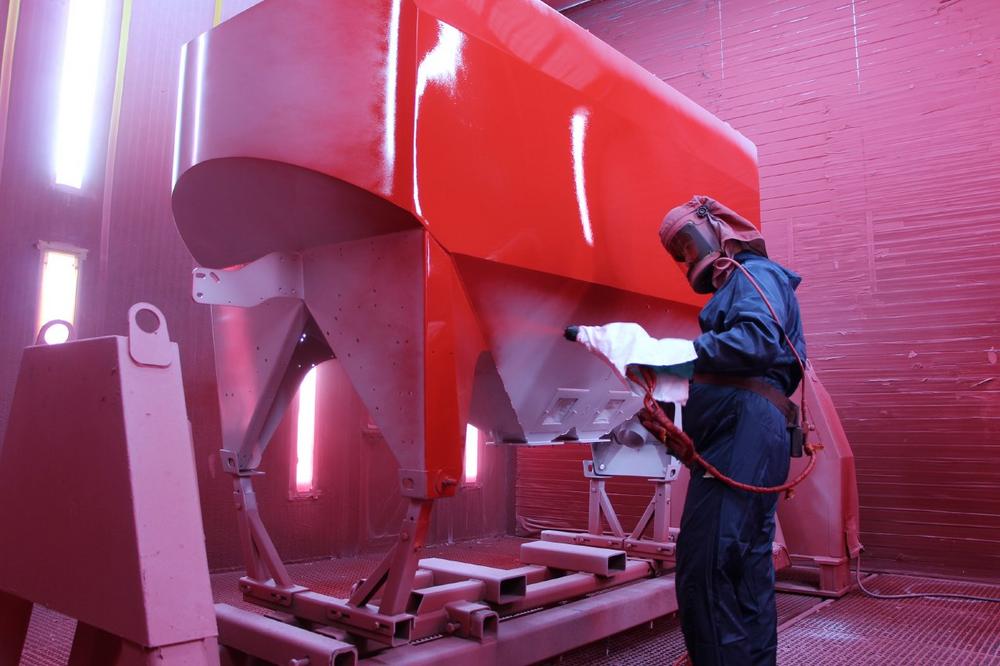
A UHS with the best properties
Disc harrows, cultivators, blade rollers – HORSCH manufactures a vast range of agricultural machinery. This company, based in the Upper Palatinate town of Schwandorf has been in business for almost forty years and first made a name for itself with its three-wheeled tractors and its minimum tillage implements. Today, HORSCH manufactures agricultural machinery as well as solutions for soil cultivation, seed and crop protection. In 2007, the company opened its first off-site production facility in Ronneburg: here in Thuringia, series products like the Pronto DC, the Terrano FX or the Joker CT/RT are produced. The plant has a large coating and assembly centre where two coating lines ensure high-quality and stable colour finishes.
More demanding requirements for surface finishes
HORSCH is one of the new providers of high-gloss surfaces with which the company hopes to satisfy the increasingly demanding requirements for the surface finishes of agricultural equipment. “Accordingly, coating is becoming a more significant issue in the agricultural machinery sector”, states Rudolf Obermeier, the senior supervisor in charge of surface coatings at HORSCH in Schwandorf. His move to HORSCH in 2015 coincided with the company’s latest agenda which was to optimise surface finishes. “The stability and edge coverage of the previous coating used by the company was no longer satisfactory. As well as a wide variety of frames and small parts, we also coat many large surfaces, tanks being just one example, and for this we need excellent and dependable spray mist absorption”, he explains. That was also a time when the sustainable reduction of VOC emissions was a priority.
Continuing successful collaboration
Before joining HORSCH, Obermeier had already been collaborating with paint manufacturer FreiLacke for many years. He brought the Black Forest coating manufacturer on board. FreiLacke then redesigned one of its UltraHighSolid systems for agricultural machinery, enabling emissions to be reduced significantly. After this promising and successful start, HORSCH decided to change over to a combination of the UR1937HRU735 and UR1409GH3307 systems from FreiLacke. Positive side effect: The Black Forest manufacturer’s system coating concept delivered conviction to the customer and was able to guarantee an identical shade of red – known as HORSCH Red – in both liquid and powder coating quality.
Challenge accepted
However, because a coating from the automotive sector had previously always provided a remarkably high-quality finish, the flow properties of the FreiLacke system have been closely scrutinised and questioned time and again, reports Stefan Kritzer, Sales Manager Vehicle Construction at coating manufacturer FreiLacke. As a consequence, the Black Forest company was called upon to improve it to the greatest possible extent. A challenge that the development and application technology teams at FreiLacke were delighted to accept. They optimised their formulations until the desired outcome was achieved. Obermeier and his team were delighted: “The flow improvement and a further reduction in solvent emissions have been impressively achieved with the UR1933HRU735 PU primer and the UR1447NH3307 PU top coat”. A successful large-scale trial was carried out in November 2020. Then, in February 2021, HORSCH switched to the new formulations.
Good flow, good application properties
The optimised coating structure is ideally suited for use on industrial goods and construction machinery of all kinds. Both components, i.e. primer and top coat, contain solvents and are based on a polyacrylate resin binder comprising cross-linked polyurethane and isocyanate. The top coat is available in a ’high gloss’ quality. In addition to the required high level of corrosion protection, this solvent-based primer offers good adhesion to various substrates – these include steel, blasted or iron-phosphated, as well as stainless steel. The corresponding UHS top coat, UR1447N, is characterised by good flow and application properties. Its processing window is max. two hours at 20°C after the addition of a curing agent. The solids volume after addition of a curing agent is 455 ml / kg (±10).
All-round positive conclusion
These new formulations have now been establishing a successful track record for more than two years. The production locations are highly satisfied and the environment also benefits from a substantial reduction in solvent emissions. In addition, the coating system has significantly shortened the cycle time: It is no coincidence that the HORSCH LEEB site in Landau an der Isar will also be switching to this tried and tested system from September 2023. And that applies to coated as well as powder-coated finishes: all of the agricultural equipment will gleam in the desired HORSCH red with a surface finish that equals an automotive finish in every respect.
Applied solutions.
FreiLacke has stood for innovative paints and coatings since 1926. The family business is now run by a third generation and, with a staff of more than 600 employees at its location in Döggingen in the Black Forest, it develops custom solutions for customers from the wheel and vehicle manufacturing industries, as well as those in the fields of mechanical and apparatus engineering, job coating, rail vehicles, wind power, functional furniture, storage technology, construction and sanitation.
As a modern family-run company now in its third generation, the safeguarding of the head office is just as important as our worldwide sales and our international subsidiaries and partners.
The product range of Europe’s leading system coating provider covers the entire spectrum from industrial coatings, powder coatings and electro-deposition coatings to composite solutions.
International sales are handled by a global network of subsidiaries and partners around the world.
Environmental protection has always been a key priority for FreiLacke.
Therefore, the company makes every effort to develop environmentally friendly products, reduce emissions, packaging materials and waste and use resources sparingly.
In 2023, FreiLacke was awarded the Great Place to Work® certification as Best Employer in Manufacturing & Industry 2023 as well as Best Employer in Baden-Württemberg for its exceptional and attractive corporate culture.
In addition, after undergoing a Culture Audit, the company also earned the Great Start award for an outstanding apprenticeship programme.
For years, FreiLacke has placed a major emphasis on training the next generation of workers and apprentices make up 10% of its workforce.
FreiLacke | Emil Frei GmbH & Co. KG
Am Bahnhof 6
78199 Bräunlingen
Telefon: +49 (7707) 151-0
http://www.freilacke.de
Head of Marketing
Telefon: +49 (7707) 151-2270
E-Mail: o.zanner@freilacke.de

